Physical Vapor Deposition (PVD) is a sophisticated technique used to deposit thin films of material onto a substrate. The process involves converting a solid target material into a vapor phase, which then condenses onto the substrate to form a thin, durable, and often highly specialized coating. This method is widely used in industries requiring high-performance coatings, such as electronics, optics, and aerospace. The PVD process is carried out in a specialized chamber, which is a critical component of the system. The chamber operates under low pressure and controlled conditions to ensure the precise deposition of materials. Key elements of the PVD chamber include the process chamber, pumping system, and control electronics, all of which work in tandem to achieve the desired coating properties.
Key Points Explained:
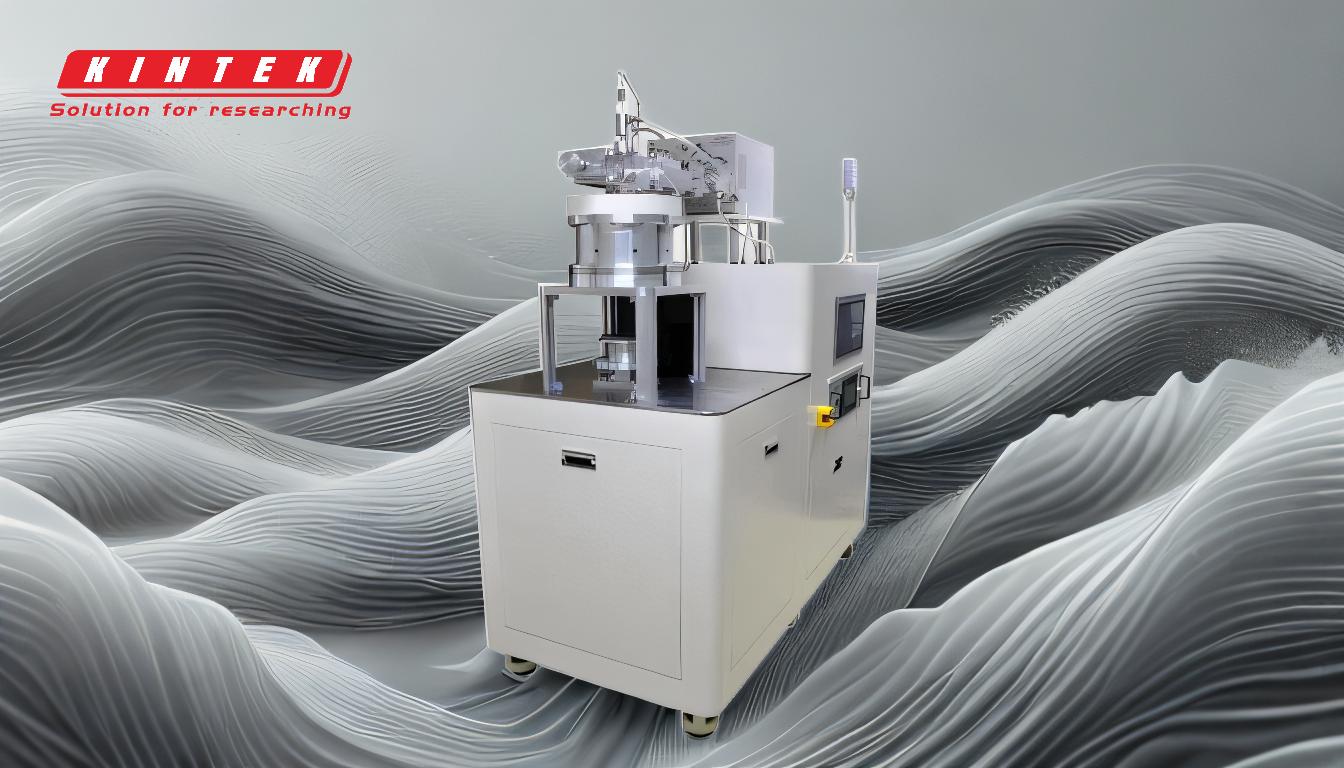
-
Conversion of Solid to Vapor Phase
- The PVD process begins with the conversion of a solid target material into a vapor phase. This is achieved through methods such as sputtering, thermal evaporation, or cathode arc.
- In sputtering, high-energy ions bombard the target material, dislodging atoms and converting them into a vapor.
- In thermal evaporation, the target material is heated to high temperatures until it vaporizes.
- The cathode arc method uses an electrical arc to vaporize the target material.
- The choice of method depends on the material properties and the desired coating characteristics.
-
Role of the PVD Chamber
- The PVD chamber is a vacuum-sealed environment where the deposition process occurs. It is designed to maintain low pressure, typically in the range of 10^-6 to 10^-3 Torr, to minimize contamination from background gases.
- The chamber houses the target material, substrate, and necessary components for vaporization and deposition.
- It is equipped with a pumping system to achieve and maintain the required vacuum levels. Larger chambers require higher-capacity pumping systems to ensure efficient operation.
-
Deposition Process
- Once the target material is vaporized, the atoms or ions travel through the chamber in a "line-of-sight" manner.
- The vaporized material condenses onto the substrate, forming a thin film. The thickness and uniformity of the film are controlled using a quartz crystal rate monitor.
- The substrate is often rotated or moved within the chamber to ensure even coating distribution.
-
Control Electronics and Process Regulation
- The PVD system is managed by sophisticated control electronics that regulate parameters such as temperature, pressure, and deposition rate.
- These controls ensure the process is stable, repeatable, and capable of producing coatings with precise properties.
- The electronics also monitor the condition of the chamber and pumping system, alerting operators to any deviations from the desired conditions.
-
Applications and Advantages of PVD
- PVD is used to create coatings that are highly durable, corrosion-resistant, and capable of withstanding extreme temperatures.
- Common applications include:
- Electronics: Thin films for semiconductors and microchips.
- Optics: Anti-reflective and protective coatings for lenses.
- Aerospace: Wear-resistant coatings for turbine blades and other components.
- The process allows for the deposition of nanosized films with exceptional precision, making it ideal for high-tech industries.
-
PVD Chamber Design Considerations
- The design of the PVD chamber must account for the specific requirements of the deposition process, including:
- Size and Geometry: Larger chambers can accommodate bigger substrates but require more powerful pumping systems.
- Material Compatibility: The chamber must be constructed from materials that can withstand high temperatures and corrosive environments.
- Temperature Control: The chamber operates at temperatures ranging from 50 to 600 degrees Celsius, depending on the process.
- Proper chamber design ensures efficient material utilization, minimal contamination, and consistent coating quality.
- The design of the PVD chamber must account for the specific requirements of the deposition process, including:
-
Comparison of PVD Methods
- Sputtering: Ideal for depositing metals, alloys, and ceramics. Provides excellent film uniformity and adhesion.
- Thermal Evaporation: Best for materials with low melting points. Offers high deposition rates but may result in less uniform coatings.
- Cathode Arc: Suitable for hard coatings like titanium nitride. Produces dense, high-quality films but may generate particulates.
In summary, the PVD chamber is the heart of the Physical Vapor Deposition process, enabling the precise and controlled deposition of thin films. By understanding the key components and processes involved, one can appreciate the complexity and versatility of this technology, which continues to play a vital role in advancing materials science and industrial applications.
Summary Table:
Aspect | Details |
---|---|
Process | Converts solid target material into vapor, condensing onto a substrate. |
Methods | Sputtering, thermal evaporation, cathode arc. |
Chamber Role | Vacuum-sealed environment for precise deposition. |
Key Components | Process chamber, pumping system, control electronics. |
Applications | Electronics, optics, aerospace, and more. |
Advantages | Durable, corrosion-resistant, high-precision coatings. |
Discover how PVD can enhance your industrial applications—contact our experts today!