A sealed quench furnace is a specialized piece of equipment used in heat treatment processes, particularly for hardening metals. It operates by heating the workpiece in a sealed environment to prevent oxidation, followed by rapid cooling (quenching) in a controlled atmosphere. This process ensures uniform heating and cooling, which is critical for achieving desired material properties such as hardness, strength, and durability. The furnace is designed to maintain high temperatures and precise control over the atmosphere, making it ideal for applications like carburizing, annealing, and tempering. Below, we’ll explore the key components and working principles of a sealed quench furnace in detail.
Key Points Explained:
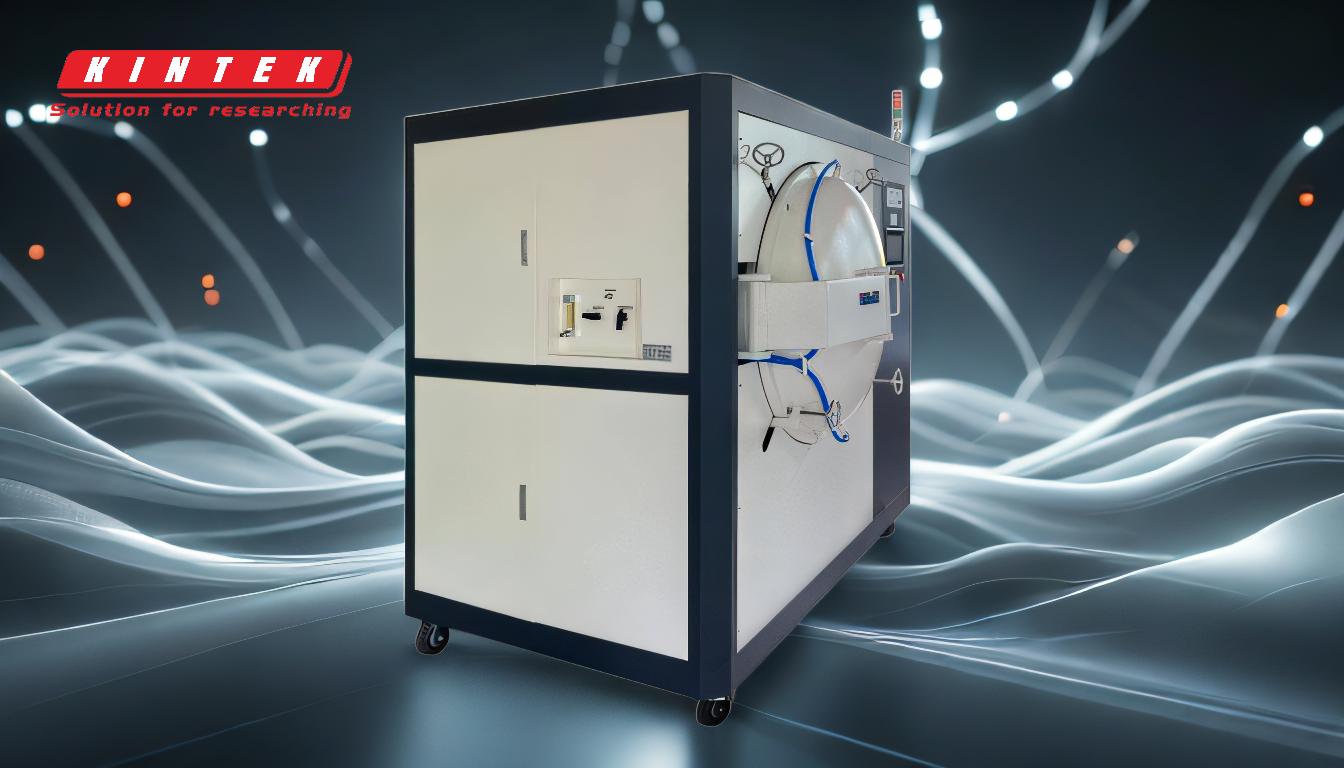
-
Sealed Environment for Controlled Atmosphere
- A sealed quench furnace operates in a closed system to prevent exposure to external air, which could cause oxidation or contamination of the workpiece.
- The sealed chamber is filled with an inert gas (e.g., nitrogen or argon) or a reactive gas (e.g., carbon-rich gas for carburizing) to create a controlled atmosphere.
- This controlled environment ensures consistent heat treatment results and prevents surface defects.
-
Heating Mechanism
- The furnace uses electric heating elements or gas burners to generate high temperatures, typically ranging from 800°C to 1200°C, depending on the application.
- The heating chamber is insulated with refractory materials to minimize heat loss and improve energy efficiency.
- The workpiece is placed inside the chamber and heated uniformly to the desired temperature.
-
Quenching Process
- After heating, the workpiece is rapidly cooled (quenched) to achieve the desired hardness and microstructure.
- The quenching chamber is integrated into the furnace design, allowing for a seamless transfer of the workpiece from the heating zone to the quenching zone.
- Quenching is typically done using oil, water, or polymer-based solutions, depending on the material and desired properties.
-
Automation and Precision Control
- Modern sealed quench furnaces are equipped with advanced control systems to monitor and regulate temperature, atmosphere composition, and quenching parameters.
- Automation ensures repeatability and consistency in heat treatment processes, which is critical for industrial applications.
- Sensors and feedback mechanisms provide real-time data to optimize the process and prevent defects.
-
Applications of Sealed Quench Furnaces
- These furnaces are widely used in industries such as automotive, aerospace, and tool manufacturing for processes like carburizing, hardening, and tempering.
- They are particularly effective for treating alloy steels, stainless steels, and other high-performance materials that require precise heat treatment.
- The sealed design makes them suitable for processing small to medium-sized components with complex geometries.
By combining a sealed environment, precise heating, and controlled quenching, sealed quench furnaces provide a reliable and efficient solution for achieving high-quality heat treatment results. Their ability to maintain consistent conditions throughout the process makes them indispensable in modern manufacturing.
Summary Table:
Key Feature | Description |
---|---|
Sealed Environment | Prevents oxidation and contamination using inert or reactive gases. |
Heating Mechanism | Uses electric or gas heating elements to reach 800°C–1200°C for uniform heating. |
Quenching Process | Rapid cooling in oil, water, or polymer solutions for desired hardness. |
Automation & Control | Advanced systems for precise temperature, atmosphere, and quenching control. |
Applications | Used in automotive, aerospace, and tool manufacturing for heat treatment. |
Discover how a sealed quench furnace can optimize your heat treatment processes—contact our experts today!