Sintering is a critical process in powder metallurgy and ceramics manufacturing, where powdered materials are transformed into dense, solid bodies through the application of heat and pressure, typically below the material's melting point. This process involves several stages, including the formation of a green part, removal of the bonding agent, and the actual sintering where particles fuse together. The sintering machine plays a vital role in controlling temperature, atmosphere, and pressure to ensure the desired material properties are achieved. Key components of the sintering process include raw materials like iron-containing powders, melting agents, and fuel, which must meet specific criteria for effective sintering.
Key Points Explained:
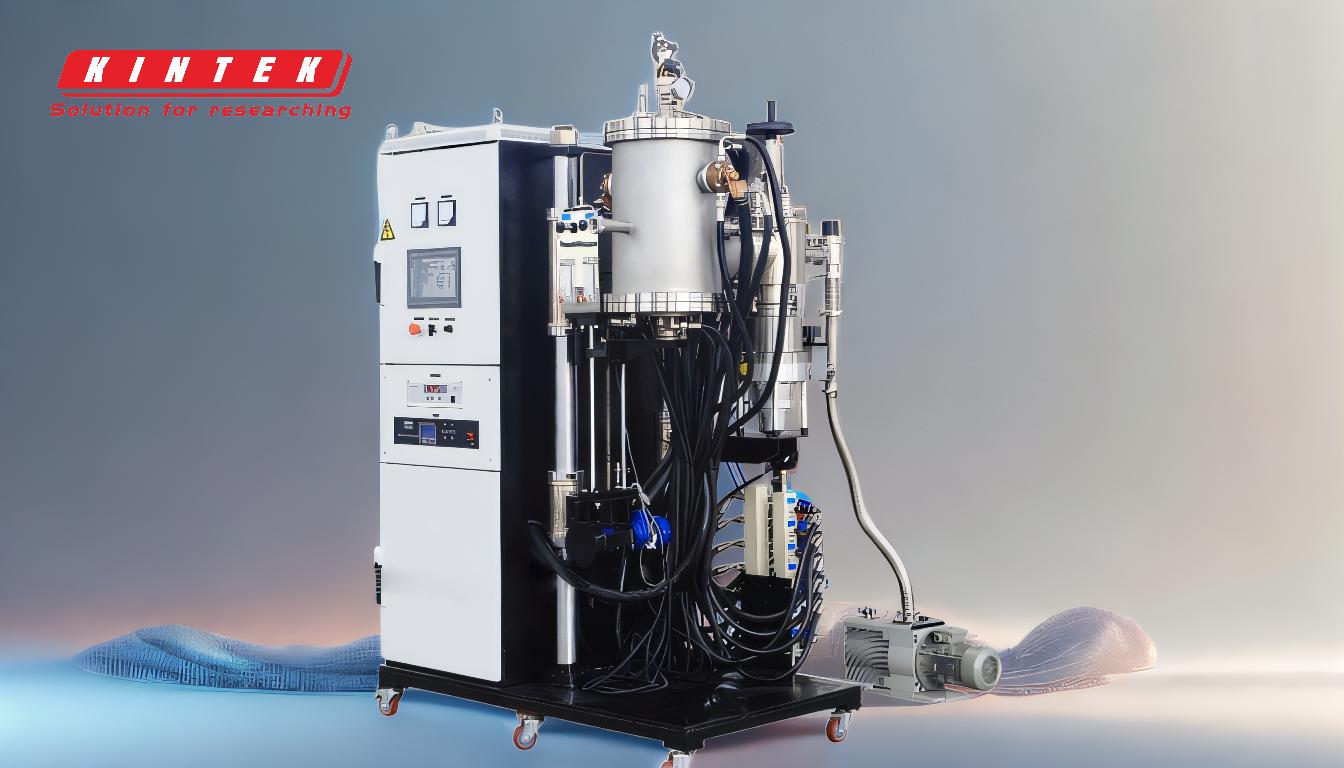
-
Definition and Purpose of Sintering:
- Sintering is a process that compacts and forms a solid mass of material by applying heat or pressure without reaching the material's melting point.
- It is used to create dense, high-strength materials from powdered forms, commonly in powder metallurgy and ceramics manufacturing.
-
Stages of the Sintering Process:
- Formation of the Green Part: A mixture of primary powder and a bonding agent (like wax or polymer) is shaped into the desired form.
- Removal of the Bonding Agent: During heating, the bonding agent evaporates or burns away.
- Sintering: The temperature is increased to a point where particles begin to fuse at their surfaces, either through partial melting or via an intermediate bonding agent.
-
Components of Sintering Raw Materials:
- Iron-containing Raw Materials: These include high iron content ore powder, iron concentrate, and other iron-rich materials.
- Melting Agents: These must have high valid CaO content, low impurities, and specific water content and particle size.
- Fuel: Typically includes coke powder and smokeless coal, which must have high fixed carbon content, low ash, and low sulfur content.
-
Key Steps in Sintering Operation:
- Cloth: Involves laying the bottom and mixing materials on the sintering machine.
- Ignition: The surface of the compartment on the trolley is ignited and maintained at a suitable high temperature.
- Sintering: Requires precise control of air volume, vacuum, layer thickness, speed, and the sintering endpoint to ensure optimal results.
-
Atmosphere Sintering Furnace:
- This type of furnace controls the atmosphere (such as nitrogen or argon) to optimize the sintering environment.
- It includes heating devices, pressure mechanisms, sintering chambers, and gas control systems.
- The controlled atmosphere allows for material migration, grain boundary movement, pore elimination, and shrinkage, resulting in a dense ceramic body with specific strength properties.
-
Benefits of Sintering:
- Produces materials with enhanced mechanical properties, such as increased strength and durability.
- Allows for the creation of complex shapes and structures that would be difficult to achieve through traditional melting and casting processes.
- Suitable for materials with extremely high melting points, like tungsten and molybdenum.
By understanding these key points, one can appreciate the complexity and precision required in the sintering process, as well as the critical role that sintering machines play in achieving the desired material properties.
Summary Table:
Aspect | Details |
---|---|
Definition | Compacting powdered materials using heat/pressure below melting point. |
Stages | Green part formation, bonding agent removal, and particle fusion. |
Key Components | Iron-containing powders, melting agents, and fuel. |
Sintering Operation | Cloth, ignition, and precise control of air, vacuum, and temperature. |
Atmosphere Sintering | Controlled environment for material migration, pore elimination, and shrinkage. |
Benefits | Enhanced strength, complex shapes, and suitability for high-melting materials. |
Learn how sintering can transform your manufacturing process—contact our experts today!