A vacuum brazing furnace is a specialized piece of equipment used to join metals by heating them to high temperatures in a vacuum environment, which prevents oxidation and contamination. The furnace operates by removing oxygen from the chamber, allowing the metals to bond without forming oxide layers. It features precise temperature control, uniformity, and sophisticated programming to ensure consistent results. The process is widely used in industries like aerospace, metallurgy, and particle physics, where high-quality, contamination-free joints are critical. The furnace's ability to handle multiple loads and larger workpieces makes it versatile and efficient for various applications.
Key Points Explained:
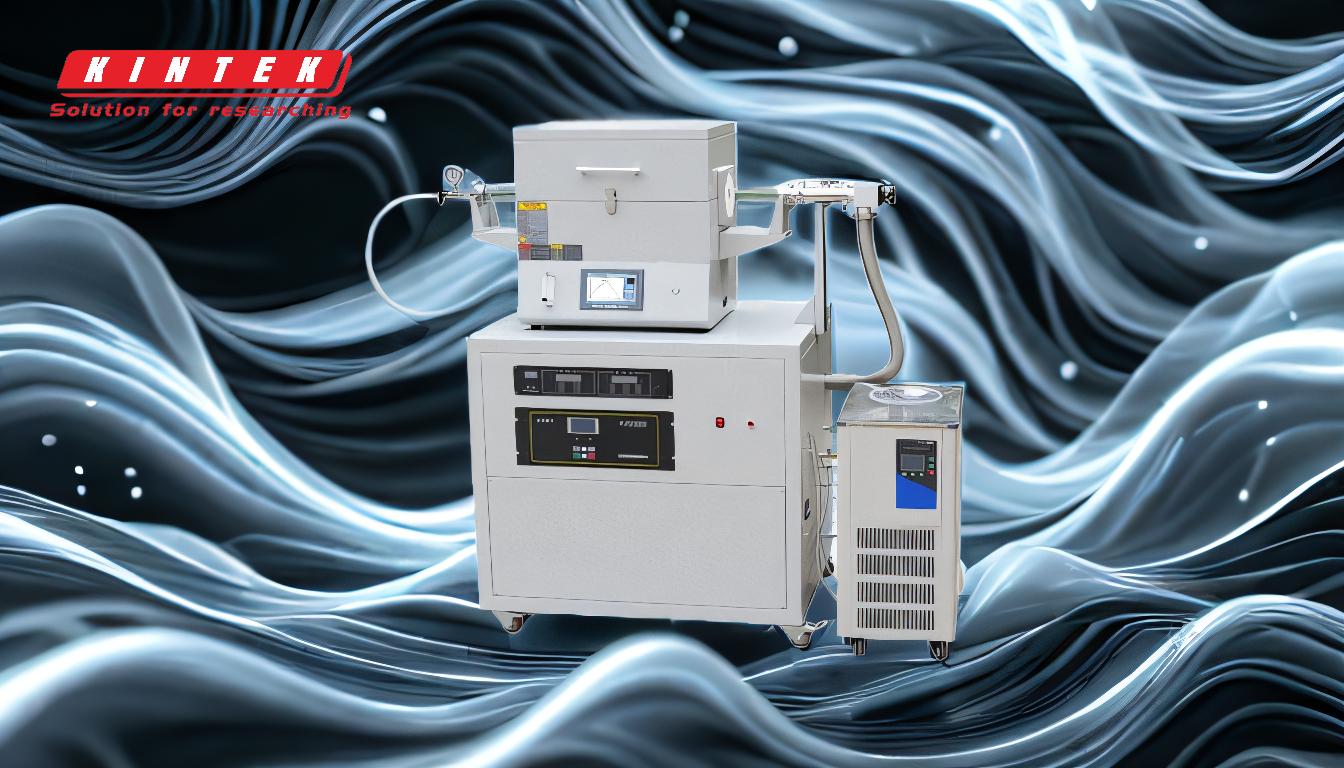
-
Vacuum Environment Creation:
- The vacuum brazing furnace removes oxygen from the heating chamber using a vacuum system. This step is crucial to prevent oxidation and contamination of the metals during the brazing process. The vacuum system typically includes mechanical and diffusion pumps to achieve the required vacuum level.
-
Heating System and Temperature Control:
- The furnace's heating system raises the temperature of the workpiece to the melting point of the filler metal. The temperature is carefully controlled using advanced programming and sensors to ensure uniformity and precision. This prevents overheating or underheating, which could compromise the quality of the brazed joint.
-
Brazing Process Steps:
- The process begins by placing the assembled workpiece into the vacuum chamber. The vacuum system is activated to remove air, and the heating system gradually raises the temperature to melt the filler metal. Once the brazing is complete, the workpiece is cooled in a controlled manner to avoid oxidation upon exposure to air.
-
Applications and Industries:
- Vacuum brazing furnaces are used in industries that require high-strength, contamination-free joints, such as aerospace, particle physics, and metallurgical research. They are also designed to meet stringent standards like NADCAP, ensuring reliability and precision for critical applications.
-
Advantages of Vacuum Brazing:
- The vacuum environment eliminates the need for flux, reducing contamination and post-brazing cleaning. It also ensures uniform heating, which is essential for brazing complex or large workpieces. The ability to program specific heating cycles for different materials and parts enhances flexibility and repeatability.
-
Comparison with Other Furnaces:
- Unlike a vacuum sintering furnace, which uses hydrogen for protection and induction heating, a vacuum brazing furnace relies solely on the vacuum environment and precise temperature control. Similarly, a vacuum hot press furnace combines pressure with heat, whereas a vacuum brazing furnace focuses on achieving contamination-free joints through controlled heating.
-
Quality Inspection:
- After the brazing process, the workpiece is inspected for quality to ensure the joint meets the required standards. This step is critical in industries like aerospace, where even minor defects can have significant consequences.
By combining precise temperature control, a contamination-free environment, and advanced programming, a vacuum brazing furnace delivers high-quality, reliable results for a wide range of industrial applications.
Summary Table:
Key Aspect | Details |
---|---|
Vacuum Environment | Removes oxygen to prevent oxidation and contamination. |
Heating System | Precise temperature control for uniform heating and reliable results. |
Brazing Process | Controlled heating and cooling to ensure high-quality, contamination-free joints. |
Applications | Aerospace, particle physics, metallurgy, and other high-precision industries. |
Advantages | No flux required, uniform heating, and programmable heating cycles. |
Quality Inspection | Ensures joints meet stringent industry standards. |
Discover how a vacuum brazing furnace can enhance your metal joining process—contact our experts today!