A vacuum induction furnace is a specialized piece of equipment used for melting and processing metals in a vacuum or controlled atmosphere environment. It operates by using electromagnetic induction to generate heat within a metal crucible, which melts the metal charge. The vacuum environment prevents oxidation and contamination, making it ideal for processing high-purity metals and alloys. This furnace is widely used in industries such as aerospace, automotive, and materials research for producing advanced materials like nickel-based alloys, titanium alloys, and rare earth metals. The process involves electromagnetic stirring, which ensures uniform composition and refining of the molten metal.
Key Points Explained:
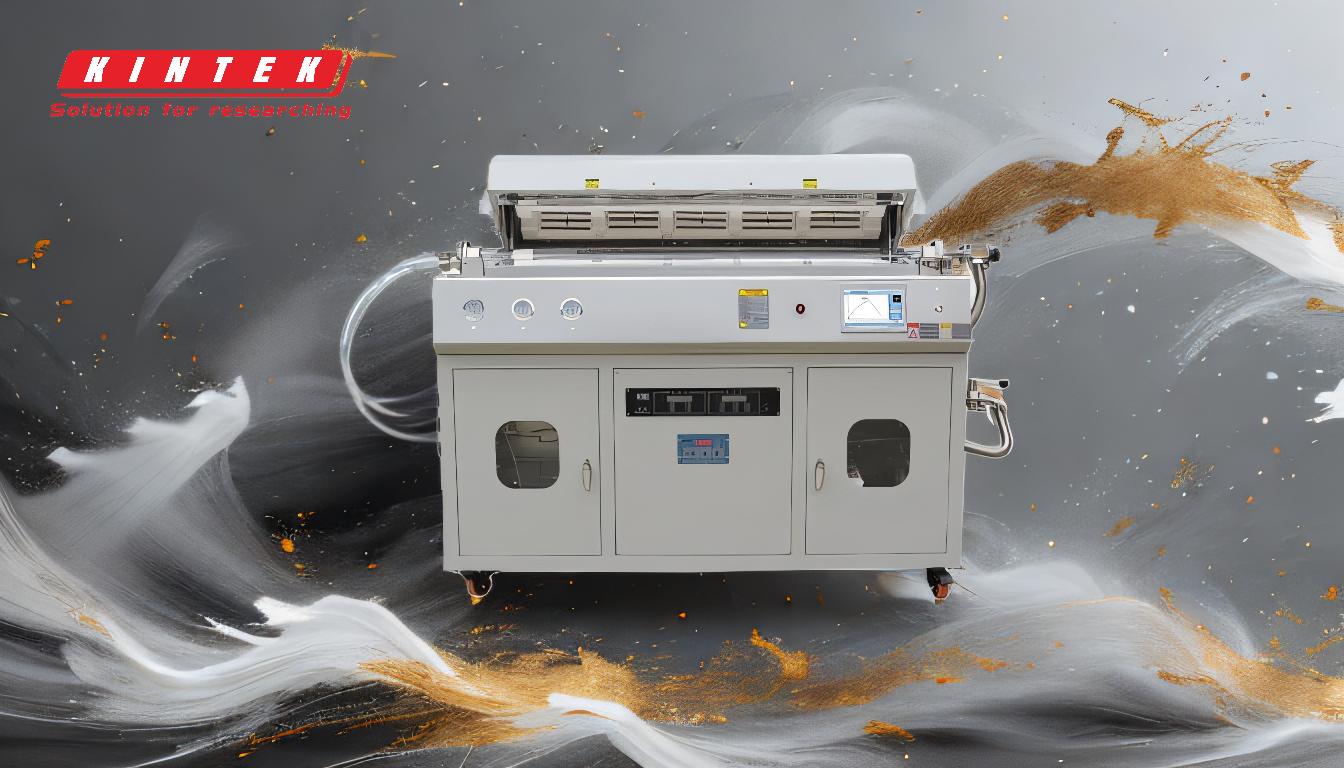
-
Working Principle of a Vacuum Induction Furnace:
- The furnace operates by inducing eddy currents in the metal charge using a water-cooled induction coil. When alternating current flows through the coil, it generates a magnetic field that induces currents in the metal, causing it to heat up and eventually melt.
- The vacuum environment is crucial as it removes gases and impurities, ensuring high-purity melting and refining of metals. This is particularly important for materials sensitive to oxidation or contamination, such as titanium and nickel-based alloys.
-
Key Components:
- Airtight Steel Jacket: The furnace is enclosed in a water-cooled steel jacket that maintains the vacuum and withstands high temperatures.
- Crucible: Made of refractory materials, the crucible holds the metal charge and is surrounded by the induction coil.
- Induction Coil: This water-cooled coil generates the electromagnetic field required for induction heating.
- Vacuum System: A vacuum pump and associated equipment maintain the low-pressure environment inside the furnace.
- Control Systems: These regulate temperature, pressure, and other parameters to ensure precise control over the melting process.
-
Applications:
- High-Purity Metals: The furnace is used for melting and casting metals like titanium, nickel, and cobalt alloys, which require a contamination-free environment.
- Rare Earth Metals: It is also suitable for processing rare earth metals and hydrogen storage materials, which are sensitive to atmospheric gases.
- Research and Development: The furnace is widely used in scientific research for developing new materials and alloys with specific properties.
-
Advantages of Vacuum Induction Melting:
- Contamination-Free Melting: The vacuum environment prevents oxidation and removes impurities, ensuring high-quality metal production.
- Electromagnetic Stirring: The induced currents create a stirring effect, ensuring uniform composition and refining of the molten metal.
- Precision Control: Advanced control systems allow for precise regulation of temperature, pressure, and melting time, enabling the production of materials with consistent properties.
-
Comparison with Other Vacuum Furnaces:
- Unlike a vacuum hardening furnace, which is used for heat treatment, a vacuum induction furnace is specifically designed for melting and refining metals.
- A vacuum hot press furnace combines high temperature and pressure for sintering or phase transformation, whereas a vacuum induction furnace focuses solely on melting and refining.
-
Operational Considerations:
- Maintenance: Regular maintenance of the vacuum system, crucible, and induction coil is essential to ensure consistent performance.
- Safety: Proper handling of the vacuum environment and high temperatures is critical to prevent accidents and equipment damage.
- Energy Efficiency: The furnace's design minimizes heat loss, making it energy-efficient for high-temperature melting processes.
In summary, a vacuum induction furnace is a sophisticated tool for melting and refining metals in a contamination-free environment. Its ability to produce high-purity materials with precise control makes it indispensable in advanced manufacturing and research applications.
Summary Table:
Aspect | Details |
---|---|
Working Principle | Electromagnetic induction heats and melts metal in a vacuum environment. |
Key Components | Airtight steel jacket, crucible, induction coil, vacuum system, controls. |
Applications | High-purity metals, rare earth metals, R&D for advanced alloys. |
Advantages | Contamination-free melting, electromagnetic stirring, precision control. |
Operational Tips | Regular maintenance, safety protocols, energy-efficient design. |
Ready to enhance your metal processing capabilities? Contact us today to learn more about vacuum induction furnaces!