An induction heating system works by using electromagnetic induction to generate heat in conductive materials. The system consists of an alternating current (AC) power source, an induction coil, and the material to be heated. When AC flows through the coil, it creates an alternating magnetic field. This field induces eddy currents in the conductive material, which flow against the material's electrical resistance, generating heat through Joule heating. Additionally, in magnetic materials, hysteresis losses contribute to heating. The process is non-contact, efficient, and can be precisely controlled, making it ideal for applications like metal hardening, melting, and brazing.
Key Points Explained:
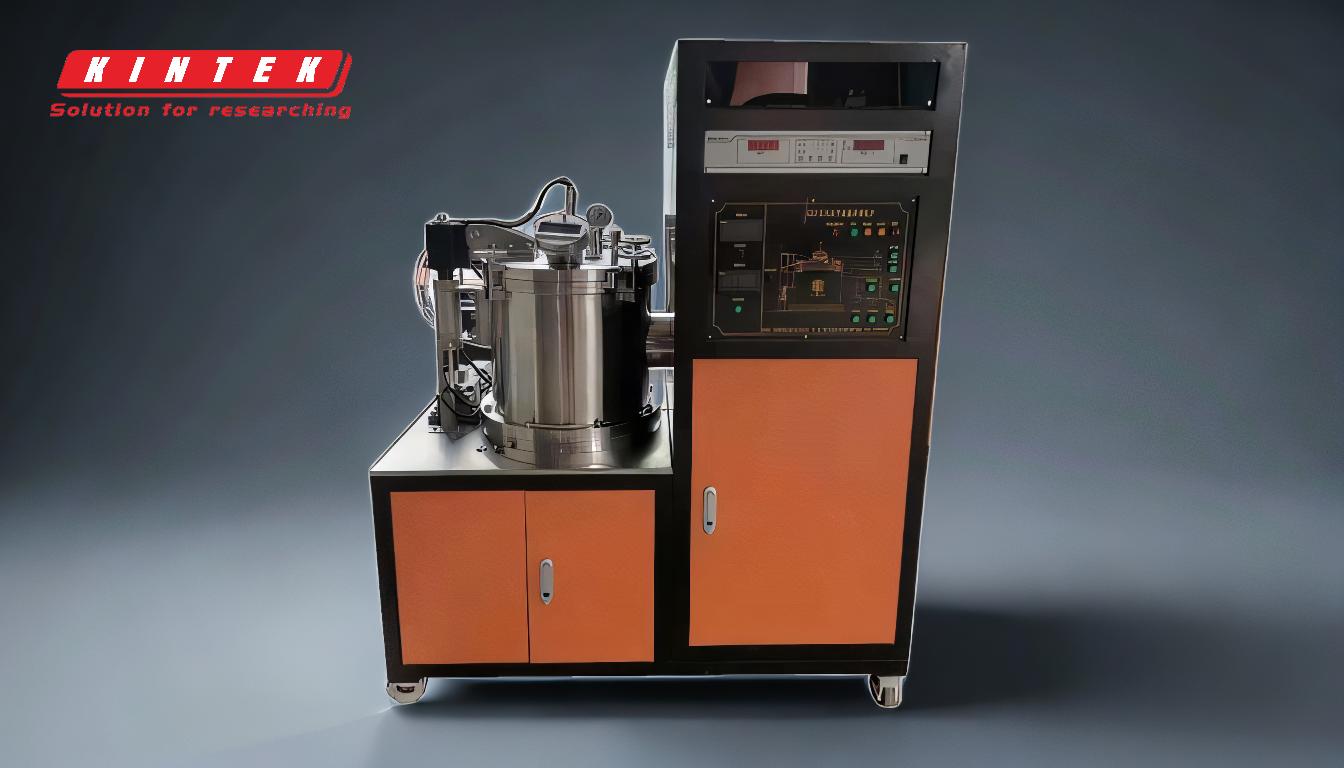
-
Electromagnetic Induction:
- The core principle of induction heating is electromagnetic induction. When an alternating current (AC) flows through an induction coil, it generates a rapidly alternating magnetic field around the coil.
- This magnetic field induces electric currents, known as eddy currents, in nearby conductive materials. The strength of these currents depends on the material's conductivity and the frequency of the AC.
-
Eddy Currents and Joule Heating:
- Eddy currents are circular electric currents induced within the conductive material by the alternating magnetic field.
- As these currents flow through the material, they encounter electrical resistance, which causes the material to heat up. This process is known as Joule heating or resistive heating.
- The amount of heat generated is proportional to the square of the current and the material's resistivity.
-
Hysteresis Losses (in Magnetic Materials):
- In ferromagnetic materials (like iron, nickel, and cobalt), the alternating magnetic field causes the magnetic domains within the material to continuously realign.
- This realignment generates heat due to internal friction, known as hysteresis losses. This effect is most significant at lower frequencies and diminishes at higher frequencies.
-
Components of an Induction Heating System:
- RF Power Supply: Provides the alternating current at the required frequency. The frequency can range from low (50-60 Hz) to high (several MHz), depending on the application.
- Induction Coil: Typically made of copper, the coil generates the alternating magnetic field. The design of the coil (shape, size, and number of turns) affects the heating pattern and efficiency.
- Workpiece: The conductive material to be heated. It must be placed within or near the coil to ensure effective induction heating.
- Chiller: Cools the induction coil and other components to prevent overheating during operation.
- Vacuum Unit (optional): Used in specialized applications (e.g., vacuum induction melting) to control the environment and prevent oxidation or contamination of the material.
-
Non-Contact Heating Process:
- Induction heating is a non-contact process, meaning the heat is generated directly within the material without physical contact between the coil and the workpiece.
- This eliminates contamination and allows for precise heating of specific areas, making it ideal for applications like localized hardening or brazing.
-
Advantages of Induction Heating:
- Efficiency: Heat is generated directly within the material, reducing energy loss compared to external heating methods.
- Speed: Rapid heating is possible due to the direct generation of heat within the material.
- Precision: The process can be finely controlled to heat specific areas or achieve uniform heating.
- Cleanliness: The non-contact nature prevents contamination, making it suitable for sensitive applications like food processing or semiconductor manufacturing.
-
Applications of Induction Heating:
- Metal Hardening: Used to strengthen the surface of metal parts by heating and then rapidly cooling them.
- Melting: Commonly used in foundries for melting metals in vacuum induction furnaces.
- Brazing and Soldering: Provides precise heating for joining metals without overheating the entire component.
- Cooking and Food Processing: Induction cooktops use this technology to heat cookware directly, offering faster and more efficient cooking.
-
Factors Influencing Induction Heating:
- Material Properties: The electrical conductivity and magnetic permeability of the material determine how effectively it can be heated.
- Frequency of AC: Higher frequencies are used for surface heating, while lower frequencies are better for deeper penetration.
- Coil Design: The geometry and placement of the coil affect the distribution and intensity of the magnetic field.
By understanding these key points, one can appreciate the versatility and efficiency of induction heating systems, which are widely used across industries for their precision, speed, and cleanliness.
Summary Table:
Key Aspect | Details |
---|---|
Core Principle | Electromagnetic induction generates eddy currents in conductive materials. |
Heating Mechanism | Joule heating (resistive heating) and hysteresis losses in magnetic materials. |
Components | RF power supply, induction coil, workpiece, chiller, and optional vacuum unit. |
Advantages | Efficiency, speed, precision, and cleanliness. |
Applications | Metal hardening, melting, brazing, soldering, and food processing. |
Influencing Factors | Material properties, AC frequency, and coil design. |
Ready to explore how induction heating can revolutionize your processes? Contact us today to learn more!