An induction melting furnace operates on the principle of electromagnetic induction, where electric energy is converted into heat energy to melt metals. The furnace consists of key components such as a power supply, induction coil, and a crucible made of refractory materials. The metal charge inside the crucible acts as a secondary winding of a transformer, and when an alternating current flows through the induction coil, it generates a magnetic field. This magnetic field induces eddy currents in the metal, producing heat and melting the metal. The process is efficient, energy-saving, and allows for precise temperature control, making it suitable for melting various metals, including steel, alloys, and non-ferrous metals.
Key Points Explained:
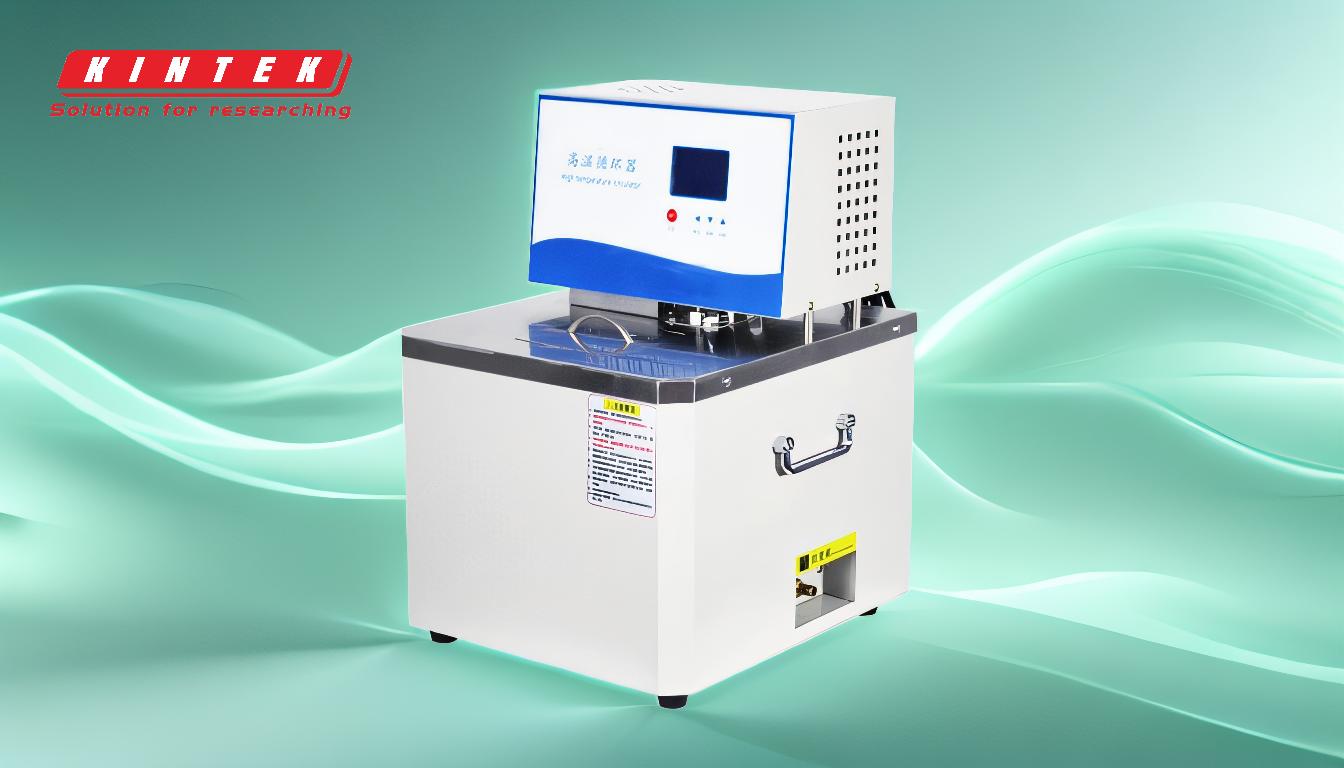
-
Principle of Electromagnetic Induction:
- The induction melting furnace works by transferring electric energy to the metal through electromagnetic induction. The alternating current in the induction coil creates a magnetic field, which induces eddy currents in the metal. These eddy currents generate heat, melting the metal without direct contact between the coil and the metal.
-
Key Components:
- Power Supply: Provides the alternating current necessary to generate the magnetic field.
- Induction Coil: A water-cooled copper coil that carries the alternating current and creates the magnetic field.
- Crucible: Made of refractory materials, it holds the metal charge and acts as the secondary winding of the transformer.
- Yokes: Protect the copper coil and help maintain the structural integrity of the furnace.
-
Process of Induction Melting:
- The metal charge is placed inside the crucible.
- An alternating current flows through the induction coil, creating a magnetic field.
- The magnetic field induces eddy currents in the metal, generating heat.
- The heat melts the metal, which can then undergo further processes like smelting, purifying, and casting.
-
Types of Induction Melting Furnaces:
- Standard Induction Melting Furnace: Used for melting metals like steel, alloys, and non-ferrous metals. It is compact, energy-efficient, and allows for quick melting and precise temperature control.
- Vacuum Induction Melting Furnace: Operates under vacuum conditions, making it suitable for melting high-purity metals and alloys, such as nickel-based alloys, special steel, and rare earth metals.
-
Applications:
- Industrial Use: Commonly used in foundries and metalworking industries for melting carbon steel, alloy steel, and non-ferrous metals like copper, aluminum, lead, and zinc.
- Scientific Research: Vacuum induction melting furnaces are used in research and production units for melting high-temperature alloys, precision alloys, and hydrogen storage materials under controlled atmospheres.
-
Advantages:
- Energy Efficiency: The direct transfer of energy to the metal reduces heat loss, making the process highly efficient.
- Precision: Allows for precise temperature control, which is crucial for producing high-quality metals.
- Compact Design: The furnace is lightweight and compact, making it suitable for various industrial and research applications.
- Versatility: Capable of melting a wide range of metals and alloys, making it a versatile tool in metallurgy.
By understanding these key points, one can appreciate the efficiency and versatility of induction melting furnaces in both industrial and scientific contexts.
Summary Table:
Aspect | Details |
---|---|
Principle | Electromagnetic induction transfers electric energy to heat and melt metals. |
Key Components | Power supply, induction coil, crucible, and yokes. |
Process | Alternating current creates a magnetic field, inducing eddy currents to generate heat. |
Types | Standard and vacuum induction melting furnaces. |
Applications | Industrial (steel, alloys, non-ferrous metals) and scientific research. |
Advantages | Energy-efficient, precise temperature control, compact, and versatile. |
Discover how an induction melting furnace can revolutionize your metalworking process—contact us today for expert advice!