Annealing is a heat treatment process that alters the physical and sometimes chemical properties of a metal to increase its ductility, reduce its hardness, and make it more workable. The process involves heating the metal to a specific temperature, holding it at that temperature for a certain period, and then cooling it at a controlled rate. This treatment results in significant changes in the metal's microstructure, which in turn affects its mechanical properties. The three primary stages of microstructural changes during annealing are recovery, recrystallization, and grain growth. Each stage plays a crucial role in determining the final properties of the metal, such as its strength, ductility, and toughness. Additionally, the specific requirements for the microstructure of a metal, such as stainless steel tubes, can vary depending on the intended application, leading to tailored annealing processes.
Key Points Explained:
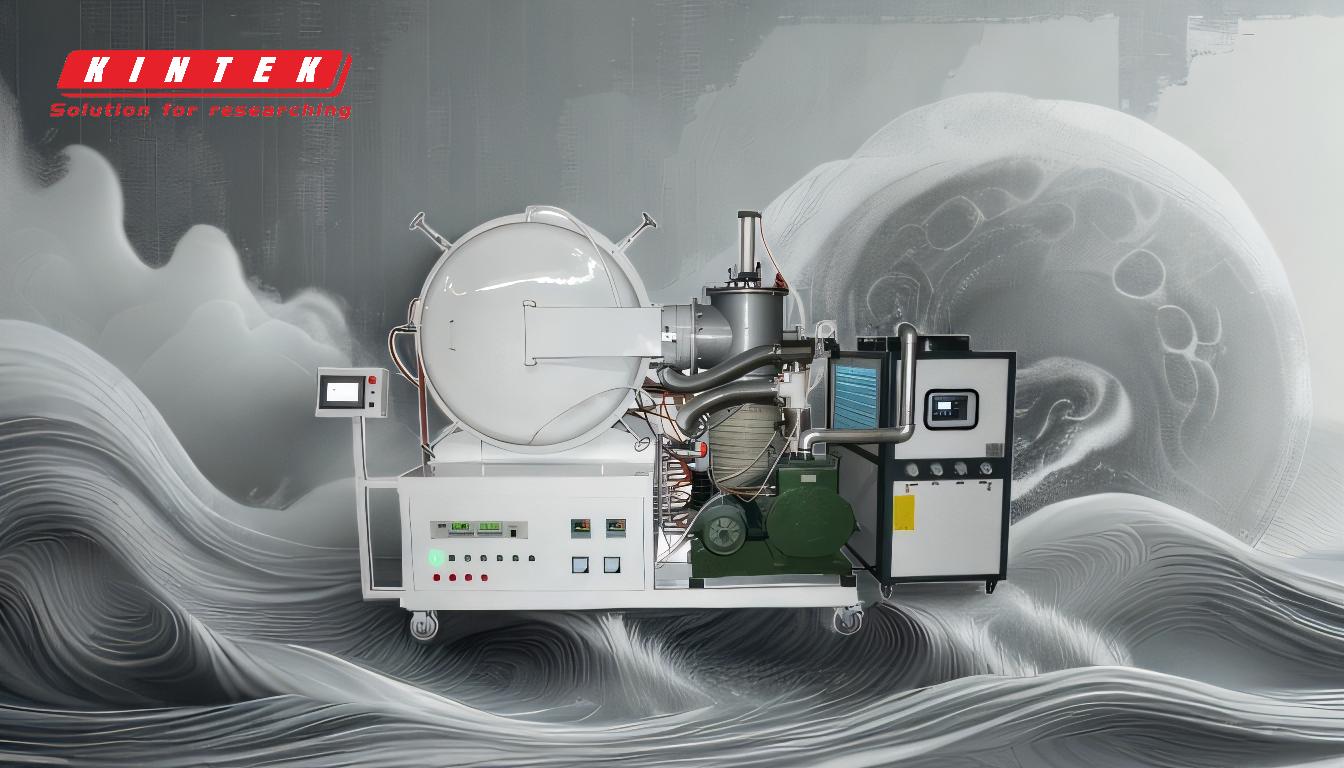
-
Recovery:
- Definition: Recovery is the first stage of annealing where the metal is heated to a temperature below its recrystallization point. During this stage, internal stresses are relieved, and dislocations within the metal's crystal structure begin to move and rearrange.
- Impact on Properties: This stage reduces the metal's internal stresses without significantly changing its microstructure. The metal becomes less brittle and more ductile, although the overall hardness remains relatively unchanged.
-
Recrystallization:
- Definition: Recrystallization occurs when the metal is heated above its recrystallization temperature. New, strain-free grains begin to form and grow, replacing the deformed grains that were present before annealing.
- Impact on Properties: This stage significantly reduces the metal's hardness and increases its ductility. The new grain structure is more uniform and free of defects, which improves the metal's overall workability and toughness.
-
Grain Growth:
- Definition: Grain growth is the final stage of annealing, where the newly formed grains continue to grow if the metal is held at the annealing temperature for an extended period. Larger grains tend to form at the expense of smaller ones.
- Impact on Properties: While grain growth can further reduce hardness and increase ductility, excessive grain growth can lead to a decrease in the metal's strength and toughness. Therefore, controlling the duration of this stage is crucial to achieving the desired mechanical properties.
-
Application-Specific Annealing:
- Variations in Process: The annealing process can be tailored to meet specific performance requirements. For example, in the case of stainless steel tubes, the bright annealing process is adjusted based on the desired microstructure for different applications.
- Impact on Microstructure: The requirements for the microstructure after bright annealing can vary significantly, leading to differences in the heat treatment process. This customization ensures that the final product meets the necessary mechanical and chemical properties for its intended use.
In summary, annealing is a critical heat treatment process that modifies the microstructure of metals, leading to changes in their mechanical properties. The stages of recovery, recrystallization, and grain growth each contribute to the final characteristics of the metal, such as increased ductility and reduced hardness. Additionally, the annealing process can be customized to meet specific performance requirements, ensuring that the metal achieves the desired properties for its intended application.
Summary Table:
Stage | Definition | Impact on Properties |
---|---|---|
Recovery | Heating below recrystallization temperature; relieves internal stresses. | Reduces brittleness, increases ductility; hardness remains unchanged. |
Recrystallization | Heating above recrystallization temperature; forms new, strain-free grains. | Reduces hardness, increases ductility; improves workability and toughness. |
Grain Growth | Extended heating; grains grow larger at the expense of smaller ones. | Further reduces hardness; excessive growth can decrease strength and toughness. |
Application-Specific | Tailored annealing for specific performance needs (e.g., stainless steel tubes). | Customizes microstructure for desired mechanical and chemical properties. |
Learn how annealing can optimize your metal's properties—contact our experts today for tailored solutions!