Brazing welding is a metal-joining process that involves melting a filler metal into a joint to bond two pieces of metal without melting the base metals. It is widely used in industries where strong, leak-proof, and precise joints are required. The process relies on capillary action to draw the molten filler metal into the joint, creating a strong bond upon cooling. Unlike welding, brazing does not melt the base metals, making it suitable for joining dissimilar metals and reducing the risk of warping or distortion. The process typically involves cleaning, assembly, heating, and post-brazing cleaning to ensure a high-quality joint.
Key Points Explained:
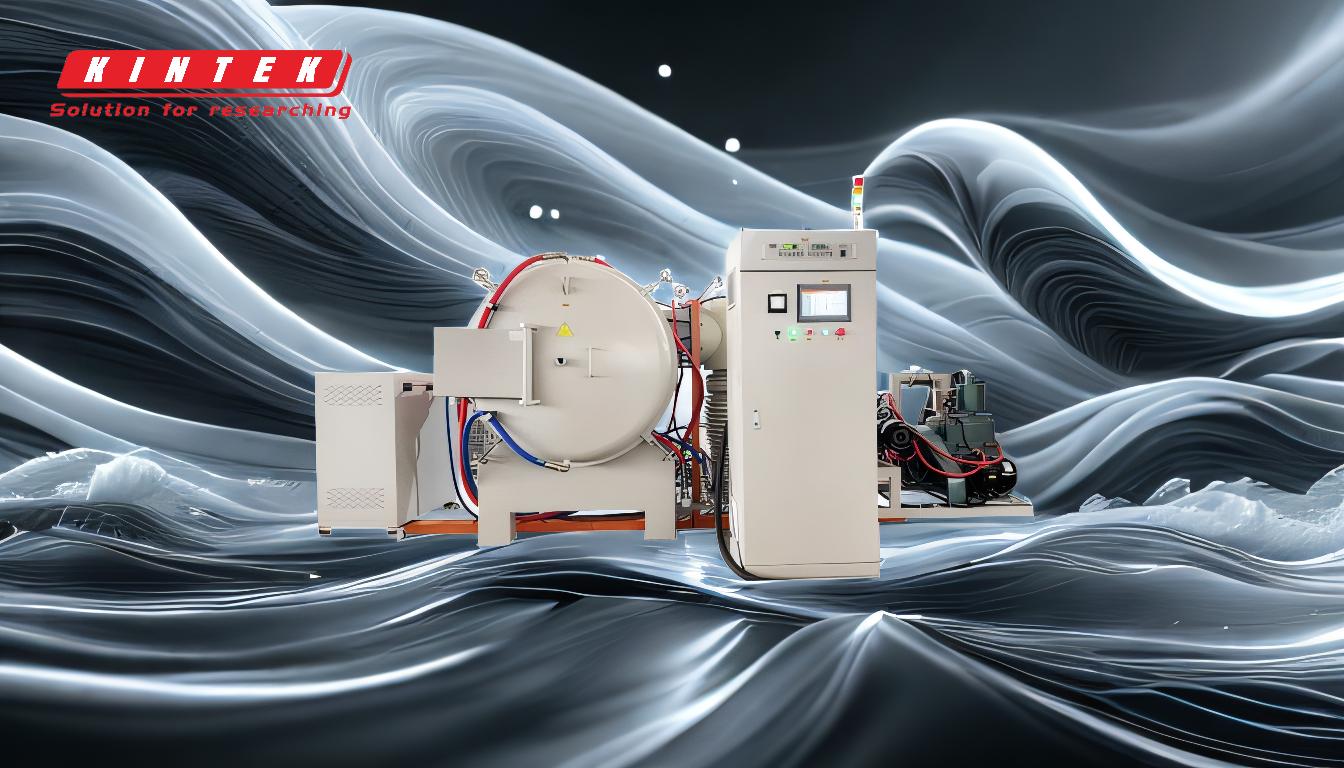
-
Understanding the Brazing Process
- Brazing involves heating a filler metal above its melting point (typically above 450°C or 840°F) and distributing it between two closely fitted metal parts using capillary action.
- The base metals do not melt, which allows for joining dissimilar materials like steel, copper, and aluminum.
- The filler metal must have a lower melting point than the base metals to ensure proper bonding without damaging the parts.
-
Key Steps in Brazing
- Joint Preparation: The joint must be designed with a precise gap width (usually 0.025–0.15 mm) to allow capillary action to draw the filler metal into the joint.
- Cleaning: The metal surfaces must be thoroughly cleaned to remove oxides, oils, and other contaminants that could interfere with the bonding process.
- Assembly: The parts are aligned and held in place using clamps, fixtures, or jigs to ensure proper alignment during heating.
- Heating: The assembly is heated in a furnace, torch, or induction heater to melt the filler metal. The heat source must provide uniform heating to avoid thermal stress.
- Cooling and Cleaning: After brazing, the assembly is cooled slowly to prevent cracking, and any residual flux or oxide is cleaned off.
-
Advantages of Brazing
- Strong Joints: Brazed joints are strong and can withstand high stress and vibration.
- Versatility: It can join dissimilar metals and complex geometries that are difficult to weld.
- Minimal Distortion: Since the base metals do not melt, there is less risk of warping or distortion.
- Leak-Proof Seals: Brazing creates leak-proof joints, making it ideal for applications like plumbing and refrigeration.
-
Applications of Brazing
- Brazing is used in industries such as automotive, aerospace, HVAC, and electronics.
- Common applications include joining heat exchangers, radiators, piping systems, and electrical components.
-
Comparison with Welding
- Welding involves melting the base metals to create a joint, which can lead to distortion and stress.
- Brazing is better suited for delicate or thin materials and dissimilar metals.
- Welding typically requires higher temperatures and more energy than brazing.
By following these steps and principles, brazing welding provides a reliable and efficient method for creating strong, durable joints in a wide range of applications.
Summary Table:
Aspect | Details |
---|---|
Process | Melting filler metal into a joint using capillary action, without melting base metals. |
Key Steps | Joint preparation, cleaning, assembly, heating, cooling, and post-brazing cleaning. |
Advantages | Strong joints, versatility, minimal distortion, leak-proof seals. |
Applications | Automotive, aerospace, HVAC, electronics, heat exchangers, piping systems. |
Comparison to Welding | Lower temperatures, less distortion, suitable for dissimilar metals. |
Discover how brazing welding can enhance your projects—contact us today for expert advice!