DC magnetron sputtering is a widely used physical vapor deposition (PVD) technique for creating thin films of materials onto substrates. It involves bombarding a target material with high-energy ions in a low-pressure gas environment, causing atoms to be ejected from the target surface and deposited onto a substrate. The process is enhanced by a magnetic field, which confines electrons near the target, increasing ionization and sputtering efficiency. This method is favored for its high deposition rates, good uniformity, and ability to produce high-quality coatings. However, it also has limitations, such as non-uniform target erosion. Below, the working principles, advantages, and challenges of DC magnetron sputtering are explained in detail.
Key Points Explained:
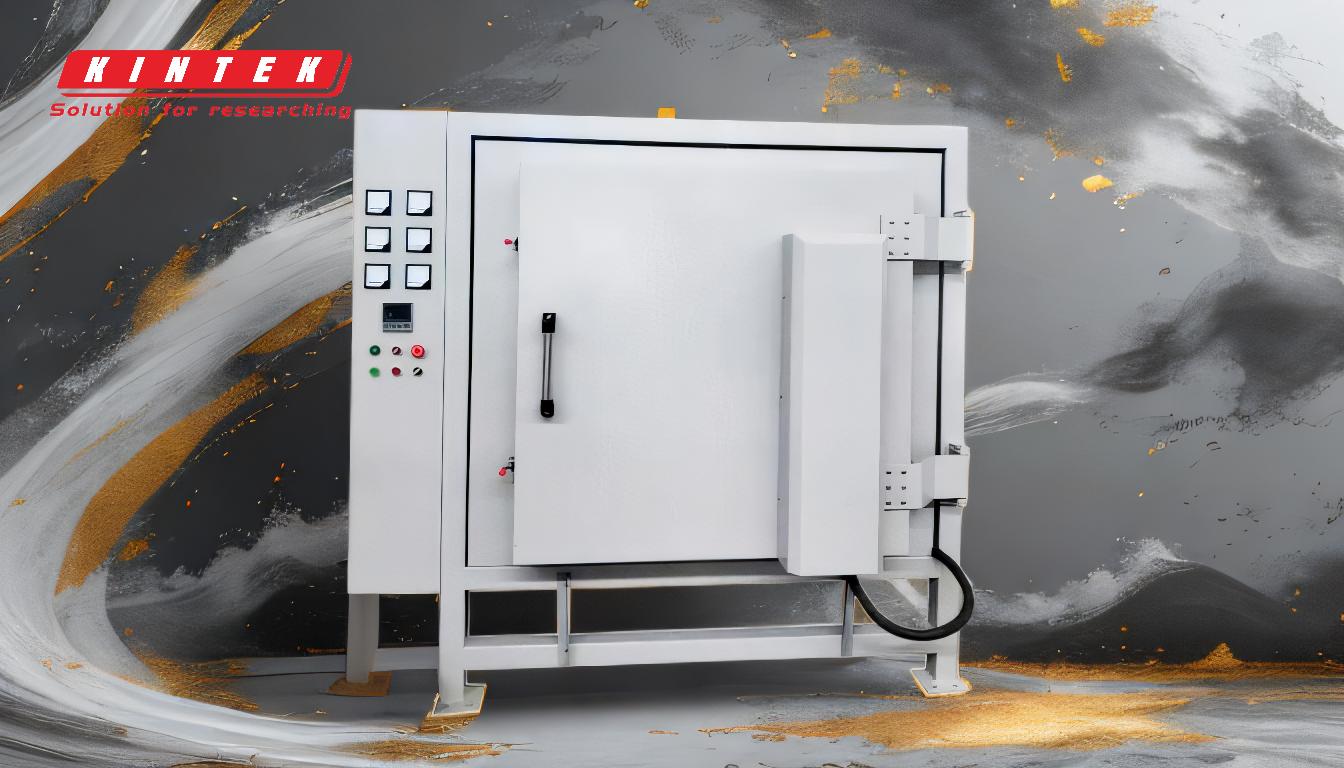
-
Basic Working Principle of DC Magnetron Sputtering
- The process begins with the creation of a plasma in a vacuum chamber filled with an inert gas, typically argon.
- A DC power supply applies a negative voltage to the target material (cathode), attracting positively charged argon ions.
- These ions bombard the target surface with high energy, causing atoms or molecules to be ejected (sputtered) from the target.
- The sputtered particles travel through the vacuum and deposit onto a substrate, forming a thin film.
-
Role of the Magnetic Field
- A magnetic field is applied near the target surface using a magnetron assembly.
- The magnetic field traps electrons in a circular trajectory, increasing their residence time in the plasma.
- This enhances collisions between electrons and argon atoms, increasing ionization and sustaining the plasma.
- The confined electrons also improve the sputtering rate by increasing the density of ions bombarding the target.
-
Advantages of DC Magnetron Sputtering
- High Deposition Rates: The magnetic field and efficient plasma generation allow for faster deposition compared to other sputtering methods.
- Good Uniformity and Step Coverage: The controlled sputtering process ensures even deposition on complex substrate geometries.
- Low Pressure Operation: The process can be conducted at lower pressures, reducing contamination and improving film quality.
- Versatility: Suitable for depositing a wide range of materials, including metals, ceramics, and alloys.
-
Challenges and Limitations
- Non-Uniform Target Erosion: The magnetic field creates a localized erosion pattern (race track) on the target, reducing its usable life.
- Heat Generation: The process can generate significant heat, requiring cooling systems to prevent damage to the target and substrate.
- Material Limitations: Some materials, such as insulators, are difficult to sputter using DC due to charge buildup on the target.
-
Applications of DC Magnetron Sputtering
- Widely used in the semiconductor industry for depositing conductive and dielectric layers.
- Applied in optical coatings for lenses, mirrors, and displays to enhance reflectivity or transparency.
- Utilized in the production of hard coatings for tools and wear-resistant surfaces.
- Employed in the fabrication of thin-film solar cells and energy storage devices.
-
Comparison with Other Sputtering Techniques
- DC vs. RF Magnetron Sputtering: DC is more suitable for conductive materials, while RF (radio frequency) sputtering is better for insulating materials.
- DC vs. Ion Beam Sputtering: DC magnetron sputtering offers higher deposition rates but less precise control over film properties compared to ion beam sputtering.
- DC vs. Diode Sputtering: Magnetron sputtering is more efficient and produces higher-quality films due to the magnetic field's role in enhancing plasma density.
-
Key Components of the DC Magnetron Sputtering System
- Vacuum Chamber: Maintains the low-pressure environment required for plasma generation.
- Target Material: The source of the sputtered atoms, typically made of the desired coating material.
- Substrate Holder: Holds the material onto which the thin film is deposited.
- Magnetron Assembly: Generates the magnetic field to confine electrons and enhance sputtering.
- DC Power Supply: Provides the voltage needed to create and sustain the plasma.
- Gas Inlet System: Introduces and controls the flow of inert gas (argon) into the chamber.
-
Process Optimization Considerations
- Gas Pressure: Optimal pressure ensures sufficient ionization while minimizing scattering of sputtered particles.
- Power Supply Settings: Adjusting voltage and current affects the sputtering rate and film quality.
- Substrate Temperature: Controlling temperature can influence film adhesion, stress, and microstructure.
- Target-Substrate Distance: Proper spacing ensures uniform deposition and minimizes defects.
In summary, DC magnetron sputtering is a versatile and efficient method for depositing thin films with high precision and uniformity. Its reliance on a magnetic field to enhance plasma generation and sputtering efficiency makes it a preferred choice in many industrial and scientific applications. However, challenges such as target erosion and heat management must be addressed to optimize the process for specific applications.
Summary Table:
Aspect | Details |
---|---|
Working Principle | High-energy ions bombard a target, ejecting atoms for thin film deposition. |
Role of Magnetic Field | Confines electrons, increasing ionization and sputtering efficiency. |
Advantages | High deposition rates, good uniformity, low pressure operation, versatility. |
Challenges | Non-uniform target erosion, heat generation, material limitations. |
Applications | Semiconductors, optical coatings, hard coatings, solar cells. |
Key Components | Vacuum chamber, target material, substrate holder, magnetron assembly. |
Discover how DC magnetron sputtering can enhance your thin film processes—contact our experts today!