Electron beam (e-beam) evaporation is a sophisticated thin-film deposition technique widely used in industries such as semiconductors, optics, and coatings. It involves using a focused electron beam to heat and evaporate a source material in a high-vacuum environment. The evaporated material then condenses onto a substrate, forming a thin, high-purity film. This method is particularly advantageous for materials with high melting points, offering superior material utilization, deposition rates, and step coverage compared to other techniques like sputtering or chemical vapor deposition (CVD). Additionally, e-beam evaporation can be enhanced with ion-assisted deposition (IAD) for improved film properties.
Key Points Explained:
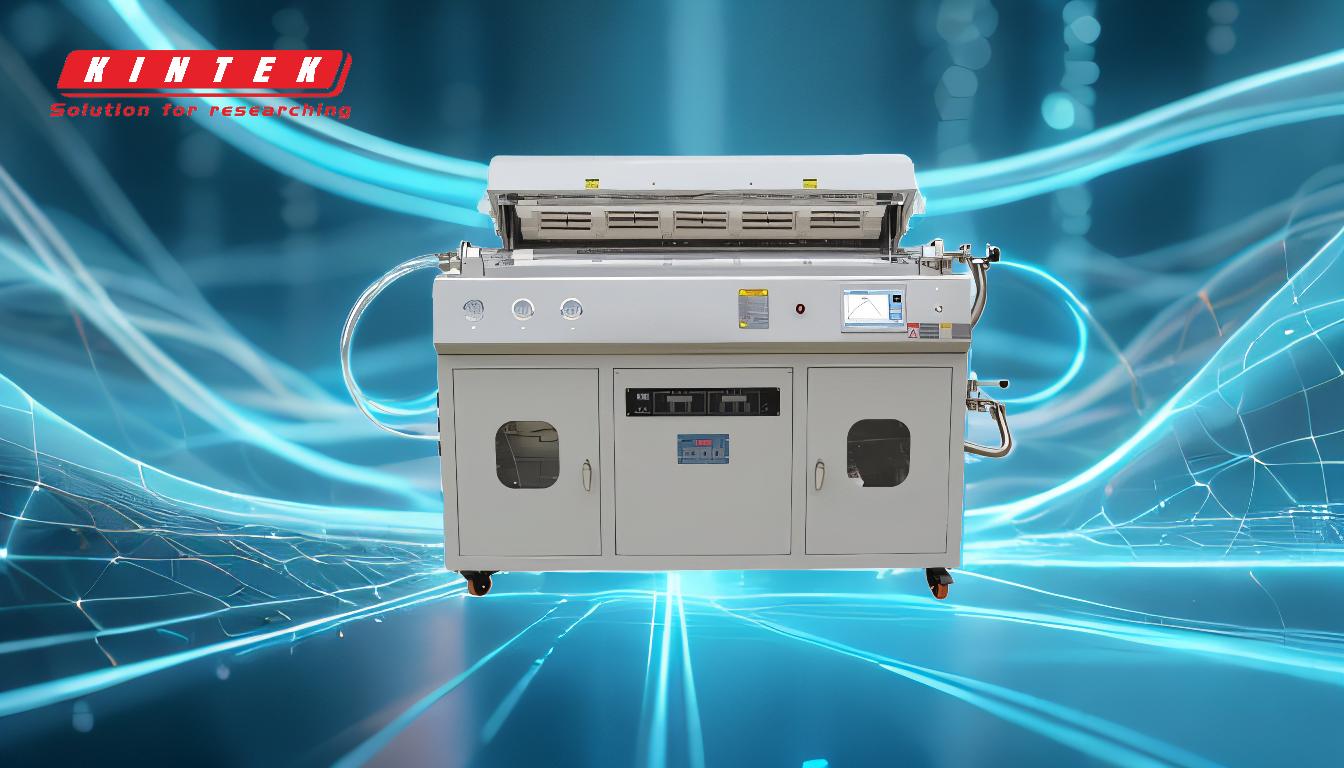
-
Electron Beam Generation and Focusing:
- The process begins with the generation of a high-energy electron beam, typically using a tungsten filament or other electron-emitting materials.
- The beam is focused and directed onto the source material using electromagnetic lenses and deflection systems. This ensures precise control over the heating process.
-
Heating and Evaporation of Source Material:
- The focused electron beam delivers intense localized heat to the source material, causing it to melt and evaporate.
- This method is particularly effective for materials with high melting points, such as refractory metals and ceramics, which are challenging to evaporate using conventional thermal methods.
-
Vacuum Environment:
- The entire process takes place in a high-vacuum chamber to minimize contamination and ensure the purity of the deposited film.
- The vacuum environment also allows for the efficient transport of evaporated particles to the substrate without interference from air molecules.
-
Deposition on Substrate:
- The evaporated material travels upwards in the vacuum chamber and condenses onto the substrate, forming a thin film.
- The substrate is typically positioned above the source material to facilitate uniform deposition.
-
Film Properties and Applications:
- E-beam evaporation produces films with excellent reflectivity, high purity, and precise thickness control (typically ranging from 5 to 250 nanometers).
- This technique is widely used in applications such as optical coatings, semiconductor devices, and protective coatings.
-
Advantages Over Other Deposition Methods:
- Higher Deposition Rates: E-beam evaporation offers faster deposition rates compared to sputtering.
- Better Material Utilization: The focused electron beam ensures efficient use of the source material, reducing waste.
- Superior Step Coverage: The process provides better coverage of complex geometries and features on the substrate.
- Compatibility with Ion-Assisted Deposition (IAD): An additional ion source can be used to pre-clean the substrate or enhance film properties during deposition.
-
Limitations and Considerations:
- The equipment and operational costs for e-beam evaporation are relatively high due to the need for a vacuum system and precise electron beam control.
- The process may not be suitable for materials that are sensitive to high-energy electron bombardment.
By leveraging the unique capabilities of e-beam evaporation, manufacturers can achieve high-performance thin films tailored to specific industrial needs.
Summary Table:
Aspect | Details |
---|---|
Process | Uses a focused electron beam to heat and evaporate source material in a vacuum. |
Key Features | High-purity films, precise thickness control, superior step coverage. |
Applications | Optical coatings, semiconductor devices, protective coatings. |
Advantages | Higher deposition rates, better material utilization, compatible with IAD. |
Limitations | High equipment costs, not suitable for electron-sensitive materials. |
Discover how e-beam evaporation can revolutionize your thin-film processes—contact our experts today!