Particle size plays a critical role in the pyrolysis process, influencing heat transfer, reaction rates, and the distribution of end products (gas, liquid, and solid). Smaller particles, typically up to 2 mm, enable faster and more uniform heat transfer, leading to quicker thermal decomposition and higher yields of pyrolysis oil. Larger particles, on the other hand, may result in uneven heating, slower reaction rates, and a greater proportion of solid char. The particle size also affects the residence time and the efficiency of the pyrolysis process, making it a key factor in optimizing the conversion of biomass or waste into valuable products.
Key Points Explained:
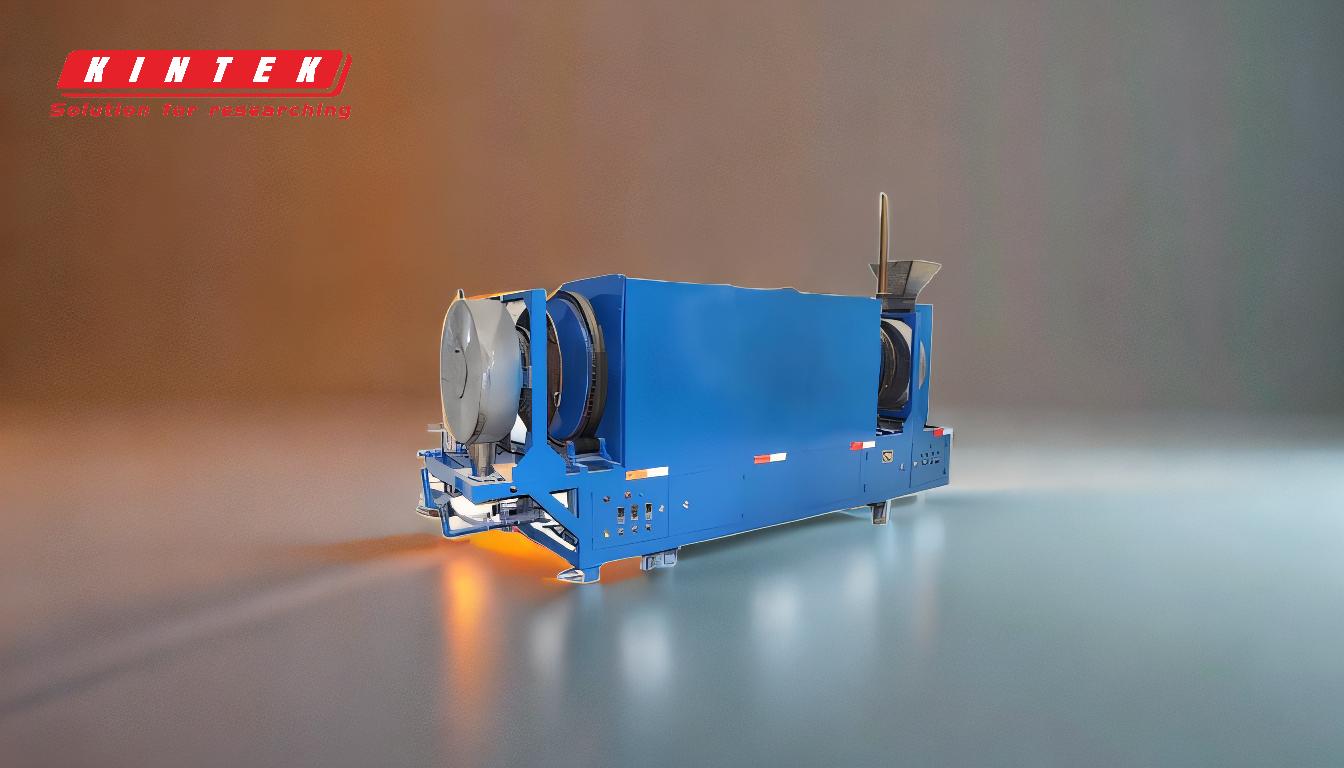
-
Heat Transfer Efficiency:
- Smaller particles (up to 2 mm) provide a larger surface area relative to their volume, allowing for rapid and uniform heat transfer throughout the material.
- This ensures that the entire particle reaches the required pyrolysis temperature quickly, minimizing the risk of incomplete decomposition.
- Larger particles may experience slower heat penetration, leading to uneven heating and potentially leaving the core of the particle under-processed.
-
Reaction Rates and Thermal Decomposition:
- Smaller particles decompose faster due to their increased surface area and efficient heat transfer.
- Faster decomposition leads to higher yields of pyrolysis oil, as the volatile compounds are released more quickly and efficiently.
- Larger particles decompose more slowly, which can result in a higher proportion of solid char due to incomplete pyrolysis.
-
Product Distribution:
- Smaller particles favor the production of pyrolysis oil and non-condensable gases, as the rapid decomposition releases more volatiles.
- Larger particles tend to produce more solid char, as the slower decomposition allows for greater carbonization of the material.
- The particle size also influences the quality of the solid residue, with smaller particles typically yielding a finer, more uniform char.
-
Residence Time:
- Smaller particles require shorter residence times in the pyrolysis chamber, as they decompose more quickly.
- This can improve the overall efficiency of the process, reducing energy consumption and increasing throughput.
- Larger particles may require longer residence times, which can lead to higher energy costs and lower process efficiency.
-
Process Optimization:
- Most pyrolysis technologies are designed to handle small particles (up to 2 mm) to maximize heat transfer and reaction rates.
- Pre-processing steps, such as shredding or grinding, are often necessary to reduce the particle size of the feedstock.
- The choice of particle size should be tailored to the specific pyrolysis technology and desired product distribution.
-
Feedstock Composition and Physical Structure:
- The particle size interacts with other factors, such as moisture content, temperature, and heating rate, to influence the pyrolysis process.
- For example, in biomass pyrolysis, smaller particles with low moisture content and high heating rates tend to produce more liquid and gas products.
- In waste pyrolysis (e.g., tires), the removal of reinforcing materials (e.g., steel and fibers) during shredding can also affect the particle size and pyrolysis outcomes.
-
Practical Considerations:
- Pre-processing to achieve the desired particle size can add to the overall cost and complexity of the pyrolysis process.
- The optimal particle size may vary depending on the type of feedstock (e.g., wood, agricultural waste, plastics) and the specific pyrolysis technology used.
- Balancing particle size with other process parameters (e.g., temperature, residence time) is essential for achieving the desired product yields and quality.
By carefully controlling the particle size of the feedstock, pyrolysis operators can optimize the process to maximize the production of desired products (oil, gas, or char) while minimizing energy consumption and processing time. This makes particle size a critical factor in the design and operation of pyrolysis systems.
Summary Table:
Aspect | Small Particles (≤2 mm) | Large Particles |
---|---|---|
Heat Transfer | Faster, uniform heat transfer | Slower, uneven heating |
Reaction Rates | Faster decomposition | Slower decomposition |
Product Distribution | Higher pyrolysis oil and gas yields | More solid char production |
Residence Time | Shorter residence time | Longer residence time |
Process Efficiency | Higher efficiency, lower energy consumption | Lower efficiency, higher energy costs |
Optimize your pyrolysis process with the right particle size—contact our experts today for tailored solutions!