Particle size plays a critical role in the sintering process, influencing the densification, mechanical properties, and overall quality of the final product. Smaller particles generally enhance sintering due to their higher surface energy and greater driving force for material transfer, leading to improved densification and reduced porosity. However, excessively fine particles can also pose challenges, such as agglomeration and difficulty in handling. The relationship between particle size and sintering is complex, involving factors like surface energy, diffusion rates, and grain growth. Understanding this relationship is essential for optimizing sintering conditions to achieve desired material properties.
Key Points Explained:
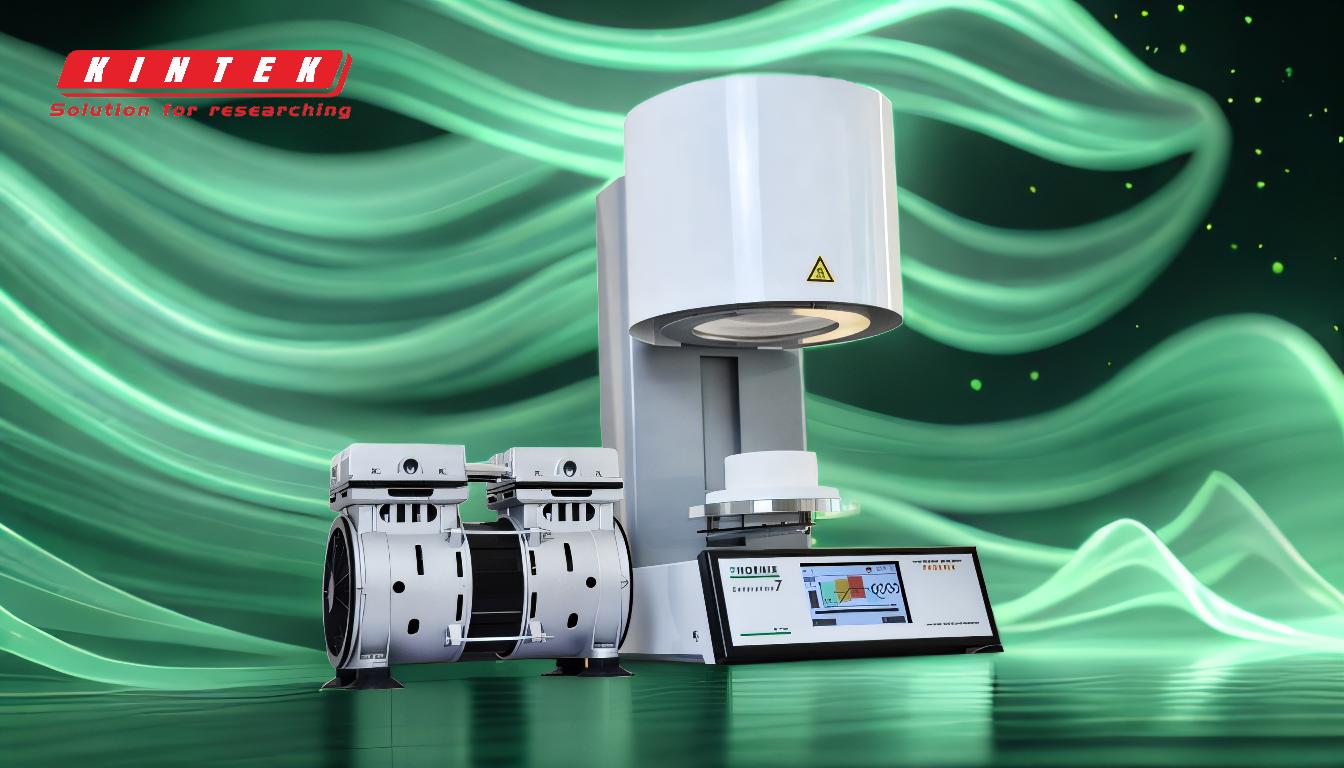
-
Surface Energy and Driving Force:
- Smaller particles have a higher surface-to-volume ratio, resulting in increased surface energy.
- This higher surface energy provides a greater driving force for material transfer during sintering, promoting densification.
- The increased surface energy also accelerates diffusion mechanisms, such as surface diffusion and grain boundary diffusion, which are critical for sintering.
-
Densification and Porosity:
- Smaller particles facilitate better particle packing, reducing the initial porosity of the green compact.
- During sintering, the enhanced material transfer mechanisms in fine particles lead to more effective pore elimination and densification.
- However, if the particles are too fine, they may agglomerate, leading to uneven densification and the formation of large pores.
-
Grain Growth:
- Fine particles tend to promote rapid grain growth during sintering due to their high surface energy and increased diffusion rates.
- While some grain growth is necessary for achieving strong interparticle bonds, excessive grain growth can degrade mechanical properties by creating large grains with weaker boundaries.
- Controlling particle size and sintering parameters is crucial to balance densification and grain growth.
-
Sintering Temperature and Time:
- Smaller particles require lower sintering temperatures and shorter times due to their higher reactivity and faster diffusion rates.
- This can lead to energy savings and improved process efficiency.
- However, care must be taken to avoid overheating, which can cause excessive grain growth or undesirable phase transformations.
-
Challenges with Fine Particles:
- Fine particles are more prone to agglomeration, which can hinder uniform compaction and lead to defects in the final product.
- Handling and processing fine powders can be challenging due to their increased surface area and reactivity, requiring specialized equipment and techniques.
- The increased surface area also makes fine particles more susceptible to contamination, which can affect sintering behavior and final properties.
-
Practical Applications:
- In ceramic technologies, fine-grained materials are often used to achieve high-density, high-strength products.
- In powder metallurgy, controlling particle size distribution is essential for producing components with precise dimensions and mechanical properties.
- Advanced sintering techniques, such as spark plasma sintering (SPS) and hot isostatic pressing (HIP), leverage the benefits of fine particles to achieve superior material properties.
In summary, particle size significantly impacts sintering by influencing surface energy, densification, grain growth, and overall material properties. While smaller particles generally enhance sintering, careful control of particle size and sintering parameters is necessary to optimize the process and achieve the desired outcomes. Understanding these relationships is crucial for material scientists and engineers working in fields such as ceramics, powder metallurgy, and advanced manufacturing.
Summary Table:
Aspect | Impact of Smaller Particles | Challenges |
---|---|---|
Surface Energy | Higher surface-to-volume ratio increases surface energy and driving force for material transfer | Agglomeration risks and handling difficulties |
Densification | Better particle packing and pore elimination, leading to improved densification | Uneven densification if particles agglomerate |
Grain Growth | Promotes rapid grain growth, enhancing interparticle bonds | Excessive grain growth can weaken mechanical properties |
Sintering Temperature | Lower temperatures and shorter times required, improving efficiency | Overheating risks causing phase transformations |
Practical Applications | Used in ceramics and powder metallurgy for high-density, high-strength products | Requires specialized equipment and techniques for fine particle handling |
Ready to optimize your sintering process? Contact our experts today for tailored solutions!