Pressure is a fundamental factor in the operation and efficiency of hydraulic systems. It directly influences the system's ability to perform work, transmit power, and maintain stability. Understanding how pressure affects hydraulic systems is crucial for optimizing performance, ensuring safety, and preventing failures. This answer explores the relationship between pressure and hydraulic systems, focusing on its impact on system components, performance, and operational efficiency.
Key Points Explained:
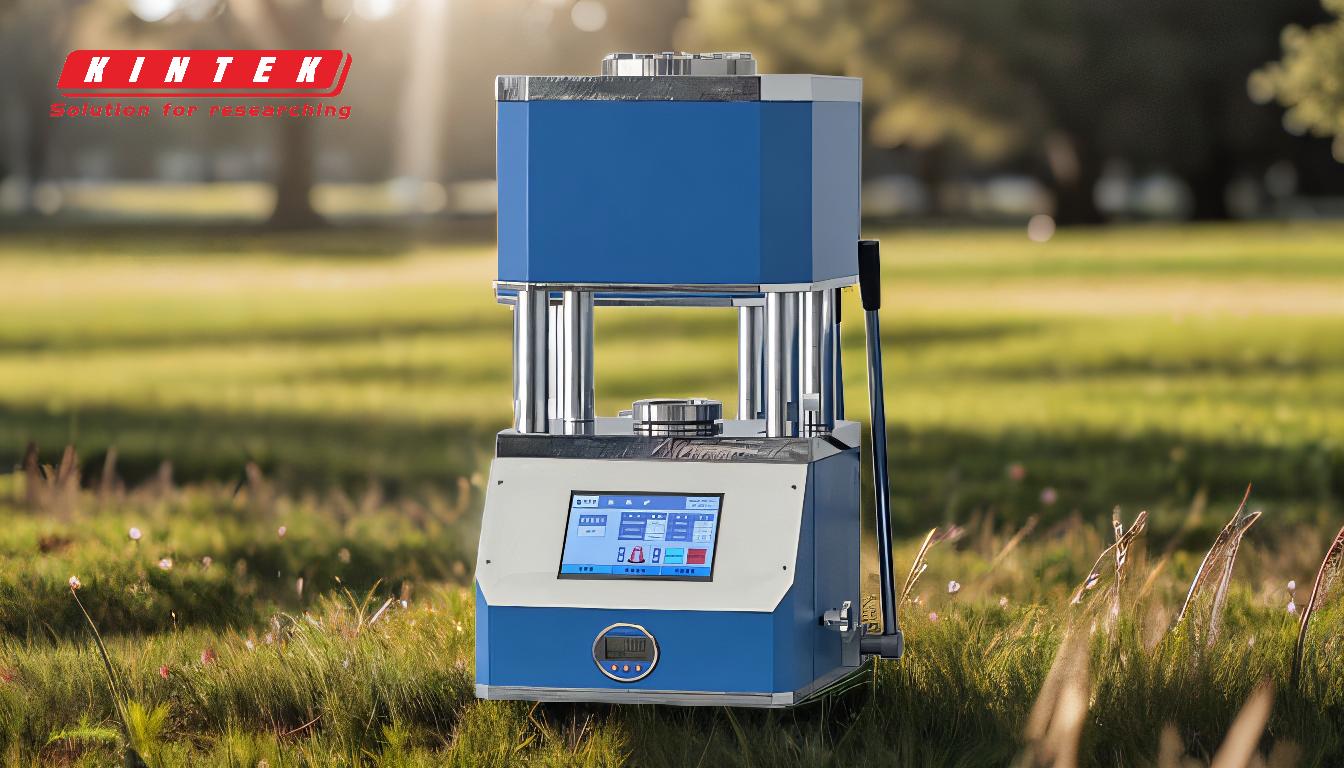
-
Role of Pressure in Hydraulic Systems
- Pressure is the force exerted by the hydraulic fluid per unit area, and it is essential for transmitting power within the system.
- Hydraulic systems rely on pressure to move actuators, such as cylinders or motors, which convert hydraulic energy into mechanical work.
- Without adequate pressure, the system cannot generate the force required to perform tasks, such as lifting heavy loads or operating machinery.
-
Impact on System Components
- Pumps: Pressure is generated by hydraulic pumps, which convert mechanical energy into hydraulic energy. Higher pressure increases the load on the pump, potentially leading to wear and reduced lifespan if not managed properly.
- Actuators: Pressure directly affects the force output of hydraulic cylinders and the torque output of hydraulic motors. Insufficient pressure results in weak or incomplete movements, while excessive pressure can cause damage or failure.
- Valves: Pressure control valves regulate system pressure to ensure safe and efficient operation. Excessive pressure can cause valves to malfunction or fail, leading to leaks or system shutdowns.
- Hoses and Seals: High pressure can strain hoses and seals, increasing the risk of leaks or bursts. Proper pressure ratings and maintenance are critical to prevent failures.
-
Effects on System Performance
- Efficiency: Optimal pressure ensures efficient energy transfer and minimizes energy losses due to friction or leakage.
- Speed and Force: Pressure determines the speed and force of hydraulic actuators. Higher pressure increases force but may reduce speed due to increased resistance.
- Stability: Maintaining consistent pressure is vital for smooth and stable operation. Pressure fluctuations can cause erratic movements, vibrations, or system instability.
-
Pressure-Related Challenges
- Cavitation: Low pressure in certain parts of the system can cause cavitation, where vapor bubbles form and collapse, damaging components and reducing efficiency.
- Overpressure: Excessive pressure can lead to component failure, leaks, or even catastrophic system breakdowns. Pressure relief valves are essential to prevent overpressure.
- Heat Generation: High pressure increases friction within the system, leading to heat generation. Excessive heat can degrade hydraulic fluid and damage components.
-
Pressure Management Strategies
- Pressure Relief Valves: These valves protect the system by releasing excess pressure, preventing damage and ensuring safety.
- Accumulators: These devices store hydraulic energy and help maintain consistent pressure, reducing pressure fluctuations and improving system stability.
- Regular Maintenance: Monitoring and maintaining pressure levels, checking for leaks, and replacing worn components are essential for optimal system performance.
By understanding how pressure affects hydraulic systems, operators and engineers can design, operate, and maintain systems that deliver reliable and efficient performance. Proper pressure management ensures safety, extends component lifespan, and maximizes the system's ability to perform work.
Summary Table:
Aspect | Impact of Pressure |
---|---|
System Components | - Pumps: Higher pressure increases wear. |
- Actuators: Insufficient or excessive pressure affects force and movement. | |
- Valves: Excessive pressure can cause malfunctions or failures. | |
- Hoses and Seals: High pressure strains components, risking leaks or bursts. | |
System Performance | - Efficiency: Optimal pressure minimizes energy losses. |
- Speed and Force: Higher pressure increases force but may reduce speed. | |
- Stability: Consistent pressure ensures smooth operation. | |
Pressure Challenges | - Cavitation: Low pressure causes vapor bubbles, damaging components. |
- Overpressure: Excessive pressure risks component failure or system breakdowns. | |
- Heat Generation: High pressure increases friction and heat, degrading components. | |
Pressure Management | - Pressure Relief Valves: Prevent overpressure and ensure safety. |
- Accumulators: Maintain consistent pressure and reduce fluctuations. | |
- Regular Maintenance: Monitor pressure levels and replace worn components. |
Discover how to optimize your hydraulic system's performance—contact our experts today for tailored solutions!