Sintering is a critical process in materials science that significantly impacts the density of a material by altering its microstructure. By applying heat and pressure, sintering reduces porosity and enhances the material's strength and durability. The process influences grain size, pore size, and grain boundary distribution, which are key factors in determining the final density of the material. Sintering allows for precise control over these microstructural features, leading to more consistent and high-quality products. Additionally, it is an energy-efficient and environmentally friendly method compared to melting, making it a preferred choice in manufacturing.
Key Points Explained:
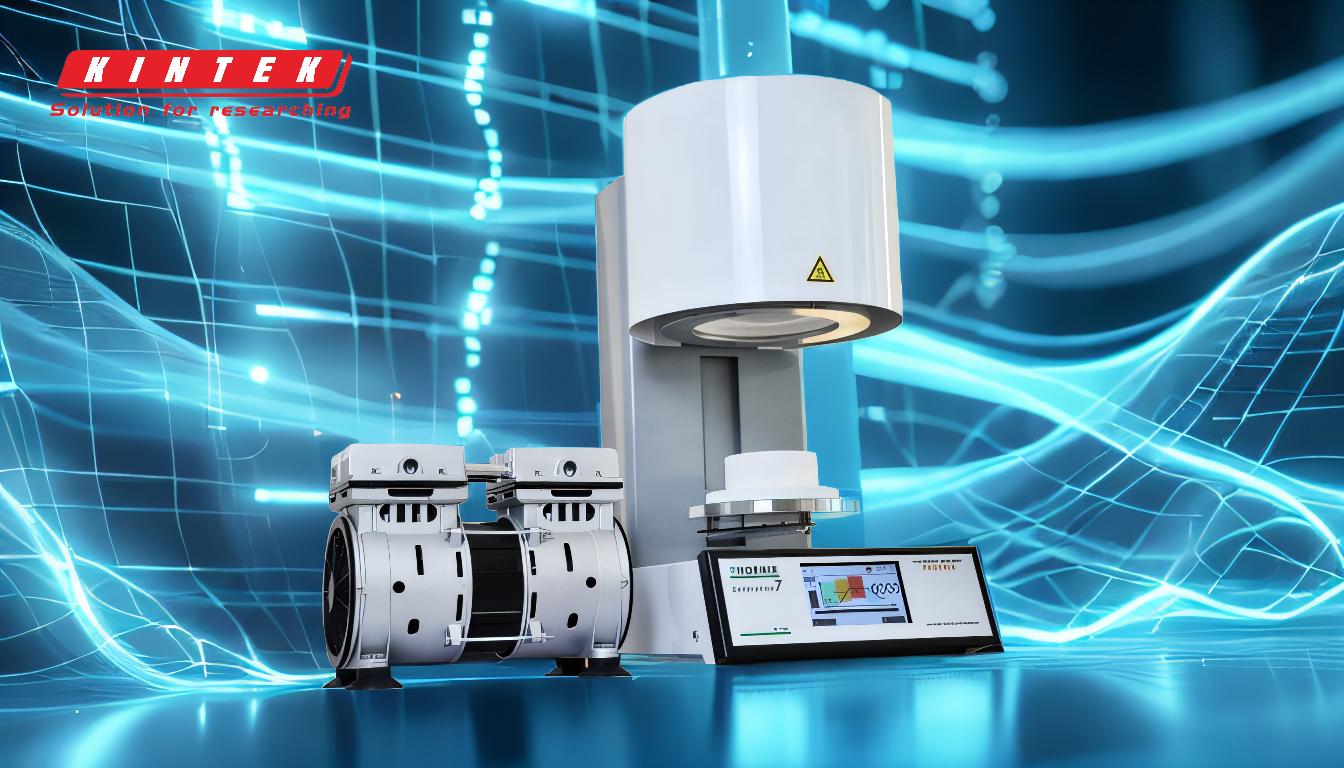
-
Definition and Mechanism of Sintering:
- Sintering is a process that combines materials by applying heat and pressure without melting them.
- It works by reducing the surface energy of particles, causing them to bond at the atomic level.
-
Impact on Microstructure:
- Grain Size: Sintering affects the size of grains within the material. Larger grains can reduce the number of grain boundaries, which can influence density.
- Pore Size: The process reduces the size and number of pores within the material, leading to increased density.
- Grain Boundary Distribution: Sintering alters the shape and distribution of grain boundaries, which can affect how densely the material is packed.
-
Effect on Density:
- Porosity Reduction: By minimizing porosity, sintering increases the overall density of the material.
- Material Consolidation: The process consolidates the material, making it more uniform and dense.
- Fully Dense Parts: Sintering is essential for producing fully dense parts that exhibit the desired material properties, such as strength and durability.
-
Controlled Variables in Sintering:
- Temperature: The temperature during sintering is crucial as it affects the vapor pressure and the rate at which particles bond.
- Initial Grain Size: The size of the initial grains can influence the final density, as smaller grains can pack more densely.
-
Benefits of Sintering:
- Strength and Durability: By reducing porosity and improving microstructure, sintering enhances the material's mechanical properties.
- Consistency: The process allows for greater control, resulting in more consistent and reliable products.
- Energy Efficiency: Sintering requires less energy than melting, making it a more sustainable option.
-
Applications and Importance:
- Manufacturing: Sintering is widely used in the production of ceramics and metals to achieve high-density materials with superior properties.
- Environmental Impact: The lower energy requirement of sintering compared to melting makes it an environmentally friendly choice in material processing.
In summary, sintering plays a pivotal role in determining the density of materials by influencing their microstructure. Through controlled application of heat and pressure, sintering reduces porosity, enhances grain and pore size distribution, and ultimately leads to materials with higher density, improved strength, and greater durability. This makes sintering an indispensable process in the manufacturing of high-performance materials.
Summary Table:
Aspect | Impact of Sintering |
---|---|
Grain Size | Influences density by altering grain boundaries; larger grains reduce boundary density. |
Pore Size | Reduces porosity, leading to higher material density. |
Grain Boundary Distribution | Enhances packing density by optimizing grain boundary shape and distribution. |
Porosity Reduction | Minimizes voids, increasing overall density. |
Energy Efficiency | Requires less energy than melting, making it environmentally friendly. |
Applications | Widely used in ceramics and metals for high-density, high-performance materials. |
Discover how sintering can optimize your material properties—contact our experts today to learn more!