Sintering is a critical process in materials science that significantly impacts the mechanical properties of materials such as strength, hardness, wear resistance, and durability. By bonding and densifying particles through controlled heating and diffusion mechanisms, sintering reduces porosity, refines grain size, and improves grain boundary distribution. These microstructural changes lead to a more cohesive and dense material structure, enhancing overall mechanical integrity. Additionally, sintering is energy-efficient compared to melting, making it an environmentally friendly manufacturing option. The process ensures consistent product quality and superior performance characteristics, making it indispensable for producing high-performance ceramic and metal components.
Key Points Explained:
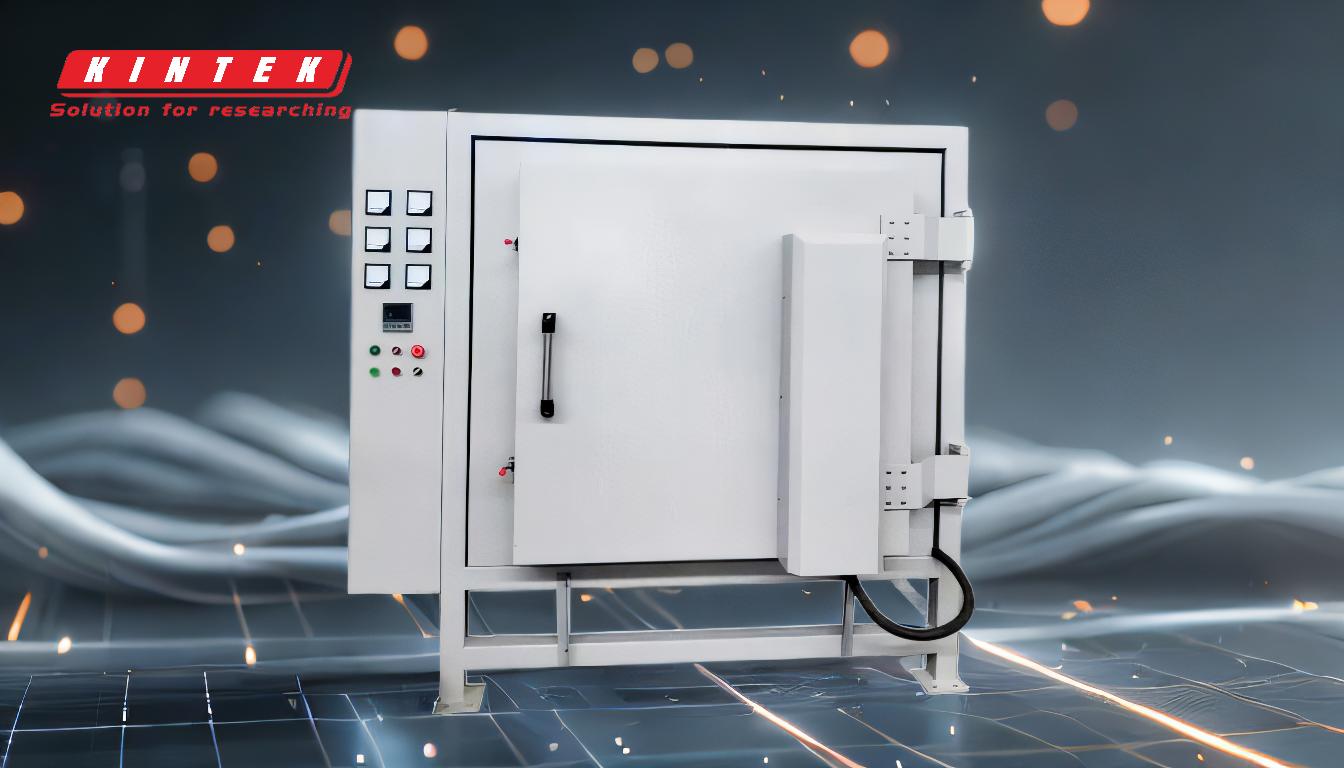
-
Microstructural Changes During Sintering:
- Sintering alters the grain size, pore size, and grain boundary distribution in materials.
- These changes are critical because they directly influence the material's mechanical properties, such as strength and durability.
- A reduction in porosity and refinement of grain boundaries contribute to a denser and more cohesive structure.
-
Enhanced Mechanical Properties:
- Strength: Sintering bonds particles together, reducing voids and creating a more uniform structure, which enhances tensile and compressive strength.
- Hardness: The densification process increases material hardness by reducing porosity and improving grain-to-grain contact.
- Wear Resistance: A denser structure with fewer defects improves resistance to wear and abrasion, extending the material's lifespan.
- Durability: The cohesive structure formed during sintering ensures the material can withstand mechanical stress and environmental factors over time.
-
Controlled Heating and Diffusion Mechanisms:
- Sintering involves carefully controlled heating to facilitate particle bonding without melting the material.
- Diffusion mechanisms enable atoms to migrate across particle boundaries, leading to densification and grain growth.
- This controlled process ensures the material achieves the desired mechanical properties while maintaining dimensional stability.
-
Energy Efficiency and Environmental Benefits:
- Sintering requires less energy compared to melting, making it a more sustainable manufacturing option.
- The process minimizes waste and allows for greater control over material properties, resulting in consistent and high-quality products.
-
Applications in Ceramics and Metals:
- Sintering is essential for producing fully dense ceramic and metal components with optimal mechanical properties.
- It is widely used in industries such as automotive, aerospace, and electronics, where high-performance materials are required.
-
Impact on Manufacturing Consistency:
- Sintering provides precise control over material properties, ensuring uniformity across batches.
- This consistency is crucial for applications where reliability and performance are paramount.
By understanding how sintering affects mechanical properties, manufacturers can optimize the process to produce materials with superior performance characteristics, meeting the demands of modern engineering applications.
Summary Table:
Aspect | Impact of Sintering |
---|---|
Microstructural Changes | Reduces porosity, refines grain size, and improves grain boundary distribution. |
Strength | Bonds particles, reduces voids, and enhances tensile and compressive strength. |
Hardness | Increases hardness by reducing porosity and improving grain-to-grain contact. |
Wear Resistance | Improves resistance to wear and abrasion, extending material lifespan. |
Durability | Ensures cohesive structure to withstand mechanical stress and environmental factors. |
Energy Efficiency | Requires less energy than melting, making it a sustainable manufacturing option. |
Applications | Essential for high-performance ceramics and metals in automotive, aerospace, and more. |
Optimize your manufacturing process with sintering—contact our experts today to learn more!