Sintering temperature plays a critical role in determining the density of a material, as it directly influences the degree of particle bonding and porosity reduction. At optimal sintering temperatures, particles bond effectively, leading to higher density and improved mechanical properties. However, deviations from this optimal range—either too high or too low—can negatively impact density and overall material performance. High temperatures may cause excessive grain growth or defects, while low temperatures may result in insufficient bonding and increased porosity. Understanding the relationship between sintering temperature and density is essential for achieving the desired material properties in ceramics and metals.
Key Points Explained:
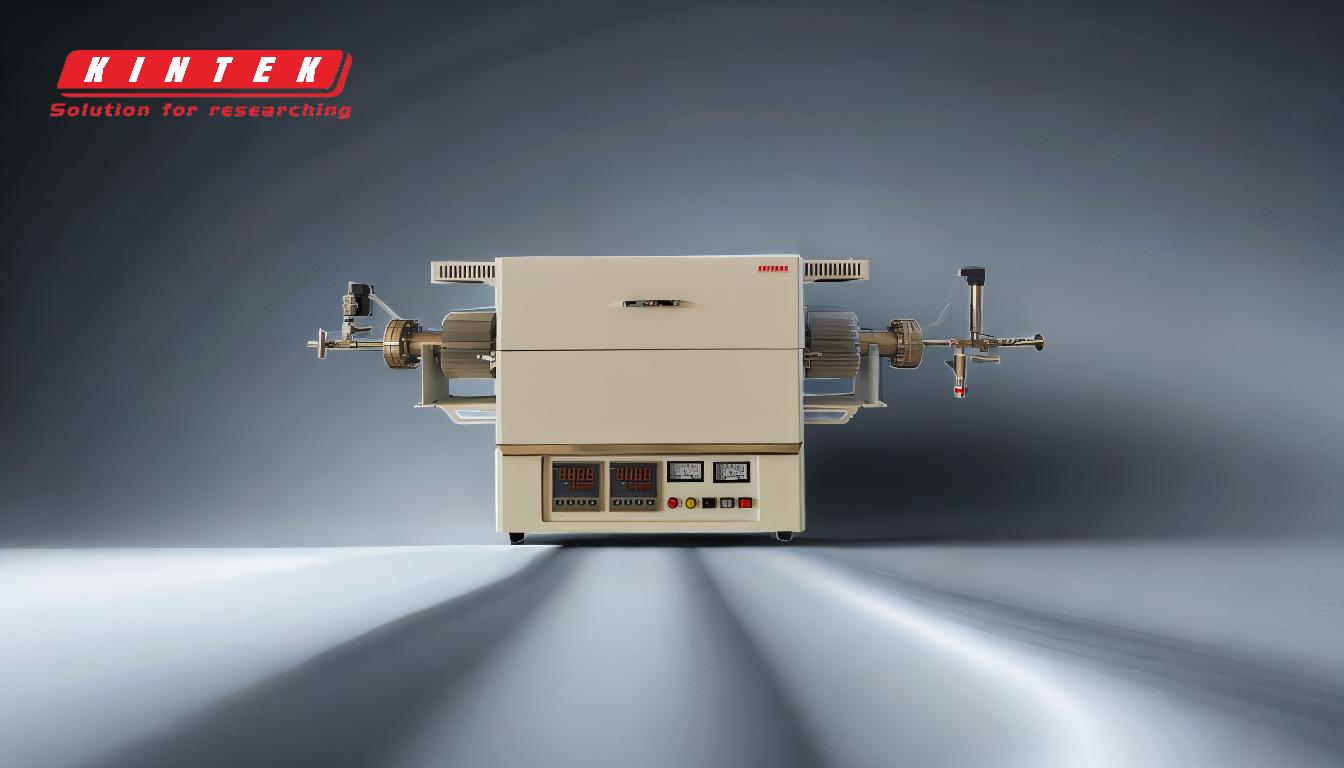
-
Optimal Sintering Temperature and Density:
- The sintering temperature must be carefully controlled to achieve the desired density. At the optimal temperature, particles bond effectively, reducing porosity and increasing density.
- For example, studies on zirconia indicate that sintering at approximately 1500℃ maximizes strength and density. Deviations from this temperature can lead to reduced density due to improper bonding or excessive grain growth.
-
Effects of High Sintering Temperatures:
- Excessive sintering temperatures can lead to over-sintering, which may cause defects such as grain coarsening or cracking. These defects increase porosity and reduce density.
- High temperatures can also lead to evaporation of volatile components or unwanted phase transformations, further degrading material properties.
-
Effects of Low Sintering Temperatures:
- Insufficient sintering temperatures result in incomplete particle bonding, leaving residual porosity and lower density.
- Low temperatures may also prevent the material from achieving its full mechanical potential, as the bonds between particles are not strong enough to support the desired properties.
-
Role of Sintering Time:
- Sintering time is closely related to temperature. Longer sintering times at appropriate temperatures can enhance density by allowing more time for particle bonding and pore elimination.
- However, excessively long sintering times at high temperatures can lead to over-sintering and defects, while insufficient time at low temperatures may not allow for proper densification.
-
Material-Specific Considerations:
- Different materials have unique sintering temperature ranges. For example, zirconia achieves optimal density at around 1500℃, while other materials may require higher or lower temperatures.
- Understanding the specific sintering behavior of a material is crucial for achieving the desired density and mechanical properties.
-
Practical Implications for Equipment and Consumable Purchasers:
- When selecting sintering equipment, it is important to ensure that the system can maintain precise temperature control within the optimal range for the material being processed.
- Consumables, such as sintering furnaces and temperature sensors, should be chosen based on their ability to provide consistent and accurate temperature profiles.
- Monitoring and controlling sintering parameters, including temperature and time, is essential for producing high-density components with consistent quality.
By carefully managing sintering temperature and time, manufacturers can achieve the desired density and material properties, ensuring that the final product meets performance requirements.
Summary Table:
Key Factor | Impact on Density |
---|---|
Optimal Sintering Temperature | Maximizes density by enabling effective particle bonding and porosity reduction. |
High Sintering Temperatures | Causes defects like grain coarsening, increasing porosity and reducing density. |
Low Sintering Temperatures | Leads to incomplete bonding, leaving residual porosity and lower density. |
Sintering Time | Longer times at optimal temperatures enhance density; improper times cause defects. |
Material-Specific Needs | Different materials require unique temperature ranges for optimal density (e.g., zirconia at 1500℃). |
Achieve the perfect sintering results for your materials—contact our experts today for tailored solutions!