Sintering is a manufacturing process that transforms powdered materials into solid objects by applying heat and pressure below the material's melting point. This process relies on atomic diffusion, where atoms move across particle boundaries, causing particles to bond and densify. Sintering is widely used in ceramics, metals, and plastics, particularly for materials with high melting points. The process occurs in stages, reducing porosity and enhancing structural integrity. Key mechanisms include surface diffusion, viscous flow, evaporative coalescence, bulk diffusion, and grain boundary diffusion. Sintering is essential for creating durable, high-strength components in industries ranging from aerospace to electronics.
Key Points Explained:
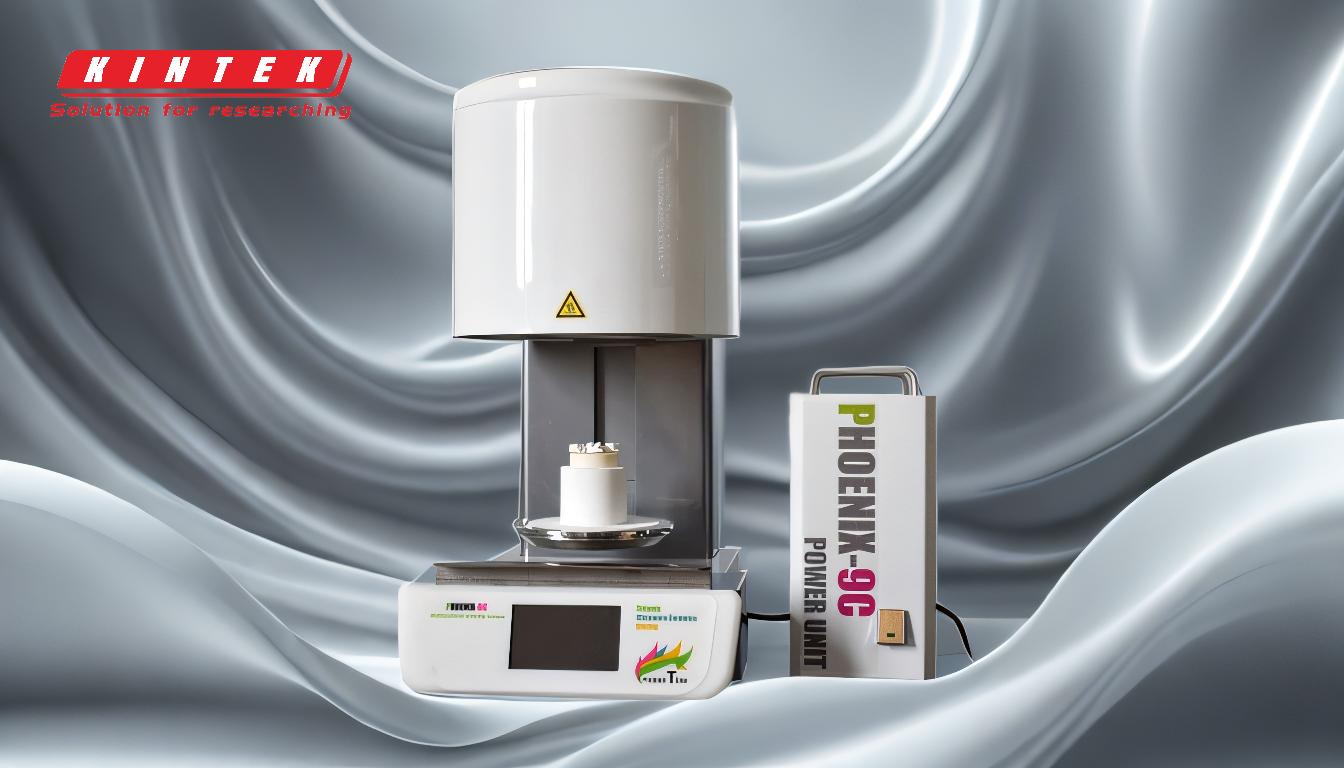
-
Definition and Purpose of Sintering:
- Sintering is a process that compacts powdered materials into solid objects by applying heat and pressure without melting the material.
- It is used to create dense, strong components from powders, particularly for materials with high melting points like ceramics, metals (e.g., tungsten, molybdenum), and plastics.
- The primary goal is to reduce porosity and improve mechanical properties such as strength and durability.
-
Mechanisms of Sintering:
- Atomic Diffusion: Atoms move across particle boundaries, fusing particles together. This is the core mechanism driving sintering.
- Surface Diffusion: Atoms migrate along the surface of particles, smoothing out irregularities.
- Viscous Flow: Particles deform and flow under pressure, filling gaps between particles.
- Evaporative Coalescence: Material evaporates from high-energy areas and condenses in low-energy areas, promoting bonding.
- Bulk Diffusion: Atoms move through the interior of particles, aiding densification.
- Grain Boundary Diffusion: Atoms diffuse along grain boundaries, enhancing particle bonding.
-
Stages of Sintering:
- Initial Stage: Particles begin to bond at contact points, forming necks between them. Porosity is high, but the structure starts to consolidate.
- Intermediate Stage: Porosity decreases as particles continue to bond and densify. The material gains strength and density.
- Final Stage: The material reaches near-full density, with minimal porosity. Grain growth may occur, further enhancing mechanical properties.
-
Temperature and Pressure Conditions:
- Sintering occurs at temperatures below the material's melting point to prevent liquefaction.
- The exact temperature and pressure depend on the material and desired properties.
- For example, ceramics may require temperatures around 70-90% of their melting point, while metals might need higher pressures to achieve densification.
-
Applications of Sintering:
- Ceramics: Used to produce high-strength, heat-resistant components like insulators, cutting tools, and biomedical implants.
- Metals: Commonly used for manufacturing parts with complex shapes, such as gears, bearings, and filters.
- Plastics: Sintered plastics are used in 3D printing (e.g., selective laser sintering) to create lightweight, durable parts.
-
Advantages of Sintering:
- Material Efficiency: Minimizes waste by using powdered materials.
- Complex Shapes: Enables the production of intricate geometries that are difficult to achieve with traditional methods.
- High Strength: Produces components with excellent mechanical properties.
- Cost-Effective: Reduces the need for machining and finishing processes.
-
Challenges and Considerations:
- Porosity Control: Achieving uniform density can be challenging, especially in complex shapes.
- Material Selection: Not all materials are suitable for sintering; some may require additives or binders.
- Process Optimization: Temperature, pressure, and time must be carefully controlled to avoid defects like warping or cracking.
-
Tools and Techniques:
- Dilatometers: Instruments like Linseis push rod dilatometers are used to measure dimensional changes during sintering, helping to optimize the process.
- Binders: Temporary binders may be added to powders to maintain shape before sintering.
- Molds and Compaction: High-pressure compaction is often used to shape powders before heating.
By understanding these key points, manufacturers can effectively utilize sintering to produce high-quality components tailored to specific applications. The process's versatility and efficiency make it a cornerstone of modern manufacturing.
Summary Table:
Aspect | Details |
---|---|
Definition | Process of compacting powdered materials into solids using heat and pressure. |
Key Mechanisms | Atomic diffusion, surface diffusion, viscous flow, evaporative coalescence. |
Stages | Initial, intermediate, and final stages of densification. |
Applications | Ceramics, metals, plastics (e.g., insulators, gears, 3D printing). |
Advantages | Material efficiency, complex shapes, high strength, cost-effectiveness. |
Challenges | Porosity control, material selection, process optimization. |
Tools | Dilatometers, binders, molds, and compaction equipment. |
Discover how sintering can revolutionize your manufacturing process—contact our experts today for tailored solutions!