Sintering is a critical process in ceramics manufacturing that transforms powdered materials into dense, strong, and durable products. It involves heating the material below its melting point to bond particles together, reducing porosity and enhancing mechanical properties. The process typically includes steps like material preparation, compaction, controlled heating in a sintering furnace, and cooling. Each stage is carefully optimized to ensure the final product meets desired specifications, such as strength, density, and thermal stability. Sintering is widely used in industries like electronics, aerospace, and automotive due to its ability to produce complex shapes with high precision and reliability.
Key Points Explained:
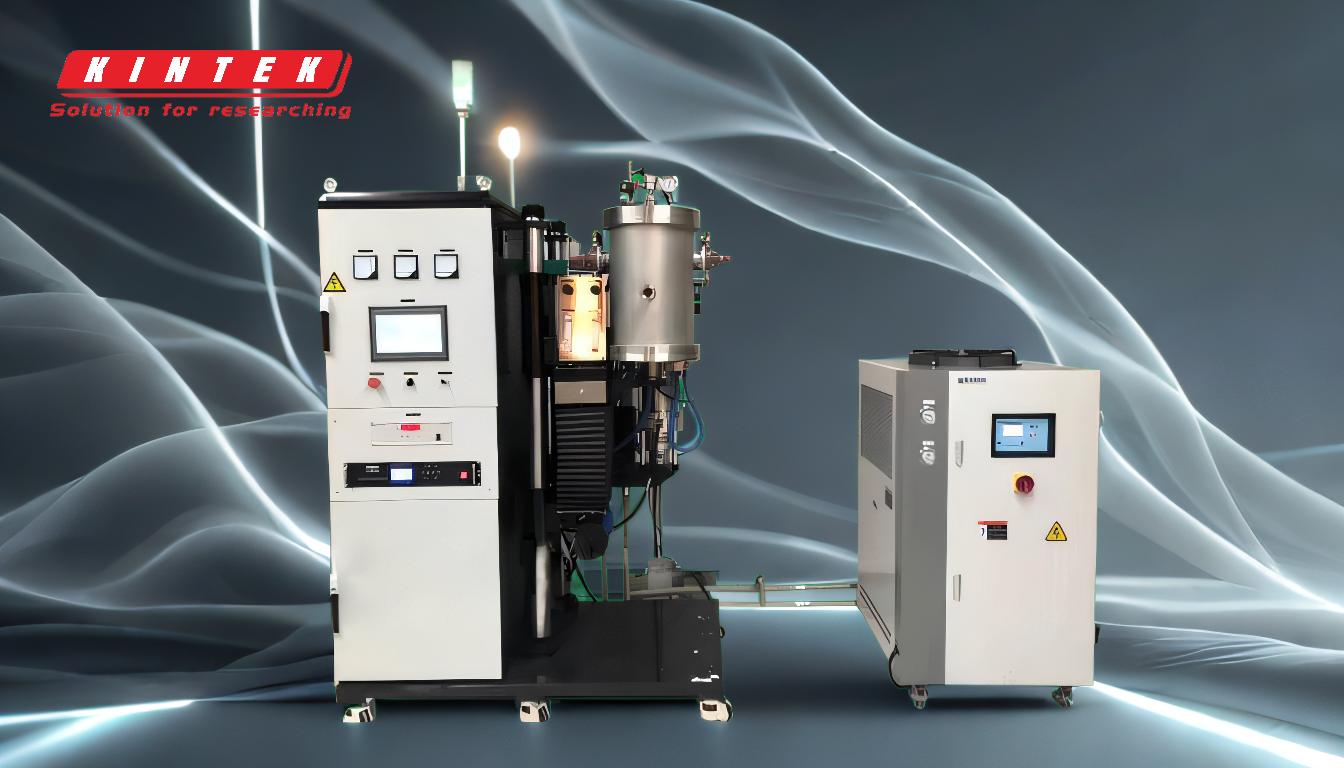
-
Material Preparation:
- The process begins with the preparation of raw materials, which are often in powder form. These powders are mixed with binders, deflocculants, and other additives to create a uniform mixture.
- This step ensures homogeneity and improves the flowability of the powder, which is crucial for achieving consistent results during compaction and sintering.
-
Compaction:
- The mixed powder is then compacted under high pressure to form a "green body," which is a pre-sintered shape close to the final product.
- Compaction eliminates voids and ensures uniformity in density, which is essential for preventing defects like cracks or warping during sintering.
-
Binder Removal (Debinding):
- Before sintering, the green body is heated at a low temperature to remove binders and other organic additives. This step prevents contamination and ensures the material is ready for high-temperature sintering.
- Proper debinding is critical to avoid issues like bloating or cracking during the sintering process.
-
Sintering in a Furnace:
- The green body is then placed in a sintering furnace and heated to a temperature below the material's melting point. This controlled heating allows particles to bond through diffusion, forming necks between particles and reducing porosity.
- The temperature and duration of sintering are carefully controlled to achieve the desired density and mechanical properties without causing complete melting.
-
Densification and Particle Bonding:
- During sintering, particles undergo diffusion, leading to neck formation and densification. This process reduces porosity and increases the material's strength and durability.
- The result is a dense, cohesive structure with improved mechanical, thermal, and electrical properties.
-
Cooling:
- After sintering, the product is cooled gradually to solidify its structure and minimize internal stresses. Proper cooling ensures the final product retains its shape and properties.
- Rapid cooling can lead to thermal shock, causing cracks or other defects.
-
Optimization and Quality Control:
- The sintering process is optimized to achieve specific physical properties, such as strength, density, and thermal stability. Parameters like temperature, pressure, and heating rate are tailored to the material and application.
- Quality control measures, such as monitoring shrinkage and porosity, ensure the final product meets industry standards.
By understanding these key steps, manufacturers can optimize the sintering process to produce high-quality ceramic products with precise dimensions and superior performance. The use of advanced sintering furnaces and process control techniques further enhances the efficiency and reliability of this critical manufacturing method.
Summary Table:
Step | Description |
---|---|
Material Preparation | Mixing powders with binders and additives for uniformity and flowability. |
Compaction | Pressing powder into a 'green body' to eliminate voids and ensure density. |
Debinding | Removing binders at low temperatures to prepare for sintering. |
Sintering | Heating in a sintering furnace to bond particles and reduce porosity. |
Densification | Diffusion forms necks between particles, increasing strength and durability. |
Cooling | Gradual cooling to solidify the structure and minimize defects. |
Quality Control | Optimizing parameters and monitoring properties to meet industry standards. |
Discover how sintering can enhance your ceramic manufacturing—contact our experts today for tailored solutions!