E-beam evaporation is a physical vapor deposition (PVD) technique used to create thin, high-purity coatings on substrates. The process involves generating an electron beam from a heated tungsten filament, which is focused onto a source material in a crucible. The intense heat from the electron beam melts and evaporates the material, which then flows upward in a vacuum chamber and deposits onto a substrate positioned above. This results in a thin film coating, typically ranging from 5 to 250 nanometers in thickness, with excellent purity and adhesion properties. E-beam evaporation is widely used in applications such as optical thin films, solar panels, and architectural glass due to its ability to produce precise and durable coatings.
Key Points Explained:
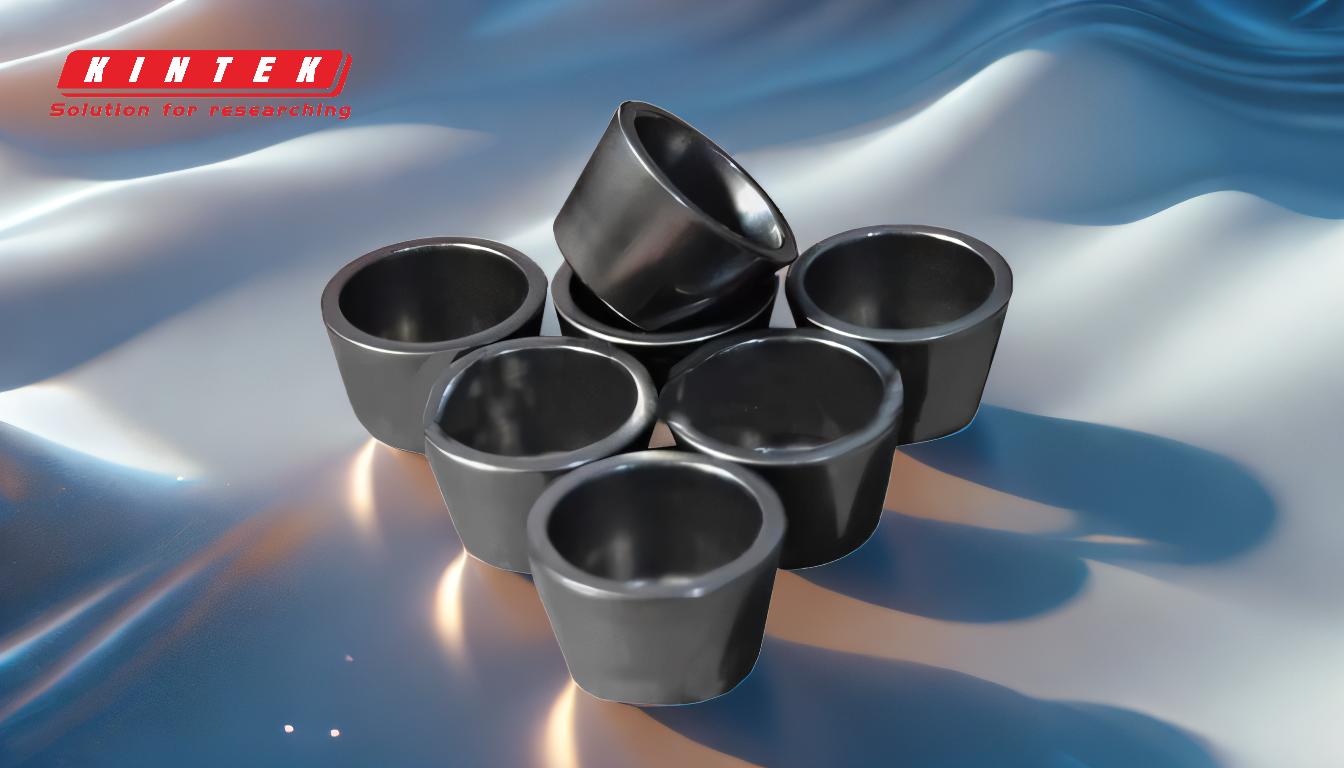
-
Process Overview:
- E-beam evaporation is a physical vapor deposition (PVD) process where a high-energy electron beam is used to vaporize a source material.
- The vaporized material condenses onto a substrate, forming a thin film coating.
- The process occurs in a high-vacuum environment to ensure high purity and prevent contamination.
-
Key Components:
- Vacuum Chamber: The process takes place in a vacuum chamber to minimize impurities and ensure a controlled environment.
- Electron Beam Source: A tungsten filament is heated to over 2,000°C to generate electrons, which are focused into a beam using magnetic fields.
- Crucible: Holds the source material and is typically water-cooled to prevent contamination and overheating.
-
How the Electron Beam Works:
- The electron beam is generated by heating a tungsten filament and accelerating the electrons toward the source material.
- The beam is focused onto the material using magnetic fields, creating intense localized heat.
- The heat melts and evaporates the material, converting it into a gaseous state.
-
Deposition Process:
- The evaporated material flows upward in the vacuum chamber due to the high-energy process.
- The material condenses onto the substrate, forming a thin film with excellent adhesion and purity.
- The thickness of the coating can be precisely controlled, typically ranging from 5 to 250 nanometers.
-
Applications:
- Optical Thin Films: Used in applications like anti-reflective coatings for glasses and lenses.
- Solar Panels: Enhances the efficiency of solar cells by depositing reflective and conductive layers.
- Architectural Glass: Provides durable and reflective coatings for energy-efficient building materials.
- Semiconductors: Used to deposit high-purity metal films for electronic components.
-
Advantages of E-Beam Evaporation:
- High Purity: The vacuum environment and precise control of the electron beam ensure minimal contamination.
- Excellent Adhesion: The evaporated material bonds strongly with the substrate, resulting in durable coatings.
- Precision: The process allows for precise control over coating thickness and uniformity.
- Versatility: Suitable for a wide range of materials, including metals, alloys, and ceramics.
-
Challenges and Considerations:
- High Equipment Cost: The vacuum chamber, electron beam source, and cooling systems are expensive.
- Material Limitations: Some materials may not evaporate efficiently or may react with the crucible.
- Complexity: The process requires careful control of parameters such as beam intensity, vacuum level, and substrate positioning.
-
Comparison with Other PVD Techniques:
- Thermal Evaporation: Unlike e-beam evaporation, thermal evaporation uses resistive heating to melt the source material, which may result in lower purity and less precise control.
- Sputtering: Sputtering involves bombarding the target material with ions, which can produce films with better step coverage but may introduce impurities.
By understanding these key points, equipment and consumable purchasers can make informed decisions about using e-beam evaporation for their specific applications, ensuring high-quality and cost-effective thin film coatings.
Summary Table:
Aspect | Details |
---|---|
Process | High-energy electron beam vaporizes material in a vacuum chamber. |
Key Components | Vacuum chamber, electron beam source, crucible. |
Coating Thickness | 5 to 250 nanometers, with precise control. |
Applications | Optical thin films, solar panels, architectural glass, semiconductors. |
Advantages | High purity, excellent adhesion, precision, versatility. |
Challenges | High equipment cost, material limitations, process complexity. |
Discover how e-beam evaporation can elevate your projects—contact our experts today!