Thin film deposition is a critical process in various industries, including electronics, optics, and energy, where precise layers of material are applied to substrates to achieve specific functional properties. The process involves several methods, broadly categorized into chemical and physical deposition techniques. Chemical methods, such as Chemical Vapor Deposition (CVD) and Atomic Layer Deposition (ALD), rely on chemical reactions to form thin films, while physical methods, like Physical Vapor Deposition (PVD), involve the physical transfer of material from a source to a substrate. Both methods require controlled environments, often in a vacuum, to ensure purity and uniformity of the deposited films. The choice of method depends on the desired film characteristics, which can include optical, electronic, mechanical, or chemical properties tailored to specific applications.
Key Points Explained:
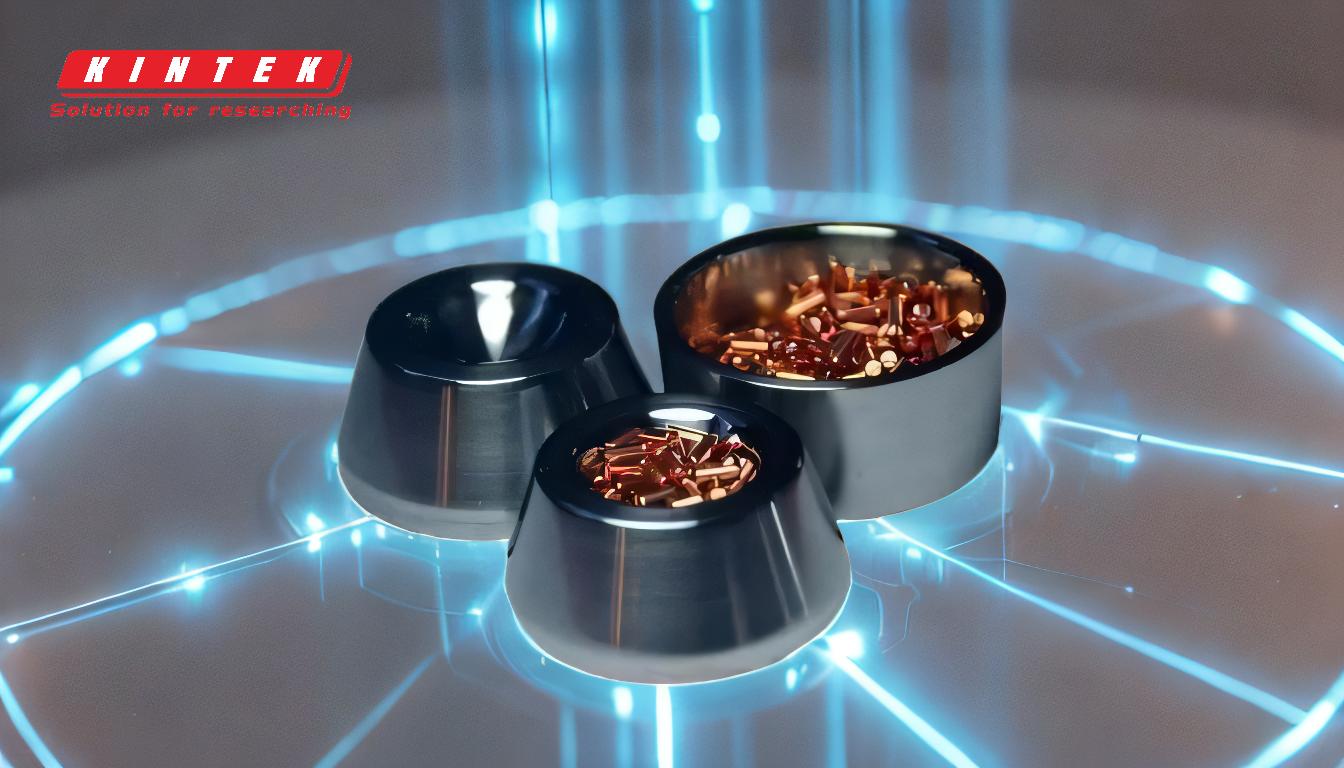
-
Categories of Thin Film Deposition Methods:
- Chemical Methods: These include techniques like Chemical Vapor Deposition (CVD), Plasma-Enhanced CVD (PECVD), Atomic Layer Deposition (ALD), electroplating, sol-gel, dip coating, and spin coating. These methods rely on chemical reactions to deposit thin films.
- Physical Methods: These primarily involve Physical Vapor Deposition (PVD) techniques such as sputtering, thermal evaporation, carbon coating, electron beam evaporation, molecular beam epitaxy (MBE), and pulsed laser deposition (PLD). These methods use physical processes to transfer material from a source to a substrate.
-
Basic Steps in Thin Film Deposition:
- Preparation: The substrate is cleaned and prepared to ensure proper adhesion of the thin film.
- Deposition: The actual process of applying the thin film, which can involve evaporation, sputtering, or chemical reactions, depending on the method used.
- Condensation: The vaporized or chemically reacted material condenses on the substrate to form a solid film.
- Post-Deposition Treatment: This may include annealing, etching, or other processes to achieve the desired film properties.
-
Chemical Vapor Deposition (CVD):
- Process: Reactant gases are introduced into a chamber where they undergo chemical reactions on the surface of the substrate, forming a solid film.
- Applications: CVD is widely used in the semiconductor industry for depositing high-purity thin films, such as silicon dioxide and silicon nitride.
-
Physical Vapor Deposition (PVD):
- Process: Material is vaporized from a solid source in a vacuum and then condenses on the substrate to form a thin film.
- Techniques: Includes methods like sputtering, where atoms are ejected from a target material, and thermal evaporation, where material is heated until it evaporates.
- Applications: PVD is used for depositing metals, alloys, and compounds in applications ranging from microelectronics to decorative coatings.
-
Evaporation Process in Thin Film Deposition:
- Principles: Involves the evaporation of source material and its subsequent condensation on the substrate. This process must occur in a vacuum to prevent contamination and ensure uniform deposition.
- Heat Source: Various heat sources, such as resistive heating or electron beams, are used to evaporate the material.
-
Applications and Requirements:
- Photonic and Optical: Thin films are used in applications like anti-reflective coatings, mirrors, and optical filters.
- Electronic: Used in semiconductor devices, integrated circuits, and sensors.
- Mechanical: Applied in wear-resistant coatings and lubricants.
- Chemical: Used in protective coatings and catalytic layers.
-
Advanced Techniques and Materials:
- Atomic Layer Deposition (ALD): Allows for the deposition of films at the atomic level, providing exceptional control over film thickness and uniformity.
- Flexible Electronics: Newer methods involve creating fine layers of polymer compounds for applications like flexible solar cells and organic light-emitting diodes (OLEDs).
-
Environmental and Process Control:
- Vacuum Conditions: Essential for most deposition methods to prevent contamination and ensure high-quality films.
- Temperature and Pressure Control: Critical parameters that must be precisely controlled to achieve the desired film properties.
By understanding these key points, one can appreciate the complexity and precision required in thin film deposition processes, which are essential for producing materials with specific functional characteristics tailored to a wide range of applications.
Summary Table:
Category | Methods | Applications |
---|---|---|
Chemical Methods | CVD, PECVD, ALD, electroplating, sol-gel, dip coating, spin coating | High-purity films, semiconductors, protective coatings |
Physical Methods | Sputtering, thermal evaporation, electron beam evaporation, MBE, PLD | Metals, alloys, decorative coatings, microelectronics |
Key Steps | Preparation, deposition, condensation, post-deposition treatment | Ensures proper adhesion, uniformity, and desired film properties |
Advanced Techniques | ALD, flexible electronics (e.g., OLEDs, flexible solar cells) | Atomic-level precision, flexible applications |
Environmental Control | Vacuum conditions, temperature, and pressure control | Prevents contamination, ensures high-quality films |
Discover how thin film deposition can enhance your projects—contact our experts today!