Vacuum brazing is a highly effective metal joining process that operates in a low-pressure, high-temperature environment, typically within the range of 10^-5 to 10^-6 atmospheres. This method is fluxless, meaning it does not require the use of chemical fluxes to clean the metal surfaces. Instead, the vacuum environment naturally deoxidizes the metals, removes high vapor pressure contaminants, and prevents reactions that would otherwise occur in hydrogen. The process involves heating the base metals just below their melting points and introducing a filler metal with a lower melting point. The filler metal liquefies and diffuses into the tiny gaps between the workpieces through capillary action, creating a strong, reliable bond upon cooling. This technique is particularly advantageous for joining materials that are sensitive to oxidation or contamination, such as stainless steel, and is widely used in industries requiring high precision and strength in metal joints.
Key Points Explained:
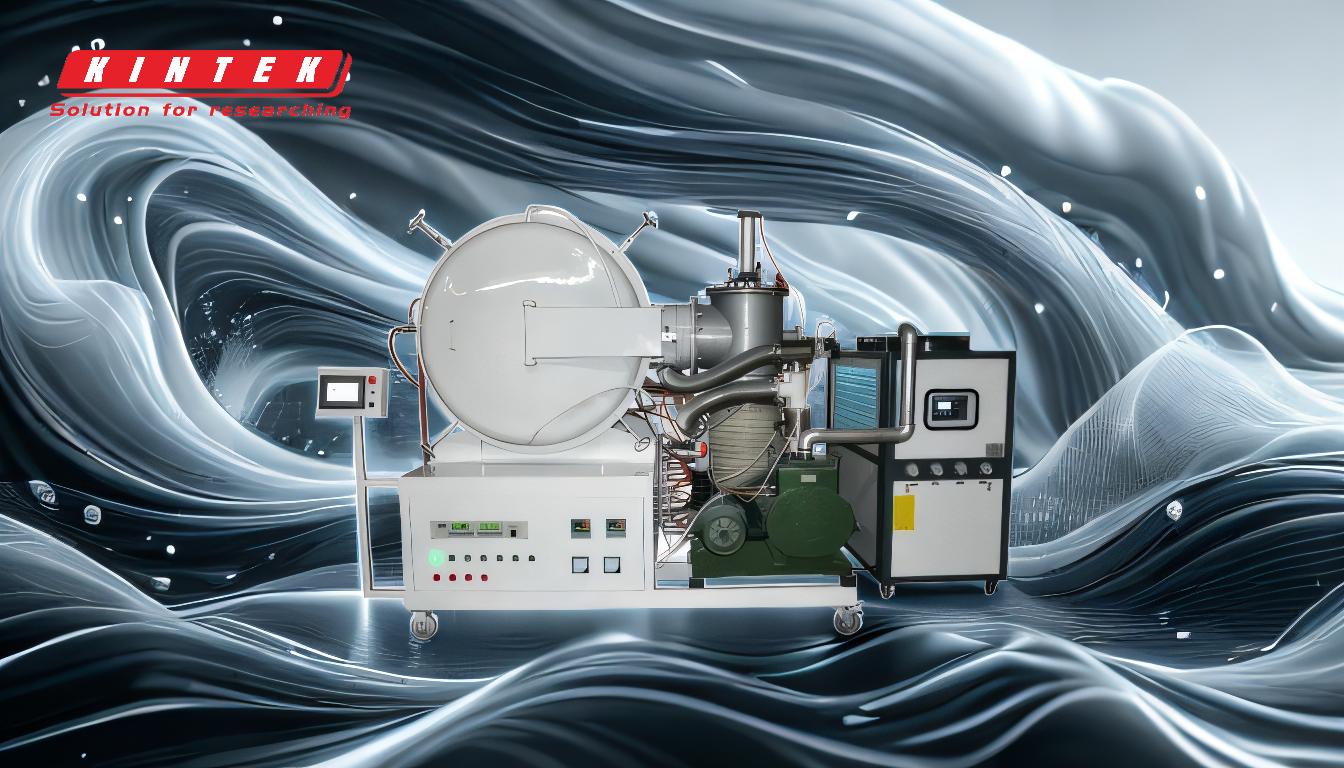
-
Environment and Conditions:
- Vacuum Environment: The process takes place in a vacuum chamber with pressures typically ranging from 10^-5 to 10^-6 atmospheres. This low-pressure environment is crucial for preventing oxidation and contamination.
- High Temperature: The metals are heated to temperatures just below their melting points, which facilitates the melting of the filler metal without compromising the integrity of the base metals.
-
Fluxless Process:
- No Chemical Fluxes: Unlike traditional brazing methods, vacuum brazing does not require chemical fluxes to clean the metal surfaces. The vacuum environment naturally deoxidizes the metals and removes contaminants.
- Clean Joints: The absence of fluxes results in cleaner joints, reducing the need for post-brazing cleaning and minimizing the risk of flux-related defects.
-
Filler Metal:
- Lower Melting Point: The filler metal used in vacuum brazing has a lower melting point than the base metals. This ensures that the filler metal liquefies before the base metals, allowing it to flow into the gaps between the workpieces.
- Capillary Action: The filler metal is drawn into the tiny gaps between the workpieces through capillary action, ensuring a uniform and strong bond.
-
Deoxidation and Contaminant Removal:
- Deoxidation: The vacuum environment naturally deoxidizes the metal surfaces, which is essential for achieving a strong bond.
- Contaminant Removal: High vapor pressure contaminants are removed under vacuum conditions, further enhancing the quality of the brazed joint.
-
Process Steps:
- Preparation: The metal surfaces are cleaned and prepared to ensure optimal bonding. This may involve degreasing, polishing, or other surface treatments.
- Assembly and Filler Metal Placement: The workpieces are assembled with the filler metal placed in the desired locations. The assembly is then placed in the vacuum furnace.
- Heating and Brazing: The furnace is heated to the required temperature, causing the filler metal to melt and flow into the gaps between the workpieces.
- Cooling and Inspection: After brazing, the assembly is allowed to cool, and the brazed joint is inspected for quality and integrity.
-
Advantages:
- High Precision: Vacuum brazing allows for precise control over the brazing process, resulting in high-quality, reliable joints.
- Material Compatibility: This method is suitable for a wide range of materials, including those that are sensitive to oxidation or contamination.
- Strong Bonds: The resulting joints are strong and durable, making vacuum brazing ideal for critical applications in industries such as aerospace, automotive, and electronics.
-
Applications:
- Stainless Steel: Vacuum brazing is commonly used for joining stainless steel components, where the prevention of oxidation and contamination is crucial.
- Complex Assemblies: The process is well-suited for complex assemblies that require precise, strong, and clean joints.
- High-Performance Components: Vacuum brazing is often used in the production of high-performance components that must withstand extreme conditions.
In summary, vacuum brazing is a sophisticated and highly effective method for joining metals, offering numerous advantages over traditional brazing techniques. Its ability to produce clean, strong, and reliable joints makes it an invaluable process in various high-tech industries.
Summary Table:
Aspect | Details |
---|---|
Environment | Vacuum chamber (10^-5 to 10^-6 atm), high temperature just below melting point |
Fluxless Process | No chemical fluxes; vacuum deoxidizes and removes contaminants |
Filler Metal | Lower melting point, flows via capillary action for uniform bonds |
Deoxidation | Natural deoxidation in vacuum, removes high vapor pressure contaminants |
Process Steps | Preparation, assembly, heating, cooling, and inspection |
Advantages | High precision, material compatibility, strong, durable joints |
Applications | Stainless steel, complex assemblies, high-performance components |
Interested in vacuum brazing for your metal joining needs? Contact us today to learn more!