Vacuum brazing is a specialized process used to join metals without the need for flux, ensuring a clean and oxidation-free bond. It involves heating the components in a vacuum environment to melt the brazing filler material, which then flows into the joint by capillary action. The process is highly controlled, requiring precise temperature management and a leak-free vacuum environment to prevent contamination. A vacuum brazing furnace is essential for this process, as it provides the necessary vacuum and heating conditions. The steps include loading the components, creating a vacuum, heating to the brazing temperature, and cooling under controlled conditions. This method is ideal for producing high-quality, contamination-free joints, especially in industries like aerospace and electronics.
Key Points Explained:
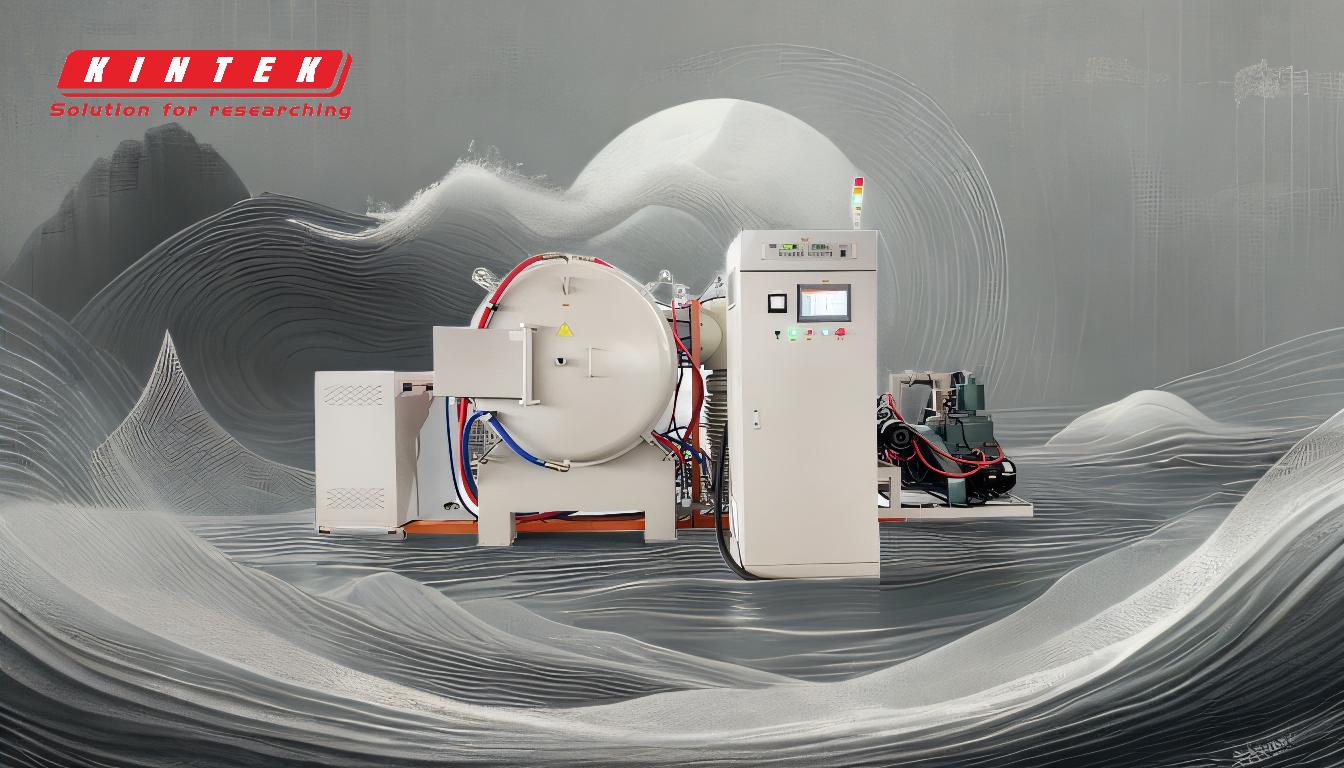
-
Loading the Furnace:
- The process begins by placing the assembled workpiece into the vacuum chamber of the vacuum brazing furnace. Proper alignment and placement are crucial to ensure even heating and effective brazing.
-
Creating a Vacuum:
- A mechanical vacuum pump is used to remove air and create a vacuum inside the chamber. This step is critical to prevent oxidation and contamination of the metals during the heating process. Once a certain vacuum level is achieved, a diffusion pump is connected to further enhance the vacuum.
-
Heating the Components:
- The furnace heats the components to the required brazing temperature. The heating system is controlled automatically by a temperature control instrument to ensure precise temperature management. This step melts the brazing filler material, allowing it to flow into the joint by capillary action.
-
Cooling and Finishing:
- After brazing, the components are cooled under controlled conditions, often using inert gases like argon to prevent oxidation. The cooling process must be carefully managed to avoid thermal stress and ensure the integrity of the brazed joint.
-
Leak Detection and Maintenance:
- Regular maintenance and leak detection are essential for the proper functioning of a vacuum brazing furnace. This includes checking for gas leaks, inspecting seals and valves, and replacing any worn or damaged components. Proper maintenance ensures consistent performance and extends the lifespan of the furnace.
-
Advantages of Vacuum Brazing:
- Vacuum brazing offers several advantages, including the ability to braze multiple pieces simultaneously, reduced flux usage, and the capability to process closed-shape parts. It also produces clean, high-quality joints free from oxidation and contamination.
-
Safety and Training:
- Operating a vacuum brazing furnace requires specialized training and experience. Proper safety protocols must be followed, including monitoring water pressure, flow, and temperature during operation. In case of water shutdown, a backup water supply system should be activated immediately to prevent damage to the furnace.
By following these steps and maintaining proper operational protocols, vacuum brazing can produce strong, reliable, and contamination-free joints, making it a preferred method in many high-precision industries.
Summary Table:
Step | Description |
---|---|
Loading the Furnace | Place the assembled workpiece into the vacuum chamber for even heating and effective brazing. |
Creating a Vacuum | Use mechanical and diffusion pumps to remove air, ensuring an oxidation-free environment. |
Heating Components | Heat to the brazing temperature, melting the filler material for capillary flow into the joint. |
Cooling and Finishing | Cool under controlled conditions using inert gases to prevent oxidation and thermal stress. |
Maintenance | Regularly inspect for leaks, replace worn parts, and ensure consistent furnace performance. |
Advantages | Clean, high-quality joints, reduced flux usage, and the ability to braze multiple pieces at once. |
Safety | Requires specialized training and adherence to safety protocols for optimal operation. |
Discover how vacuum brazing can enhance your metal joining process—contact our experts today!