Vapor deposition is a versatile process used to create thin films and coatings on substrates, primarily through two main techniques: Chemical Vapor Deposition (CVD) and Physical Vapor Deposition (PVD). Both methods involve the transformation of a material into a vapor phase, which is then deposited onto a substrate to form a thin film. CVD relies on chemical reactions to deposit materials, while PVD uses physical processes like sputtering or evaporation. The choice between CVD and PVD depends on the desired film properties, substrate material, and application requirements.
Key Points Explained:
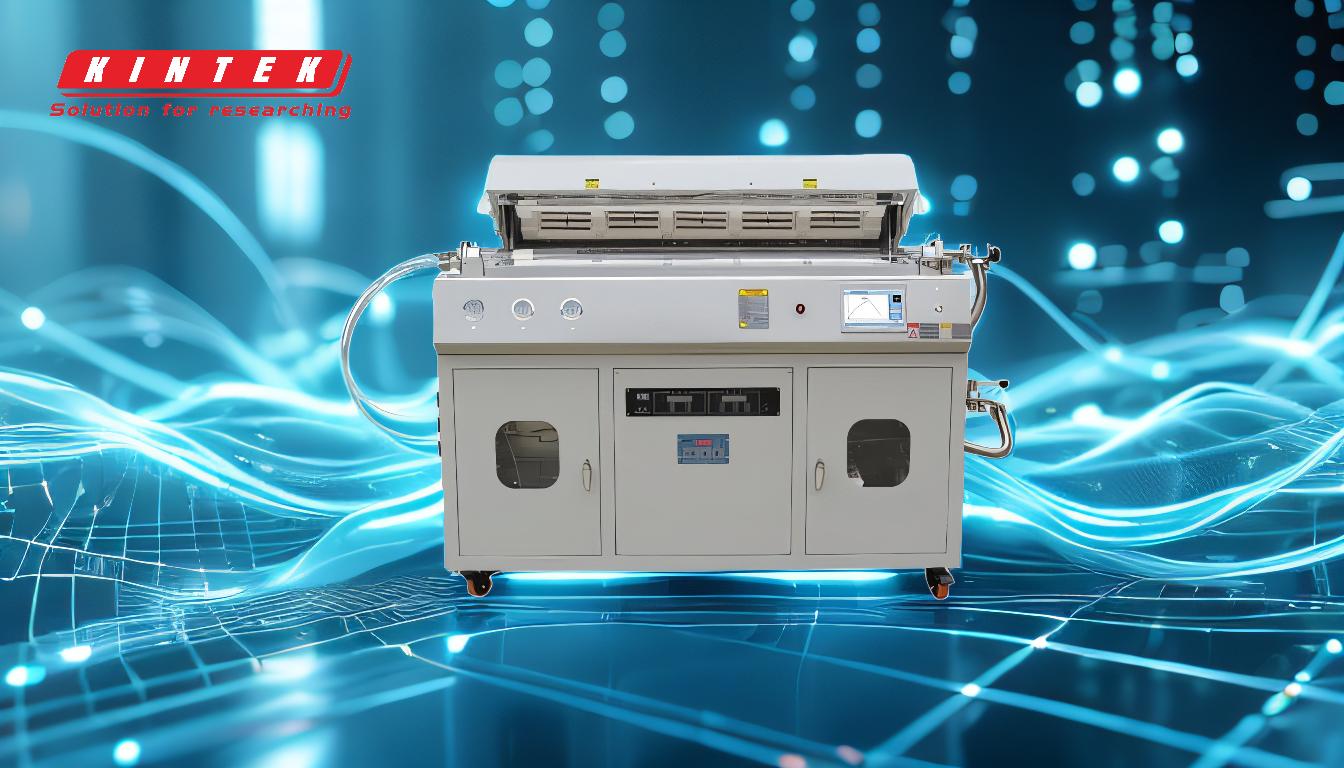
-
Chemical Vapor Deposition (CVD):
- Transport of Reacting Gaseous Species: The process begins with the transport of gaseous reactants to the substrate surface. These gases are typically introduced into a reaction chamber where they flow over the substrate.
- Adsorption on the Surface: Once the gaseous species reach the substrate, they adsorb onto its surface. This step is crucial as it allows the reactants to interact with the substrate.
- Surface-Catalyzed Reactions: The adsorbed species undergo chemical reactions on the substrate surface, often catalyzed by the surface itself. These reactions lead to the formation of the desired film material.
- Surface Diffusion and Growth: The reacted species diffuse across the surface to growth sites, where they nucleate and grow into a continuous film.
- Desorption and Removal of By-products: After the film has formed, any gaseous by-products desorb from the surface and are transported away from the reaction chamber.
-
Physical Vapor Deposition (PVD):
- Vaporization of the Material: In PVD, the material to be deposited is first vaporized. This can be achieved through various methods, such as sputtering or evaporation. In sputtering, high-energy ions bombard a solid target, ejecting atoms into the gas phase. In evaporation, the material is heated until it vaporizes.
- Introduction of Reactive Gas (Optional): In some PVD processes, a reactive gas is introduced into the chamber. This gas can react with the vaporized material to form a compound, which is then deposited onto the substrate.
- Deposition onto the Substrate: The vaporized atoms or molecules travel through the vacuum chamber and condense onto the substrate, forming a thin film. The film's properties, such as thickness and uniformity, can be controlled by adjusting process parameters like pressure, temperature, and deposition rate.
-
Sputtering in PVD:
- Ejection of Target Atoms: Sputtering involves bombarding a solid target (usually a metal) with high-energy ions. This bombardment ejects atoms from the target into the gas phase.
- Deposition of Atoms: The ejected atoms travel through the vacuum chamber and deposit onto the substrate, forming a thin film. Sputtering is widely used because it allows for precise control over the film's composition and properties.
-
Advantages of Vapor Deposition:
- Versatility: Both CVD and PVD can deposit a wide range of materials, including metals, ceramics, and polymers, onto various substrates.
- High-Quality Films: Vapor deposition techniques produce films with excellent uniformity, adhesion, and purity, making them suitable for applications in electronics, optics, and protective coatings.
- Controlled Deposition: The processes allow for precise control over film thickness, composition, and microstructure, enabling the creation of tailored coatings with specific properties.
-
Applications of Vapor Deposition:
- Electronics: CVD and PVD are used to deposit thin films in semiconductor manufacturing, such as the creation of conductive layers, insulating layers, and passivation coatings.
- Optics: Vapor deposition is used to create anti-reflective coatings, mirrors, and optical filters.
- Protective Coatings: PVD, in particular, is used to apply hard, wear-resistant coatings on tools, molds, and medical devices to improve their durability and performance.
In summary, vapor deposition is a critical technology in modern manufacturing, offering precise control over the deposition of thin films with tailored properties. Whether through chemical reactions in CVD or physical processes in PVD, these techniques enable the creation of high-quality coatings for a wide range of applications.
Summary Table:
Aspect | Chemical Vapor Deposition (CVD) | Physical Vapor Deposition (PVD) |
---|---|---|
Process | Relies on chemical reactions to deposit materials. | Uses physical processes like sputtering or evaporation. |
Key Steps | 1. Transport of gaseous reactants. 2. Adsorption. 3. Surface-catalyzed reactions. 4. Diffusion. | 1. Vaporization of material. 2. Optional reactive gas introduction. 3. Deposition onto substrate. |
Applications | Electronics, semiconductors, and high-purity films. | Optics, protective coatings, and wear-resistant layers. |
Advantages | High-quality films, precise control, and versatility. | Excellent uniformity, adhesion, and tailored properties. |
Discover how vapor deposition can enhance your manufacturing process—contact our experts today!