Running an electric kiln involves several cost factors, including electricity consumption, kiln size, firing frequency, and local electricity rates. The primary expense is the electricity used during firing cycles, which depends on the kiln's wattage, firing temperature, and duration. Smaller kilns (e.g., 120V) are cheaper to run but have limited capacity, while larger kilns (e.g., 240V) consume more power but are more efficient for bulk firing. On average, running an electric kiln can cost between $0.50 to $5 per firing, depending on these variables. Additional costs include maintenance, replacement elements, and potential upgrades to electrical systems to support higher voltage kilns.
Key Points Explained:
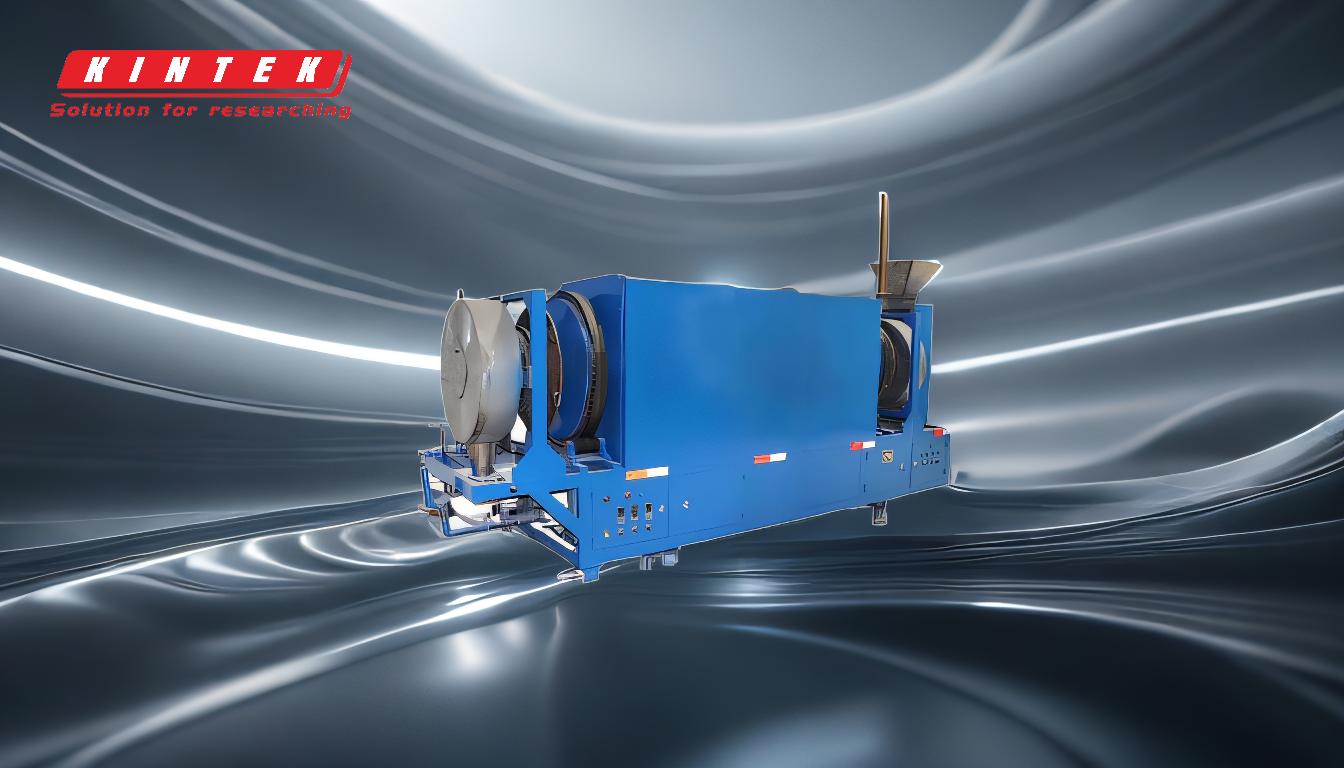
-
Electricity Consumption and Costs
- The primary cost of running an electric kiln is the electricity it consumes.
- Kilns typically range from 1,500 to 10,000 watts, with larger kilns requiring more power.
- The cost per firing depends on the kiln's wattage, firing temperature, and duration. For example, a 2,400-watt kiln running for 8 hours at $0.12 per kWh would cost approximately $2.30 per firing.
- Higher firing temperatures (e.g., cone 10) require more energy and thus increase costs.
-
Kiln Size and Voltage
- Smaller kilns (120V) are less expensive to operate but have limited capacity, making them suitable for hobbyists or small projects.
- Larger kilns (240V) are more energy-efficient for bulk firing but require higher upfront costs and may need electrical system upgrades.
- The size and voltage of the kiln directly impact both operational costs and firing efficiency.
-
Firing Frequency and Efficiency
- Frequent firing increases electricity costs, so optimizing kiln loads (e.g., firing multiple pieces at once) can reduce per-piece costs.
- Properly maintaining the kiln (e.g., replacing worn elements, ensuring tight seals) improves energy efficiency and reduces long-term costs.
-
Additional Costs
- Maintenance: Kiln elements, thermocouples, and relays may need periodic replacement, adding to operational costs.
- Electrical Upgrades: Larger kilns may require upgrading home electrical systems to support higher voltage, which can be a significant upfront expense.
- Insulation and Upgrades: Investing in better insulation or modern kiln controllers can improve efficiency and reduce long-term costs.
-
Cost Comparison with Other Kiln Types
- Electric kilns are generally more expensive to run than gas or wood-fired kilns due to higher electricity costs.
- However, electric kilns offer precise temperature control, cleaner operation, and lower maintenance compared to fuel-based kilns.
-
Practical Tips to Reduce Costs
- Optimize Loads: Fill the kiln to its capacity to maximize energy use per firing.
- Use Efficient Programs: Modern kiln controllers allow for programmable firing schedules that can save energy.
- Monitor Usage: Track electricity consumption to identify patterns and reduce unnecessary firing.
By understanding these factors, users can estimate the costs of running an electric kiln and implement strategies to optimize energy use and reduce expenses.
Summary Table:
Factor | Details |
---|---|
Electricity Costs | Depends on wattage, temperature, and duration. Costs range from $0.50–$5 per firing. |
Kiln Size & Voltage | Smaller kilns (120V) are cheaper but limited; larger kilns (240V) are more efficient for bulk firing. |
Firing Frequency | Frequent firing increases costs. Optimize loads to reduce per-piece expenses. |
Maintenance | Periodic replacement of elements, thermocouples, and relays adds to costs. |
Electrical Upgrades | Larger kilns may require upgrades to home electrical systems. |
Cost-Saving Tips | Optimize loads, use efficient programs, and monitor electricity consumption. |
Ready to optimize your kiln's efficiency? Contact us today for expert advice!