PVD (Physical Vapor Deposition) coating is a highly advanced and versatile surface treatment technology that offers numerous benefits, including enhanced durability, wear resistance, and environmental friendliness. However, it also comes with certain drawbacks, such as higher costs, slower processing rates, and limitations in coating complex geometries. Despite these challenges, PVD coating is widely used across industries like automotive, medical, and consumer goods due to its ability to significantly extend product lifespans and provide decorative finishes. Below, we explore the key aspects of PVD coating in detail.
Key Points Explained:
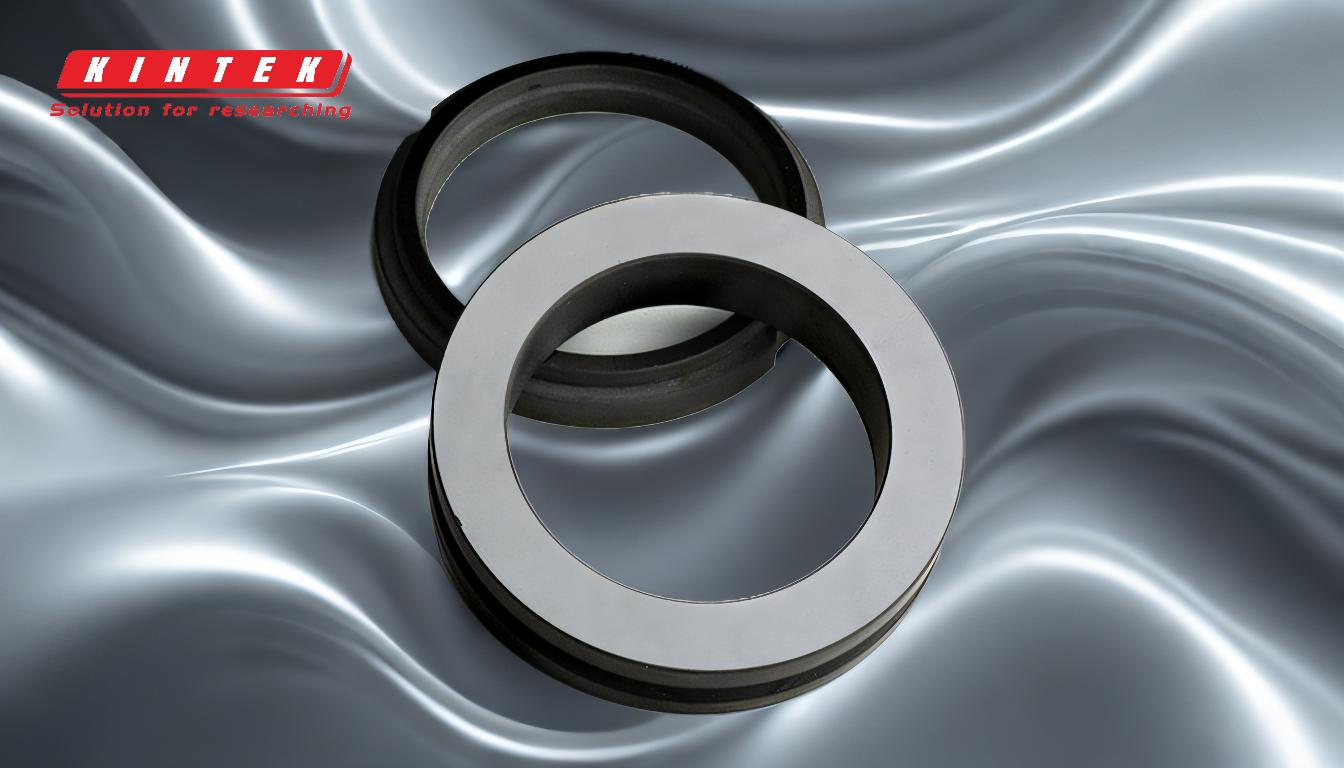
-
Advantages of PVD Coating:
- Enhanced Hardness and Wear Resistance: PVD coatings increase the hardness of substrate materials, making them more resistant to wear and tear. This is particularly beneficial for industrial tools, automotive parts, and medical instruments.
- High Adhesion: PVD coatings bond strongly to the substrate, ensuring long-lasting performance even under harsh conditions.
- Environmental Friendliness: Unlike traditional chrome plating, PVD coating does not produce toxic substances, making it a greener alternative.
- Versatility: PVD coatings can be applied to a wide range of materials, including metals, ceramics, and plastics, and are suitable for both functional and decorative applications.
- Low Processing Temperatures: The deposition process occurs at relatively low temperatures, making it ideal for heat-sensitive materials.
- Decorative Finishes: PVD coatings can create aesthetically pleasing finishes, such as gold, black, or bronze, which are popular in jewelry, architectural components, and consumer goods.
-
Disadvantages of PVD Coating:
- Higher Costs: The process requires specialized equipment, such as vacuum chambers and complex machines, which can be expensive to purchase and maintain. Additionally, skilled operators are needed, further increasing costs.
- Slow Processing Rates: PVD coating is relatively slow compared to other surface treatment methods, which can limit its efficiency for high-volume production.
- Line-of-Sight Limitation: PVD is a "line of sight" technique, meaning it can only coat surfaces directly exposed to the vapor stream. This makes it unsuitable for coating complex or internal geometries.
- Color Destruction: The process can sometimes alter or destroy colors, leading to material wastage and additional costs.
-
Applications of PVD Coating:
- Automotive Industry: Used for coating car parts like wheels, pistons, and engine components to enhance durability and corrosion resistance.
- Medical Equipment: Applied to surgical tools and implants to improve wear resistance and biocompatibility.
- Consumer Goods: Commonly used in kitchen and bath fixtures, writing instruments, jewelry, and eyeglass frames for both functional and decorative purposes.
- Industrial Tools: Extends the lifespan of drill bits, cutting tools, and other equipment by increasing hardness and reducing friction.
- Sporting Goods: Used in golf clubs, firearms, and marine hardware to improve performance and durability.
-
Cost Considerations:
- PVD coating costs vary depending on the method used. For example, evaporation is a lower-cost option, while ion beam sputtering and magnetron sputtering are more expensive but offer better scalability and performance.
-
Environmental and Ethical Benefits:
- PVD coating is a sustainable alternative to traditional chrome plating, as it does not produce harmful byproducts. It also significantly extends the lifespan of products, reducing waste and promoting ethical manufacturing practices.
In summary, PVD coating is a highly effective and environmentally friendly surface treatment technology with a wide range of applications. While it has some limitations, such as higher costs and slower processing rates, its benefits in terms of durability, versatility, and sustainability make it a valuable choice for many industries.
Summary Table:
Aspect | Details |
---|---|
Advantages | - Enhanced hardness and wear resistance |
- High adhesion
- Environmental friendliness
- Versatility
- Low processing temperatures
- Decorative finishes | | Disadvantages | - Higher costs
- Slow processing rates
- Line-of-sight limitation
- Color destruction | | Applications | - Automotive parts
- Medical equipment
- Consumer goods
- Industrial tools
- Sporting goods | | Cost Considerations | Varies by method (e.g., evaporation, ion beam sputtering, magnetron sputtering) | | Environmental Benefits| Sustainable alternative to chrome plating, extends product lifespan, reduces waste |
Ready to enhance your products with PVD coating? Contact our experts today to learn more!