Ceramics are known for their ability to withstand high temperatures, making them essential in applications ranging from industrial furnaces to aerospace components. The maximum temperature a ceramic can endure depends on its composition, structure, and intended use. Generally, ceramics can withstand temperatures ranging from 1,000°C to over 3,000°C, with specialized ceramics like silicon carbide and zirconia pushing the upper limits. Factors such as thermal shock resistance, chemical stability, and mechanical strength also play a role in determining their performance under extreme heat. Understanding these properties is crucial for selecting the right ceramic material for high-temperature applications.
Key Points Explained:
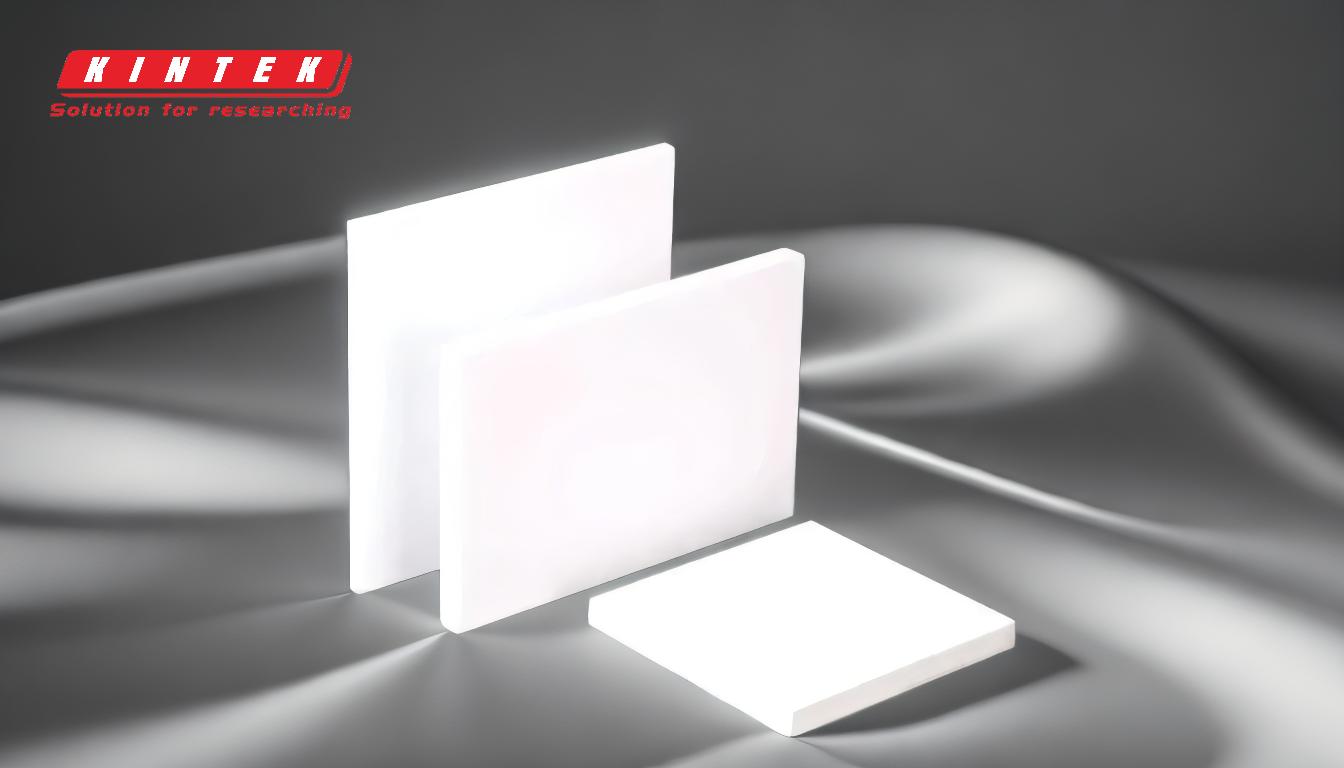
-
Temperature Resistance of Common Ceramics
- Different types of ceramics have varying temperature thresholds. For example:
- Alumina (Al₂O₃): Can withstand temperatures up to 1,800°C, commonly used in kiln linings and electrical insulators.
- Silicon Carbide (SiC): Can endure temperatures up to 2,700°C, ideal for high-temperature furnaces and aerospace components.
- Zirconia (ZrO₂): Stable up to 2,400°C, often used in thermal barrier coatings and refractory materials.
- Boron Nitride (BN): Can handle temperatures up to 2,000°C, used in high-temperature lubricants and crucibles.
- Different types of ceramics have varying temperature thresholds. For example:
-
Factors Influencing High-Temperature Performance
- Thermal Shock Resistance: The ability to withstand rapid temperature changes without cracking. Materials like silicon nitride excel in this area.
- Chemical Stability: Resistance to oxidation or reaction with other materials at high temperatures. Zirconia is highly stable in oxidizing environments.
- Mechanical Strength: The ability to maintain structural integrity under stress. Silicon carbide is known for its high strength at elevated temperatures.
-
Applications of High-Temperature Ceramics
- Industrial Furnaces: Ceramics like alumina and silicon carbide are used in kilns and furnaces due to their heat resistance.
- Aerospace: Components like turbine blades and heat shields rely on ceramics such as zirconia and silicon carbide.
- Energy: Ceramics are used in fuel cells and nuclear reactors for their ability to withstand extreme conditions.
-
Limitations and Challenges
- While ceramics are excellent for high-temperature applications, they can be brittle and prone to cracking under mechanical stress.
- Manufacturing high-performance ceramics can be costly and complex, requiring precise control over composition and processing.
-
Future Developments
- Research is ongoing to develop new ceramic materials with even higher temperature resistance and improved mechanical properties.
- Advances in nanotechnology and composite materials are expected to enhance the performance of ceramics in extreme environments.
By understanding the specific properties and limitations of different ceramics, engineers and purchasers can make informed decisions about the best materials for their high-temperature applications.
Summary Table:
Ceramic Type | Max Temperature | Key Applications |
---|---|---|
Alumina (Al₂O₃) | Up to 1,800°C | Kiln linings, electrical insulators |
Silicon Carbide (SiC) | Up to 2,700°C | High-temperature furnaces, aerospace components |
Zirconia (ZrO₂) | Up to 2,400°C | Thermal barrier coatings, refractory materials |
Boron Nitride (BN) | Up to 2,000°C | High-temperature lubricants, crucibles |
Need the perfect ceramic for your high-temperature application? Contact our experts today for tailored solutions!