Copper is a widely used metal due to its excellent thermal and electrical conductivity, and understanding the temperature required to melt it is crucial for various industrial and crafting applications. The melting point of pure copper is approximately 1085°C (1985°F). However, achieving this temperature in a furnace requires careful consideration of the furnace type, energy source, and the purity of the copper being melted. Different types of furnaces, such as electric, gas, or induction furnaces, can be used, each with its own efficiency and temperature control capabilities. Additionally, factors like the presence of impurities or alloying elements can slightly alter the melting point. Ensuring the furnace can consistently reach and maintain the required temperature is essential for successful melting and casting processes.
Key Points Explained:
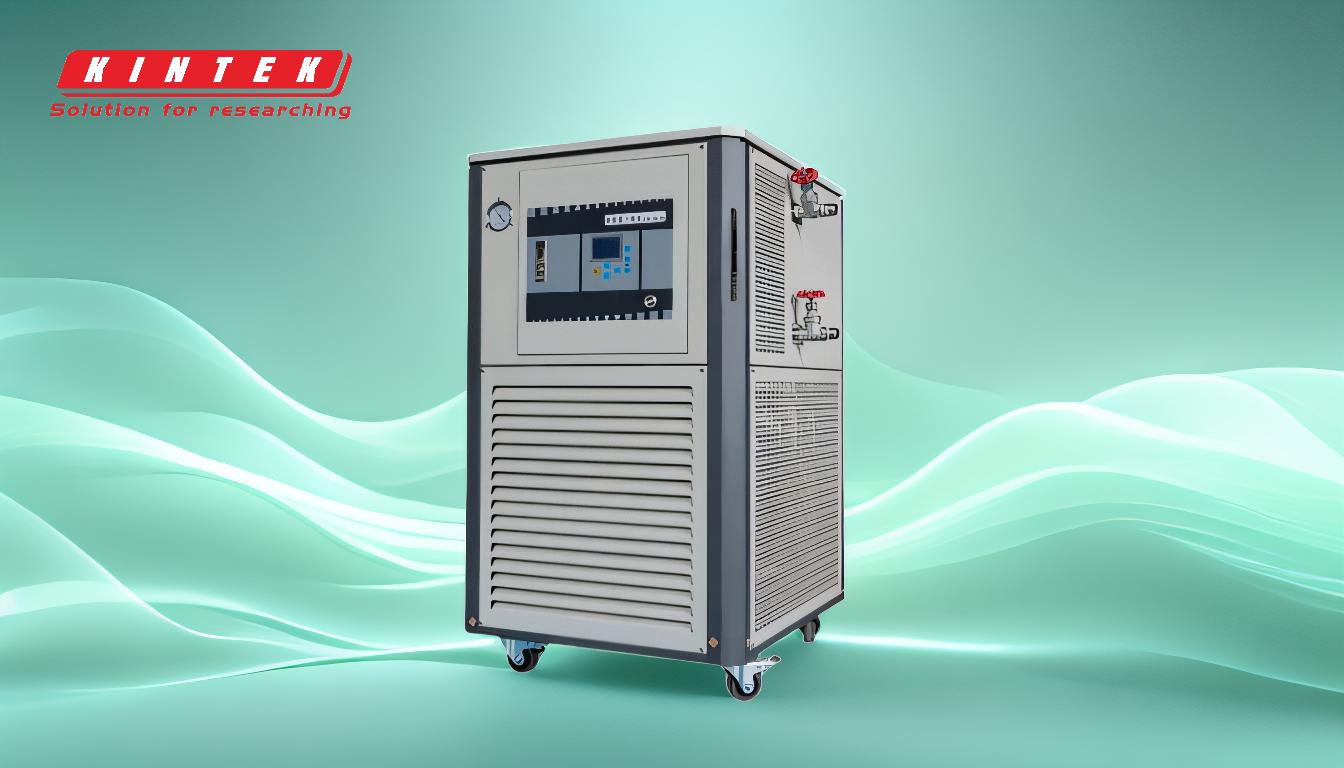
-
Melting Point of Copper:
- The melting point of pure copper is 1085°C (1985°F). This is the temperature at which solid copper transitions into a liquid state.
- This value is critical for determining the furnace specifications needed for melting copper.
-
Factors Affecting the Melting Point:
- Purity of Copper: Pure copper has a well-defined melting point, but the presence of impurities or alloying elements (e.g., tin, zinc) can lower or raise the melting temperature slightly.
- Oxidation: Copper can oxidize at high temperatures, forming copper oxide, which may affect the melting process and require additional considerations like protective atmospheres or fluxes.
-
Types of Furnaces Suitable for Melting Copper:
- Electric Furnaces: These furnaces are highly efficient and provide precise temperature control, making them ideal for melting copper. They can easily reach temperatures above 1200°C, ensuring the copper melts completely.
- Gas Furnaces: Propane or natural gas furnaces are also commonly used. They are cost-effective and can achieve the necessary temperatures, but they require proper ventilation and safety measures.
- Induction Furnaces: These are highly efficient and provide rapid heating, making them suitable for industrial applications. They are particularly useful for melting smaller quantities of copper quickly.
-
Energy Requirements and Efficiency:
- The energy required to melt copper depends on the furnace type and its insulation. Efficient furnaces minimize heat loss and reduce energy consumption.
- Insulation materials like ceramic fiber or refractory bricks are often used to maintain high temperatures and improve efficiency.
-
Safety Considerations:
- Melting copper involves extremely high temperatures, so proper safety gear, including heat-resistant gloves, face shields, and aprons, is essential.
- Adequate ventilation is necessary to prevent the buildup of harmful fumes, especially when using gas furnaces or fluxes.
-
Applications of Molten Copper:
- Molten copper is used in various industries, including electronics (for wiring and circuit boards), construction (for plumbing and roofing), and art (for casting sculptures).
- The ability to melt copper efficiently is crucial for these applications, as it ensures the metal can be shaped and molded as needed.
-
Temperature Control and Monitoring:
- Accurate temperature control is vital to avoid overheating, which can lead to excessive oxidation or even vaporization of the copper.
- Thermocouples and digital controllers are commonly used to monitor and maintain the desired temperature within the furnace.
-
Environmental and Economic Considerations:
- Using energy-efficient furnaces not only reduces operational costs but also minimizes environmental impact.
- Recycling copper scrap by melting it in a furnace is an eco-friendly practice that conserves resources and reduces waste.
By understanding these key points, you can select the appropriate furnace and ensure a safe and efficient process for melting copper. Whether you're working on a small-scale project or an industrial application, achieving the correct temperature is fundamental to success.
Summary Table:
Key Factor | Details |
---|---|
Melting Point of Copper | 1085°C (1985°F) |
Furnace Types | Electric, Gas, Induction |
Energy Efficiency | Minimize heat loss with proper insulation (e.g., ceramic fiber) |
Safety Measures | Heat-resistant gear, ventilation, and protective atmospheres |
Applications | Electronics, construction, art casting |
Temperature Control | Use thermocouples and digital controllers for precision |
Environmental Impact | Energy-efficient furnaces reduce costs and environmental footprint |
Ready to melt copper efficiently? Contact our experts today for tailored furnace solutions!