Ash content determination using a muffle furnace is a widely used method, particularly in industries like food, polymers, and materials research. The process involves heating a sample at high temperatures (typically up to 900°C) to burn off organic matter, leaving behind inorganic residues (ash). The ash content is then calculated using the weight difference before and after ashing. This method is preferred for its precision, ability to isolate samples from contaminants, and suitability for materials stable at high temperatures. The process includes steps like preliminary cauterization, cooling, dissolving water-soluble salts, drying, and re-cauterization to achieve constant weight.
Key Points Explained:
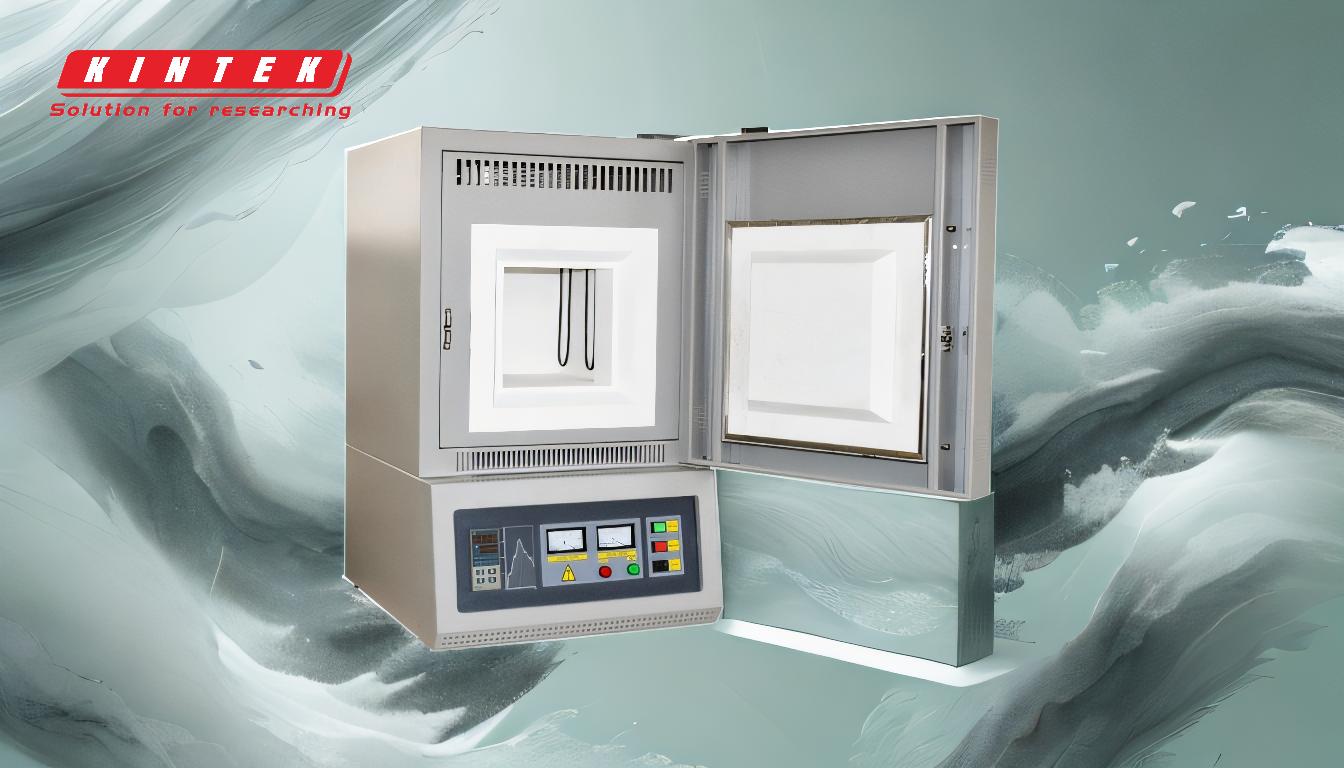
-
Purpose of Ash Content Determination:
- Ash content is a measure of the inorganic residue left after burning organic matter in a sample.
- It is a critical parameter in industries like food, polymers, and materials research to assess purity, quality, and composition.
-
Dry Ashing Method:
- Dry ashing is the most common method for ash determination using a muffle furnace.
- It involves heating the sample at high temperatures (typically 500°C–900°C) to oxidize organic components, leaving inorganic residues.
- The method is suitable for materials stable at high temperatures, such as polymers and rubbers.
-
Steps in Ash Content Determination:
- Sample Preparation: Weigh the sample accurately before ashing (M(dry)).
- Preliminary Cauterization: Place the sample in a crucible and heat it in the muffle furnace to burn off organic matter.
- Cooling: Remove the sample and allow it to cool.
- Dissolving Water-Soluble Salts: Add deionized water to dissolve water-soluble salts and expose encapsulated carbon particles.
- Drying and Re-Cauterization: Evaporate the water on a water bath, dry the sample in an oven at 120°C–130°C, and re-cauterize to achieve constant weight.
- Final Weighing: Weigh the sample after ashing (M(ash)).
-
Calculation of Ash Content:
- The ash content is calculated using the formula:
[
\text{Ash content (%)} = \frac{M(\text{ash})}{M(\text{dry})} \times 100
]
where:
- ( M(\text{ash}) ) = weight of the sample after ashing.
- ( M(\text{dry}) ) = weight of the sample before ashing.
- The ash content is calculated using the formula:
[
\text{Ash content (%)} = \frac{M(\text{ash})}{M(\text{dry})} \times 100
]
where:
-
Advantages of Using a Muffle Furnace:
- Precise Temperature Control: Ensures consistent and accurate results.
- Isolation from Contaminants: The enclosed chamber prevents contamination from combustion byproducts.
- Versatility: Suitable for a wide range of materials, including polymers, rubbers, and food products.
-
Considerations for Accurate Results:
- Sample Stability: Ensure the sample is stable at high temperatures to avoid decomposition or volatilization.
- Crucible Selection: Use crucibles made of materials resistant to high temperatures, such as porcelain or platinum.
- Cooling and Handling: Allow the sample to cool in a desiccator to prevent moisture absorption, which can affect the final weight.
-
Comparison with Other Methods:
- Wet Ashing: Involves using acids to dissolve organic matter, suitable for samples that may decompose at high temperatures.
- Low-Temperature Ashing: Uses plasma or oxygen at lower temperatures, ideal for heat-sensitive materials.
- Dry ashing is preferred for its simplicity, cost-effectiveness, and suitability for high-temperature-stable materials.
-
Applications of Ash Content Determination:
- Food Industry: To assess mineral content and quality of food products.
- Polymers and Rubbers: To evaluate inorganic filler content and material composition.
- Materials Research: To analyze the purity and composition of various materials.
By following these steps and considerations, ash content determination using a muffle furnace provides reliable and accurate results, making it a valuable technique in various industries.
Summary Table:
Key Aspect | Details |
---|---|
Purpose | Measure inorganic residue to assess purity, quality, and composition. |
Method | Dry ashing at 500°C–900°C to oxidize organic matter. |
Steps | Sample preparation, cauterization, cooling, dissolving salts, re-cauterization, final weighing. |
Calculation | Ash content (%) = (M(ash) / M(dry)) × 100. |
Advantages | Precise temperature control, contamination-free, versatile. |
Applications | Food industry, polymers, rubbers, materials research. |
Need assistance with ash content determination? Contact our experts today for reliable solutions!