Deposition is a critical process in integrated circuit (IC) fabrication, enabling the creation of high-quality, high-performance solid materials and thin films. It plays a vital role in forming the layers and structures necessary for semiconductor devices, such as transistors, interconnects, and insulating layers. Deposition techniques like Chemical Vapor Deposition (CVD), Plasma-Enhanced CVD (PECVD), and High-Density Plasma CVD (HDP-CVD) are used to deposit materials such as aluminum, tungsten, and dielectrics onto substrates. These processes allow for precise control over material properties, thickness, and uniformity, which are essential for achieving the desired electrical and mechanical performance of ICs. Additionally, innovative methods like aerosol deposition offer room-temperature processing solutions, expanding the range of substrates and materials that can be used in semiconductor fabrication.
Key Points Explained:
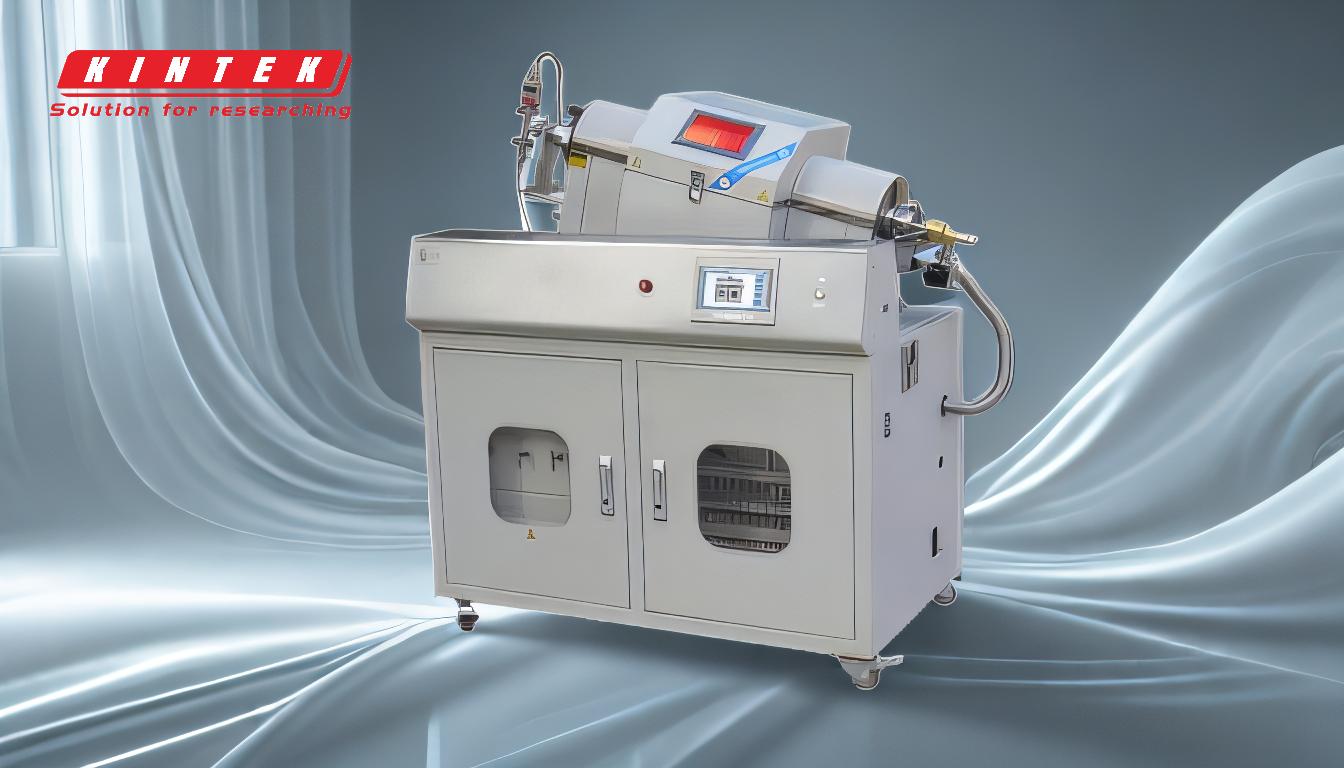
-
Creation of Thin Films and Layers:
- Deposition is used to form thin films and layers on semiconductor substrates, which are essential for building the intricate structures of ICs.
- Techniques like CVD, PECVD, and HDP-CVD enable the deposition of materials such as aluminum, tungsten, and dielectrics.
- These layers serve various functions, including conducting electricity (interconnects), insulating between layers (dielectrics), and forming the active regions of transistors.
-
Precision and Control:
- Deposition processes allow for precise control over the thickness, uniformity, and composition of the deposited materials.
- This precision is critical for ensuring the performance, reliability, and miniaturization of modern ICs.
- For example, CVD tungsten is used to create uniform and conformal layers in high-aspect-ratio structures, which are common in advanced IC designs.
-
Material Versatility:
- Deposition techniques can be used with a wide range of materials, including metals, semiconductors, and insulators.
- This versatility enables the fabrication of complex multi-layer structures with tailored electrical, thermal, and mechanical properties.
- For instance, aluminum is commonly used for interconnects due to its excellent conductivity, while dielectric materials like silicon dioxide provide electrical insulation.
-
Innovative Deposition Methods:
- New techniques like aerosol deposition offer unique advantages, such as room-temperature processing.
- This is particularly beneficial for substrates with low melting points or polymers, which cannot withstand high-temperature processes.
- Aerosol deposition opens up new possibilities for high-technology semiconductor applications and expands the range of materials that can be used in IC fabrication.
-
Modification of Material Properties:
- Deposition processes can modify the properties of existing materials, such as improving conductivity, adhesion, or thermal stability.
- This capability is crucial for meeting the increasing demand for versatile and high-performance materials in the semiconductor industry.
- For example, plasma-enhanced CVD can deposit high-quality dielectric films with improved step coverage and adhesion.
-
Enabling Advanced IC Technologies:
- Deposition is integral to the development of advanced IC technologies, such as 3D NAND flash memory and FinFET transistors.
- These technologies rely on the ability to deposit thin, uniform layers with precise control over their properties.
- Without advanced deposition techniques, it would be impossible to achieve the performance and density requirements of modern semiconductor devices.
In summary, deposition is a cornerstone of IC fabrication, enabling the creation of high-quality thin films and layers with precise control over their properties. It supports the development of advanced semiconductor technologies and offers innovative solutions for challenging materials and substrates. By leveraging deposition techniques, the semiconductor industry can continue to push the boundaries of performance, miniaturization, and functionality in ICs.
Summary Table:
Key Aspect | Details |
---|---|
Thin Film Creation | Forms layers for transistors, interconnects, and insulating layers. |
Precision & Control | Ensures uniformity, thickness, and material properties for IC performance. |
Material Versatility | Works with metals, semiconductors, and insulators for tailored properties. |
Innovative Methods | Aerosol deposition enables room-temperature processing for sensitive substrates. |
Material Property Modification | Enhances conductivity, adhesion, and thermal stability. |
Advanced IC Technologies | Supports 3D NAND, FinFET, and other high-performance semiconductor devices. |
Ready to optimize your IC fabrication process? Contact our experts today to learn more about advanced deposition solutions!