Graphene synthesis via Chemical Vapor Deposition (CVD) is a widely used method for producing high-quality, large-area graphene. The process involves the decomposition of carbon precursors on a catalytic substrate, typically copper or nickel, under controlled atmospheric conditions. The carbon atoms then reorganize into a hexagonal lattice to form graphene. The CVD method is highly scalable and cost-effective, making it a preferred choice for industrial applications. Below is a detailed explanation of the key steps and mechanisms involved in graphene production using CVD.
Key Points Explained:
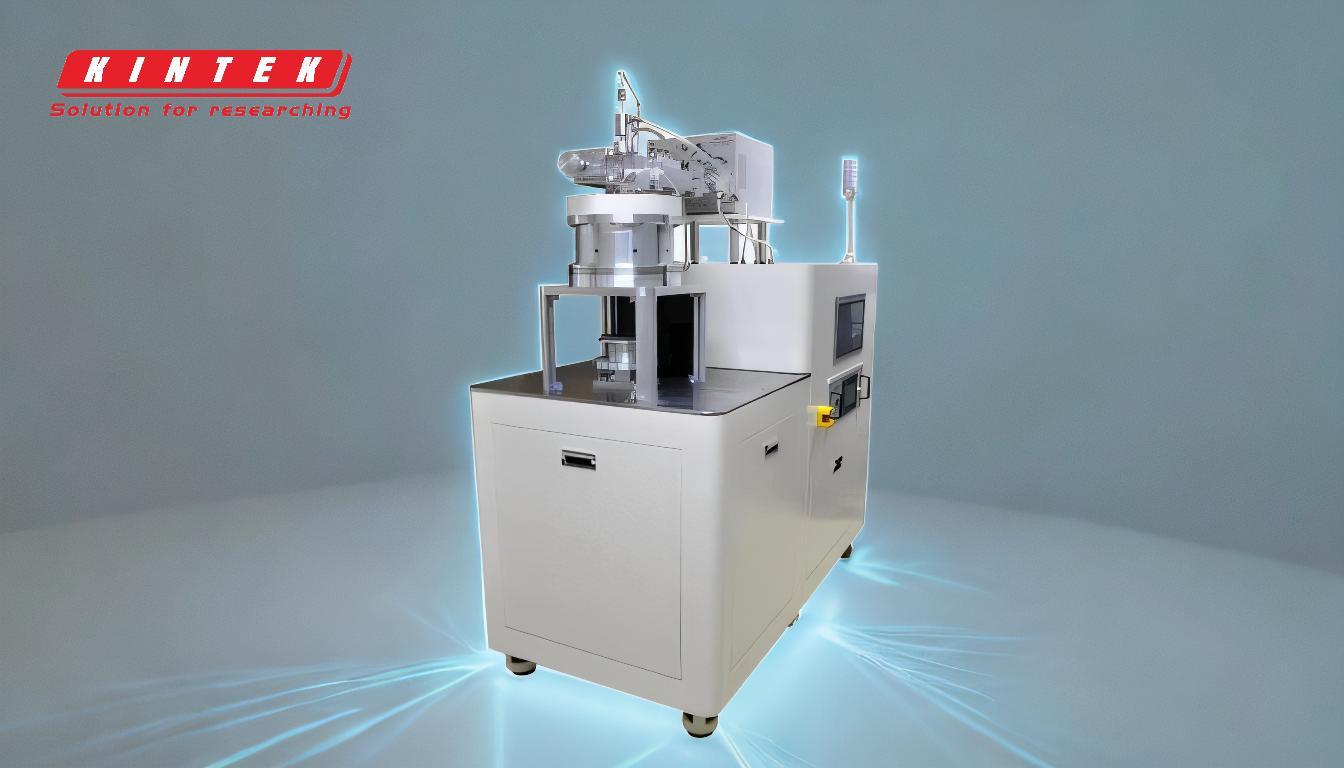
-
Role of the Catalyst Substrate
- The catalyst substrate (usually copper or nickel) plays a critical role in the CVD process.
- Copper is preferred for monolayer graphene due to its low carbon solubility, which limits carbon diffusion into the bulk and promotes surface adsorption.
- Nickel, with its higher carbon solubility, allows carbon atoms to dissolve into the metal and segregate upon cooling, forming graphene layers.
- The choice of substrate depends on the desired graphene quality and layer thickness.
-
Precursor Adsorption and Decomposition
- A hydrocarbon gas (e.g., methane) is introduced as the carbon precursor.
- The precursor molecules adsorb onto the catalyst surface and decompose into carbon species under high temperatures (typically 900–1000°C).
- This decomposition is facilitated by the catalytic properties of the substrate and the presence of carrier gases like hydrogen (H2) and argon (Ar).
-
Carbon Diffusion and Nucleation
- On copper substrates, carbon atoms remain on the surface due to low solubility, forming small carbon clusters.
- On nickel substrates, carbon atoms diffuse into the metal and later segregate to the surface during cooling.
- Once the carbon clusters exceed a critical size, they nucleate into graphene crystals.
-
Graphene Growth Mechanism
- The nucleated graphene crystals grow as carbon species continue to attach to their edges.
- The growth process is influenced by factors such as temperature, gas flow rates, and substrate properties.
- On copper, the process typically results in monolayer graphene, while nickel can produce multilayer graphene due to carbon segregation.
-
Cooling and Graphene Formation
- After the growth phase, the system is cooled in an inert gas (e.g., argon) to stabilize the graphene structure.
- On nickel, cooling causes dissolved carbon to segregate and form graphene layers on the surface.
- On copper, the graphene layer remains intact on the surface without significant diffusion.
-
Advantages of CVD for Graphene Production
- Scalability: CVD can produce large-area graphene films suitable for industrial applications.
- Quality: The method yields high-quality, defect-free graphene with excellent electrical and mechanical properties.
- Cost-Effectiveness: Compared to other methods like mechanical exfoliation, CVD is relatively inexpensive and efficient.
-
Challenges and Considerations
- Substrate Selection: The choice of substrate (Cu vs. Ni) affects graphene thickness and quality.
- Process Optimization: Precise control of temperature, gas flow rates, and cooling rates is essential for consistent results.
- Transfer Process: Graphene must often be transferred from the growth substrate to a target substrate, which can introduce defects or contamination.
In summary, the CVD method for graphene production is a highly controlled and scalable process that leverages the catalytic properties of metal substrates to decompose carbon precursors and form high-quality graphene. By carefully optimizing parameters such as substrate choice, temperature, and gas composition, researchers and manufacturers can produce graphene with tailored properties for various applications, including electronics, sensors, and energy storage.
Summary Table:
Key Aspect | Details |
---|---|
Catalyst Substrate | Copper (monolayer) or nickel (multilayer) for graphene quality and thickness. |
Precursor Decomposition | Hydrocarbon gas (e.g., methane) decomposes at high temperatures (900–1000°C). |
Carbon Diffusion | Cu: surface adsorption; Ni: diffusion into metal and segregation upon cooling. |
Graphene Growth | Nucleation and growth influenced by temperature, gas flow, and substrate. |
Cooling Process | Stabilized with inert gas (e.g., argon) to form graphene layers. |
Advantages | Scalable, high-quality, cost-effective, and suitable for industrial use. |
Challenges | Substrate selection, process optimization, and transfer process risks. |
Discover how CVD can revolutionize your graphene production—contact our experts today!