The lifespan of a crucible depends on several factors, including the material of the crucible, the operating conditions, and the specific application. Graphite crucibles, for example, are known for their long service life due to their excellent thermal stability, corrosion resistance, and ability to withstand thermal shock. They can endure temperatures exceeding 2000°C, making them suitable for high-temperature applications. However, the actual lifespan can vary based on factors such as the type of furnace, the melting and holding temperatures, the rate of temperature changes, and the specific materials being melted. Proper selection, maintenance, and operational practices are crucial to maximizing the lifespan of a crucible.
Key Points Explained:
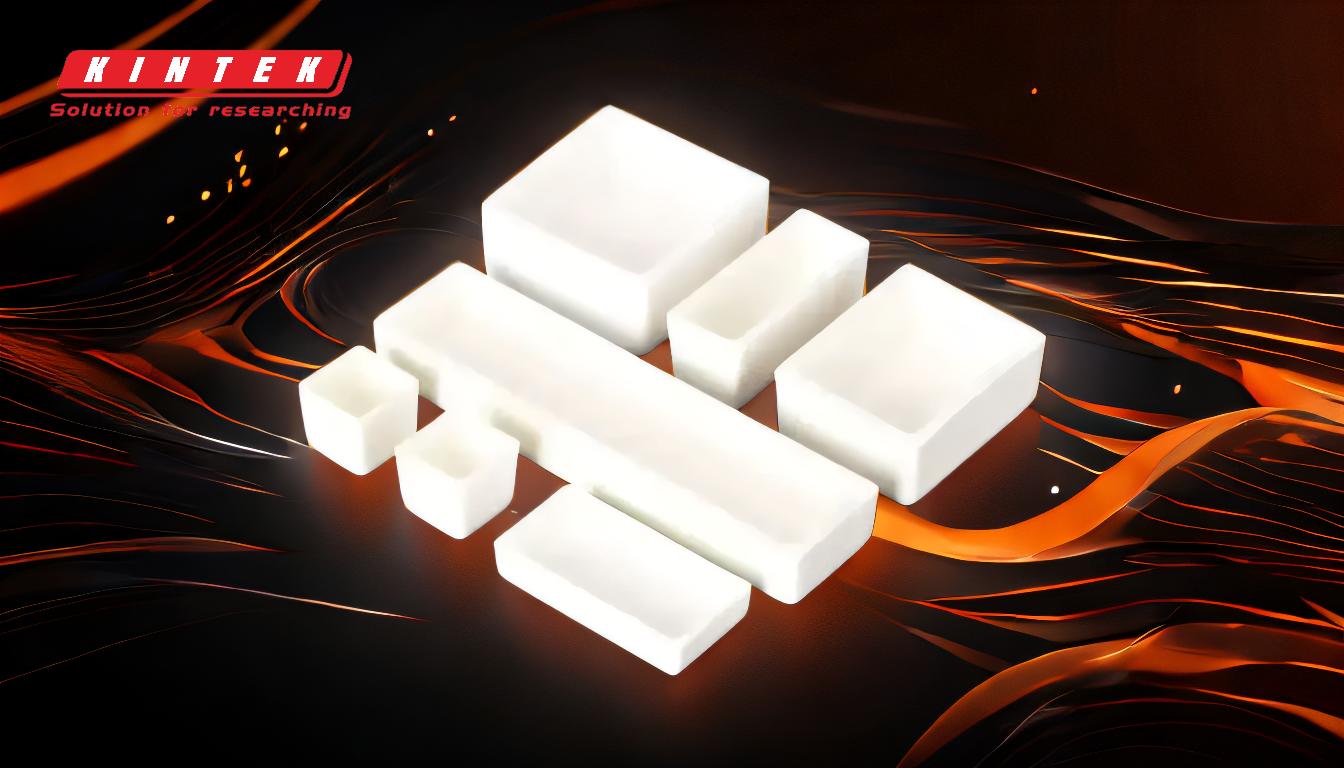
-
Material of the Crucible:
- Graphite Crucibles: Known for their long service life due to excellent thermal stability, corrosion resistance, and ability to withstand thermal shock. They can endure temperatures exceeding 2000°C.
- Silicon Carbide Crucibles: These crucibles are also durable and can withstand high temperatures, but their lifespan can be influenced by factors such as furnace atmosphere, watt density, and operating temperature.
-
Operating Conditions:
- Temperature: The melting and holding temperatures significantly impact the lifespan of a crucible. Higher temperatures can accelerate wear and tear.
- Thermal Shock: Rapid temperature changes can cause thermal shock, which can shorten the lifespan of a crucible. Graphite crucibles are particularly resistant to thermal shock.
- Furnace Atmosphere: The environment inside the furnace, including the presence of corrosive gases, can affect the crucible's durability.
-
Specific Application:
- Type of Alloy: The specific alloy or range of alloys being melted can influence the lifespan of a crucible. Some alloys may be more corrosive or require higher temperatures, which can wear down the crucible faster.
- Fluxes and Additions: The use of fluxes or other additions can also impact the crucible's lifespan. Some fluxes can be corrosive or cause buildup that affects the crucible's performance.
- Degassing and Refining Processes: These processes can introduce additional stresses on the crucible, potentially reducing its lifespan.
-
Maintenance and Operational Practices:
- Frequency of Maintenance: Regular maintenance, such as cleaning and inspecting the crucible, can help extend its lifespan.
- Charging and Emptying: The methods used to charge and empty the crucible can also affect its durability. Proper handling can minimize physical damage.
- Avoiding Cross-Contamination: Ensuring that the crucible is used for compatible materials can prevent contamination and extend its useful life.
-
Furnace Type and Design:
- Induction Furnaces: The electrical characteristics of the crucible must match the operating frequency of the furnace. Mismatched crucibles can overheat and fail prematurely.
- Crucible Furnaces: These furnaces are designed to hold the crucible within a heat source. The design and materials of the furnace can influence the crucible's performance and lifespan.
-
Environmental Factors:
- Atmospheric Conditions: The presence of moisture, oxygen, or other reactive gases can affect the crucible's integrity over time.
- Mechanical Stress: Physical impacts or vibrations during operation can cause cracks or other damage to the crucible.
In summary, the lifespan of a crucible is influenced by a combination of material properties, operating conditions, specific applications, maintenance practices, and environmental factors. By carefully selecting the appropriate crucible for the intended use and adhering to best practices in operation and maintenance, it is possible to maximize the crucible's service life.
Summary Table:
Factor | Impact on Crucible Lifespan |
---|---|
Material | Graphite crucibles offer thermal stability and corrosion resistance; silicon carbide is durable. |
Operating Conditions | High temperatures, thermal shock, and furnace atmosphere affect durability. |
Specific Application | Alloy type, fluxes, and degassing processes influence wear and tear. |
Maintenance Practices | Regular cleaning, proper handling, and avoiding cross-contamination extend lifespan. |
Furnace Type | Induction and crucible furnaces require compatible crucibles to prevent overheating. |
Environmental Factors | Moisture, oxygen, and mechanical stress can degrade crucible integrity. |
Need help selecting the right crucible for your application? Contact our experts today!