PVD (Physical Vapor Deposition) coatings are renowned for their exceptional durability, making them a popular choice for watch coatings. The lifespan of PVD coatings on watches can vary significantly, typically ranging from 10 years to several decades, depending on factors such as the substrate material, coating thickness, bond strength, and environmental conditions. Proper maintenance and care can further extend the longevity of the coating, ensuring it remains resistant to scratches, corrosion, and wear over time. PVD coatings are considered superior to traditional finishes, offering unmatched durability and protection for watches.
Key Points Explained:
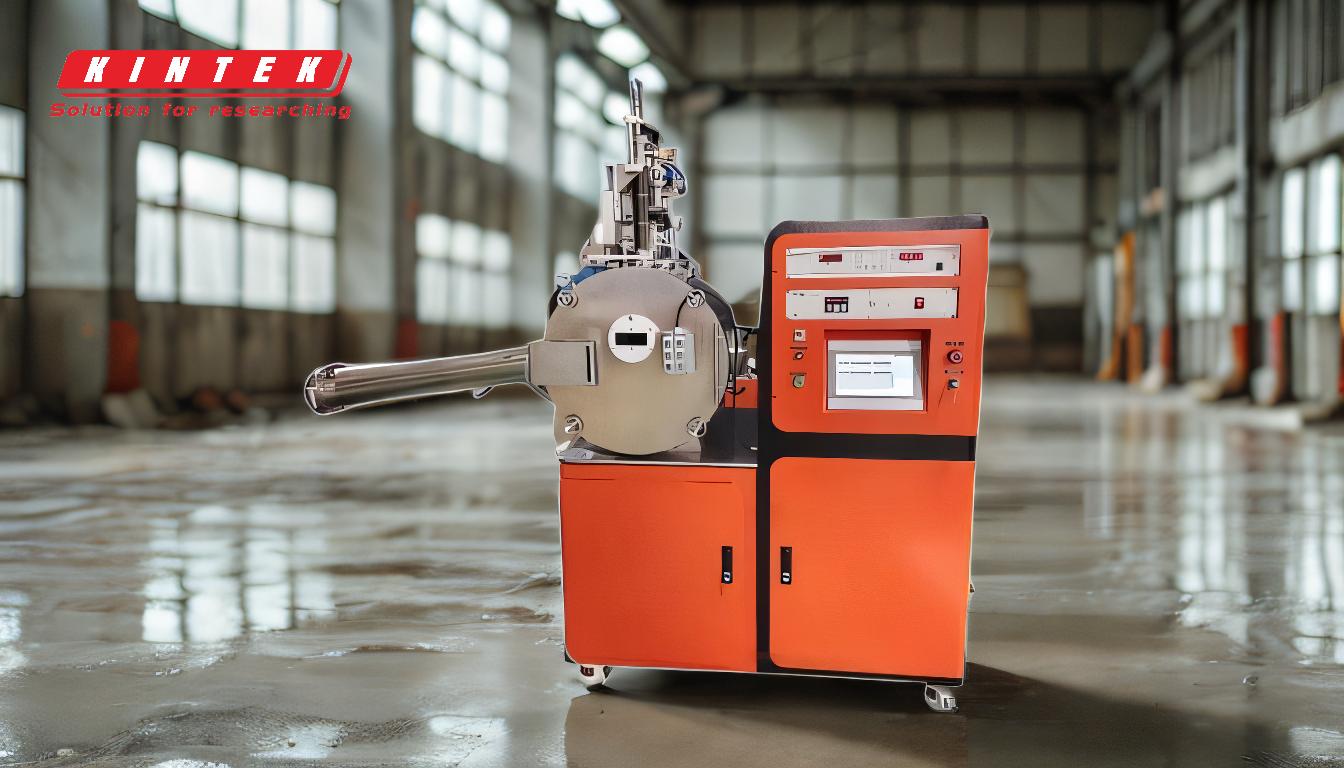
-
Durability of PVD Coatings
- PVD coatings are highly durable, with robust resistance to abrasion, corrosion, and impact.
- They are considered the most durable coating available today, outperforming traditional finishes.
- The hardness of PVD coatings ensures they can withstand daily wear and tear, making them ideal for watches.
-
Factors Affecting Lifespan
- Substrate Material: The type of material the coating is applied to (e.g., stainless steel, titanium) influences its longevity.
- Coating Thickness: Thicker coatings generally last longer but must balance with aesthetic and functional requirements.
- Bond Strength: The adhesion between the coating and the substrate is critical; stronger bonds enhance durability.
- Environmental Conditions: Exposure to high temperatures, chemicals, or abrasive environments can affect the coating's lifespan.
-
Typical Lifespan of PVD Coatings on Watches
- In the jewelry and watch industry, PVD coatings can last up to 10 years with proper application and maintenance.
- Under optimal conditions, PVD coatings can last decades or even hundreds of years, depending on the factors mentioned above.
-
Advantages Over Traditional Finishes
- PVD coatings are scratch-resistant, ensuring the watch retains its appearance over time.
- They are corrosion-resistant, protecting the watch from moisture and environmental damage.
- PVD coatings provide a long-lasting finish that outlasts traditional plating methods.
-
Maintenance Tips to Extend Lifespan
- Avoid exposing the watch to harsh chemicals or abrasive materials.
- Clean the watch regularly with a soft cloth to remove dirt and oils.
- Store the watch in a dry, safe place when not in use to prevent unnecessary wear.
In summary, PVD coatings on watches are highly durable and can last for many years, provided they are applied correctly and maintained properly. Their superior resistance to scratches, corrosion, and wear makes them an excellent choice for enhancing the longevity and appearance of watches.
Summary Table:
Aspect | Details |
---|---|
Durability | Highly resistant to scratches, corrosion, and wear. |
Lifespan | 10 years to several decades, depending on application and maintenance. |
Key Factors | Substrate material, coating thickness, bond strength, environmental conditions. |
Advantages | Scratch-resistant, corrosion-resistant, long-lasting finish. |
Maintenance Tips | Avoid harsh chemicals, clean regularly, store properly. |
Ensure your watch stays protected and stylish—contact us today for expert advice on PVD coatings!