PVD (Physical Vapor Deposition) plating is known for its durability, corrosion resistance, and ability to retain the original shape of the product while providing a rich finish. The lifespan of PVD plating varies depending on factors such as the substrate material, coating thickness, bond strength, and exposure to environmental conditions like heat, wear, and abrasion. In the jewelry industry, for example, PVD coatings can last up to 10 years with proper application and maintenance. However, aggressive attacks can damage the color, which may not always be repairable. Overall, PVD coatings are highly durable and resistant to corrosion and scratching, making them a long-lasting solution for many applications.
Key Points Explained:
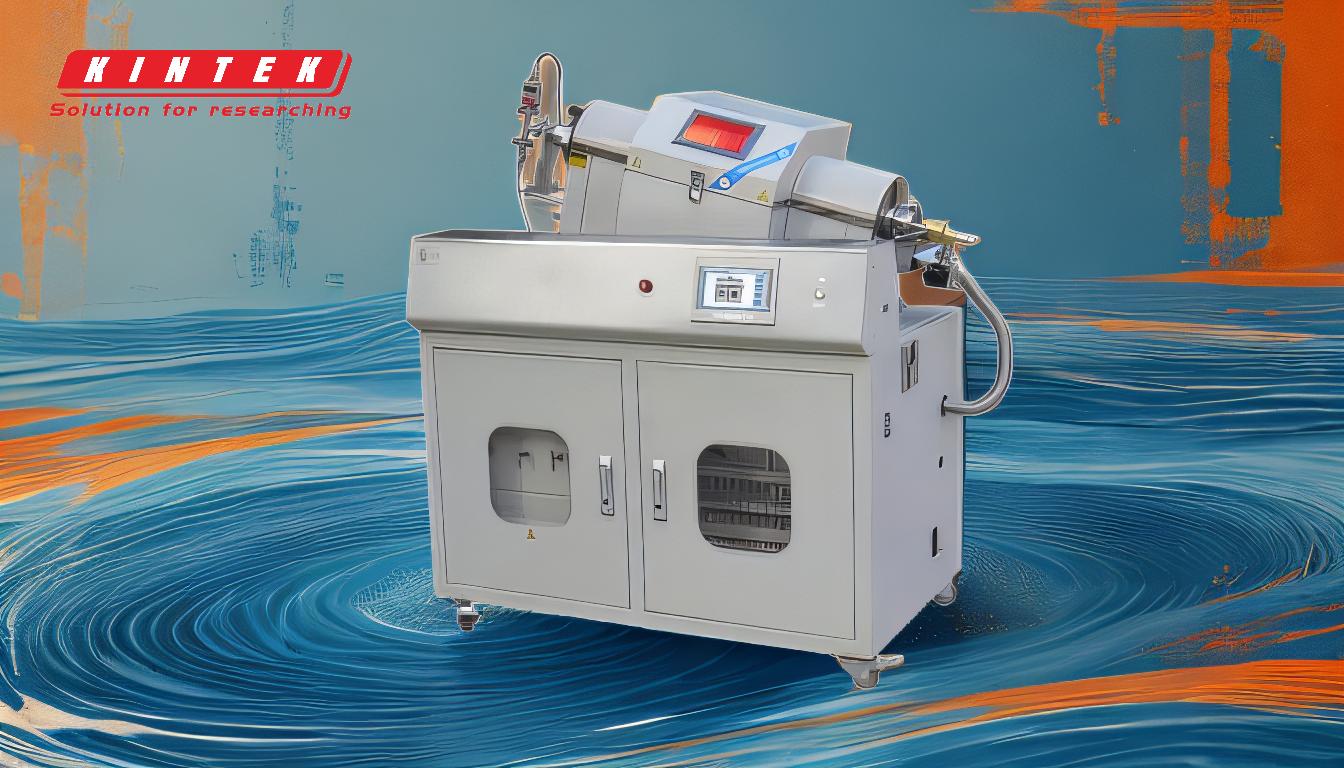
-
Durability and Resistance of PVD Coatings:
- PVD coatings are extremely thin yet strong, offering high levels of corrosion, temperature, and abrasion resistance. This makes them suitable for applications where durability is critical.
- The vacuum environment during the PVD process eliminates contamination, ensuring a stronger bond between the coating and the substrate. This bond enhances the coating's resistance to scratching and wear.
-
Lifespan in Different Applications:
- In the jewelry industry, PVD coatings can last up to 10 years when applied correctly and maintained properly. This longevity is attributed to the coating's resistance to environmental factors and wear.
- The lifespan of PVD coatings can vary significantly depending on the application. For example, coatings used in industrial settings may experience different wear and tear compared to those in consumer products.
-
Factors Affecting PVD Coating Lifespan:
- Substrate Material: The type of material being coated plays a significant role in determining the lifespan of the PVD coating. Different substrates bond differently with the coating, affecting durability.
- Coating Thickness: Thicker coatings generally provide better protection and longer lifespans, but they must be balanced with the need to retain the product's original shape.
- Bond Strength: The strength of the bond between the coating and the substrate is crucial. A stronger bond ensures better adhesion and resistance to peeling or flaking.
- Environmental Exposure: Exposure to heat, abrasion, and aggressive chemicals can impact the lifespan of PVD coatings. Proper maintenance and avoiding harsh conditions can extend the coating's life.
-
Limitations and Potential Damage:
- While PVD coatings are wear and weather-resistant, they are not indestructible. Aggressive attacks, such as harsh chemicals or physical abrasion, can damage the color and finish. In some cases, this damage may not be repairable.
- The thinness of PVD coatings, while beneficial for retaining the product's shape, can also make them more susceptible to damage if not properly maintained.
-
Advantages Over Traditional Coatings:
- PVD coatings eliminate the need for additional top coatings or support due to their inherent durability and resistance properties.
- The vacuum environment during application prevents oxidation and degradation caused by oxygen and moisture, further enhancing the coating's longevity.
In summary, PVD plating is a highly durable and long-lasting solution for various applications, with a lifespan that can extend up to 10 years in favorable conditions. However, its longevity depends on factors such as substrate material, coating thickness, bond strength, and environmental exposure. Proper application and maintenance are essential to maximize the lifespan of PVD coatings.
Summary Table:
Key Factor | Impact on PVD Coating Lifespan |
---|---|
Substrate Material | Different materials bond uniquely, affecting durability and adhesion. |
Coating Thickness | Thicker coatings offer better protection but must balance with the product's original shape. |
Bond Strength | Stronger bonds enhance resistance to peeling, flaking, and wear. |
Environmental Exposure | Heat, abrasion, and chemicals can reduce lifespan; proper maintenance extends durability. |
Maximize the lifespan of your PVD coatings—contact our experts today for tailored solutions!