Spark plasma sintering (SPS), also known as field-assisted sintering technique (FAST), is a rapid sintering process that significantly reduces the time required compared to conventional methods. The process typically takes only a few minutes to complete, depending on the material and desired density. This is achieved through the application of pulsed direct current (DC) that generates high temperatures locally, facilitating rapid heating and cooling rates, as well as short holding times. The entire process, including heating, holding, and cooling, can be completed in a fraction of the time required for traditional sintering methods, making it highly efficient for producing dense materials.
Key Points Explained:
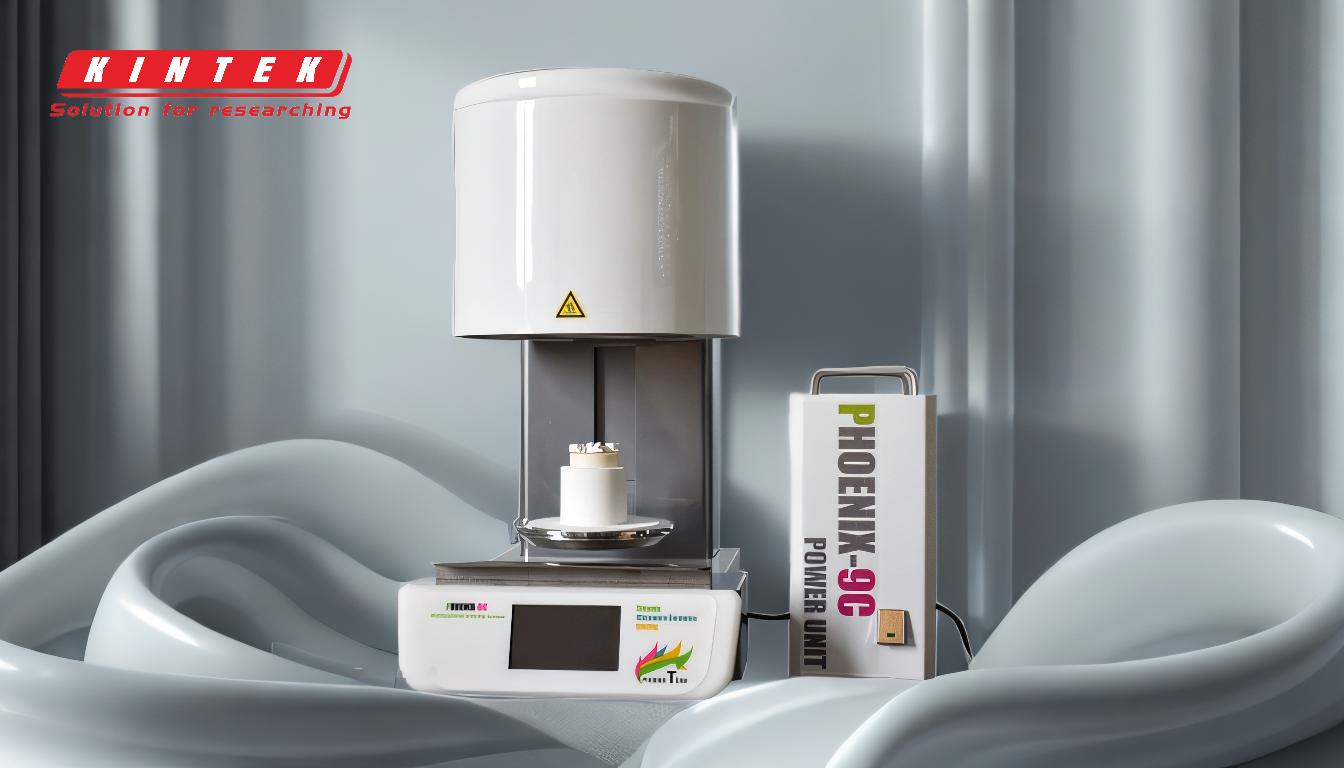
-
Rapid Heating and Cooling Rates:
- SPS uses pulsed DC to generate high temperatures locally, allowing for extremely fast heating rates. This rapid heating is facilitated by the direct application of current through the material and the die, which acts as a heat source.
- The cooling rate is also rapid, as the process does not rely on external heating elements that require time to cool down. This rapid cycling of heating and cooling contributes to the overall short duration of the SPS process.
-
Short Holding Times:
- Unlike conventional sintering, which may require hours of holding at high temperatures, SPS typically involves holding times of only a few minutes. This is because the high local temperatures and plasma generation at particle interfaces accelerate the densification process.
- The short holding time is sufficient to achieve high densities (often over 99%) due to the enhanced sintering activity caused by mechanisms such as Joule heating, plasma generation, and electromigration.
-
Lower Sintering Temperatures:
- SPS allows for densification at temperatures several hundred degrees lower than those required in conventional sintering. This is due to the combined effects of pressure and the electric field, which enhance the sintering activity at lower temperatures.
- The lower temperatures reduce the time needed for the material to reach the required sintering conditions, further contributing to the overall efficiency of the process.
-
Process Duration:
- The entire SPS process, including heating, holding, and cooling, can be completed in just a few minutes. This is a significant reduction compared to traditional sintering methods, which may take several hours or even days.
- The exact duration of the SPS process can vary depending on the material being sintered and the desired density, but it is generally much shorter than conventional sintering.
-
Mechanisms of SPS:
- Joule Heating: The pulsed DC current generates heat directly within the material, leading to rapid temperature increases.
- Plasma Generation: The high-energy pulses create plasma at the particle interfaces, which helps to clean the surfaces and promote bonding.
- Electromigration: The electric field enhances the movement of atoms at the particle boundaries, facilitating diffusion and densification.
-
Applications and Efficiency:
- SPS is particularly useful for materials that require high densities and fine microstructures, such as ceramics and metallic powders. The rapid processing time makes it an attractive option for industrial applications where time and energy efficiency are critical.
- The ability to achieve high densities at lower temperatures and in shorter times also reduces the risk of grain growth and other undesirable microstructural changes that can occur during prolonged sintering.
In summary, spark plasma sintering is a highly efficient process that typically takes only a few minutes to complete, thanks to its rapid heating and cooling rates, short holding times, and lower sintering temperatures. The mechanisms of Joule heating, plasma generation, and electromigration work together to achieve high densities in a fraction of the time required by conventional sintering methods.
Summary Table:
Aspect | Details |
---|---|
Process Duration | Typically a few minutes, significantly shorter than conventional methods. |
Heating/Cooling Rates | Rapid due to pulsed DC and localized heat generation. |
Holding Times | Short (minutes) for high-density results. |
Sintering Temperatures | Lower than conventional methods, enhancing efficiency. |
Key Mechanisms | Joule heating, plasma generation, and electromigration. |
Applications | Ideal for ceramics, metallic powders, and fine microstructures. |
Ready to enhance your material processing with SPS? Contact our experts today to learn more!