The calcination process duration varies depending on factors such as the material being processed, the desired chemical reaction, the equipment used, and the specific temperature requirements. Generally, calcination can take anywhere from a few minutes to several hours. For example, in the production of lime from limestone, the process typically takes 1-2 hours in a rotary kiln at temperatures around 900-1000°C. However, other materials or reactions may require different durations. The process is carefully controlled to ensure complete thermal decomposition or removal of volatile substances.
Key Points Explained:
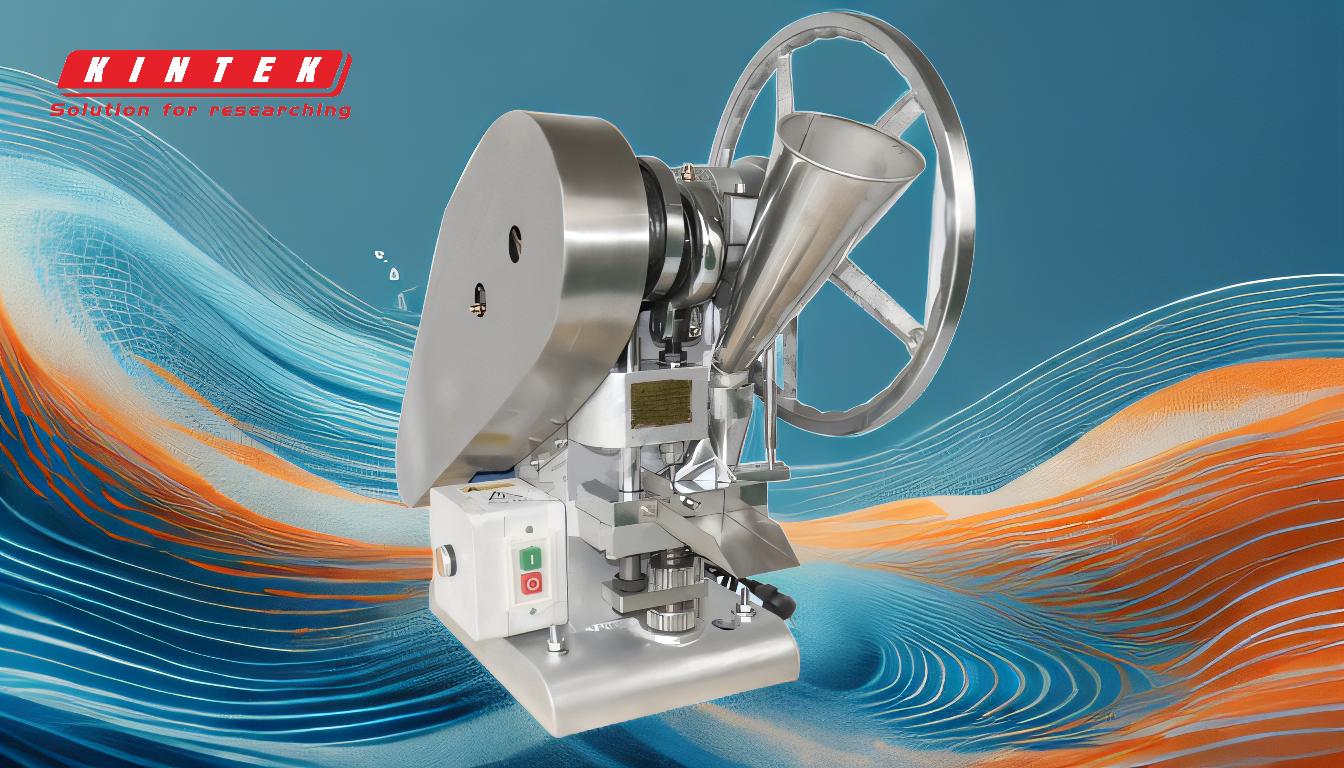
-
Definition and Purpose of Calcination:
- Calcination is a heat treatment process used to induce thermal decomposition, remove volatile impurities, or achieve chemical dissociation in materials.
- It involves heating materials below their melting point, often in the absence or limited supply of air or oxygen.
- Common applications include the production of lime from limestone and the extraction of metals from ores.
-
Factors Influencing Calcination Duration:
- Material Properties: Different materials require varying temperatures and durations for complete decomposition. For example, limestone calcination typically occurs at 900-1000°C.
- Reaction Requirements: The specific chemical reaction being targeted (e.g., dissociation of calcium carbonate) influences the time needed.
- Equipment Used: Rotary kilns, for instance, are efficient for calcination and can process materials like limestone in 1-2 hours.
- Particle Size: Smaller particles (e.g., 60 mm or less) calcine more uniformly and quickly in rotary kilns.
-
Examples of Calcination Processes:
- Lime Production: Heating limestone (CaCO3) to 900-1000°C for 1-2 hours produces lime (CaO) and carbon dioxide (CO2).
- Metal Ore Processing: Calcination removes volatile impurities from metal ores, often requiring precise temperature control and duration.
- Moisture Removal: Materials like borax are calcined to remove bound moisture, with the duration depending on the material's properties.
-
Equipment and Process Optimization:
- Rotary kilns are commonly used for calcination due to their ability to handle large volumes and provide uniform heating.
- The process is optimized to balance temperature, duration, and material properties, ensuring efficient and complete reactions.
-
General Timeframe:
- Calcination typically ranges from a few minutes to several hours, depending on the material and reaction.
- Industrial processes often aim for shorter durations to improve efficiency, while ensuring the desired chemical changes are achieved.
In summary, the calcination process duration is highly variable and depends on the specific application, material, and equipment. Understanding these factors is crucial for optimizing the process and achieving the desired results.
Summary Table:
Factor | Impact on Duration |
---|---|
Material Properties | Different materials require varying temperatures and durations for decomposition. |
Reaction Requirements | Specific chemical reactions influence the time needed for complete calcination. |
Equipment Used | Rotary kilns can process materials like limestone in 1-2 hours. |
Particle Size | Smaller particles calcine more uniformly and quickly in rotary kilns. |
Need help optimizing your calcination process? Contact our experts today for tailored solutions!