The time it takes for a furnace to raise the temperature to its maximum level depends on several factors, including the furnace type, size, power capacity, and construction materials. For instance, a muffle furnace can take anywhere from 20 minutes to several hours to reach its maximum temperature, depending on its size and insulation. Smaller laboratory-scale furnaces with low thermal mass insulation heat up faster, while larger furnaces with dense refractory materials take longer. Additionally, the specific model of the furnace, the material being processed, and the desired processing conditions also play a role in determining the heating time. Understanding these factors is crucial for optimizing furnace performance and ensuring efficient operations.
Key Points Explained:
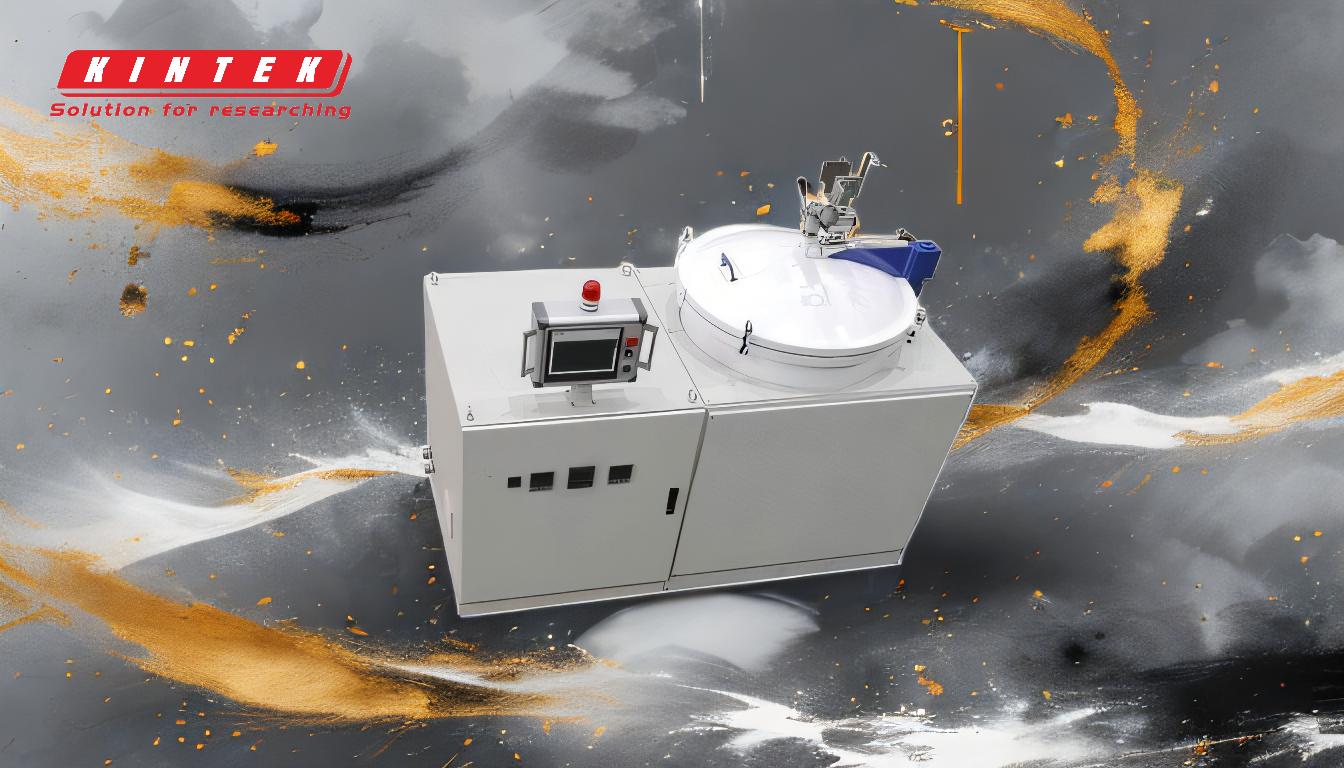
-
Furnace Type and Size:
- The type and size of the furnace significantly impact the time required to reach maximum temperature. Smaller furnaces, such as laboratory-scale muffle furnaces, heat up faster due to their lower thermal mass. Larger furnaces, especially those used in industrial applications, take longer because they have more material to heat and often use dense refractory materials for insulation.
-
Power Capacity:
- The maximum power available to the furnace directly affects its heating rate. Furnaces with higher power capacities can generate more heat in a shorter time, reducing the overall time required to reach the desired temperature. This is particularly important in industrial settings where time efficiency is critical.
-
Construction Materials:
- The materials used in the construction of the furnace, such as insulation and refractory materials, influence its heating time. Furnaces with low thermal mass insulation, like those used in laboratory settings, heat up faster. In contrast, furnaces with dense refractory materials, which are common in industrial applications, take longer to heat due to their higher thermal mass.
-
Material Being Processed:
- The properties of the material being processed also play a role in determining the heating time. Different materials have varying thermal conductivities and specific heat capacities, which affect how quickly they absorb heat. For example, metals generally heat up faster than ceramics due to their higher thermal conductivity.
-
Desired Processing Conditions:
- The specific processing conditions, such as the target temperature and the rate of temperature increase, influence the time required to reach the maximum temperature. Some processes require gradual heating to prevent thermal shock, while others may allow for rapid heating.
-
Furnace Model and Design:
- The specific model and design of the furnace can also impact heating time. Different models may have varying efficiencies, heating element configurations, and control systems, all of which affect how quickly the furnace can reach its maximum temperature.
-
Environmental and Operational Factors:
- External factors, such as ambient temperature and the condition of the furnace (e.g., soiling or deposits from previous uses), can also influence heating time. Regular maintenance and cleaning can help maintain optimal performance and reduce heating time.
Understanding these factors allows users to select the appropriate furnace for their needs and optimize its operation to achieve the desired heating time. Whether in a laboratory or industrial setting, considering these variables ensures efficient and effective furnace performance.
Summary Table:
Factor | Impact on Heating Time |
---|---|
Furnace Type and Size | Smaller furnaces heat up faster; larger furnaces take longer due to higher thermal mass. |
Power Capacity | Higher power reduces heating time, especially in industrial settings. |
Construction Materials | Low thermal mass insulation heats faster; dense refractory materials take longer. |
Material Being Processed | Metals heat faster than ceramics due to higher thermal conductivity. |
Desired Processing Conditions | Gradual heating prevents thermal shock; rapid heating may be allowed. |
Furnace Model and Design | Efficiency, heating elements, and control systems vary by model. |
Environmental Factors | Ambient temperature and furnace condition (e.g., cleanliness) affect heating time. |
Need help optimizing your furnace's heating time? Contact our experts today for tailored solutions!