PVD (Physical Vapor Deposition) coatings are thin film coatings that typically range in thickness from 0.25 microns to 5 microns. This range ensures that the coatings enhance properties like hardness, smoothness, and corrosion resistance without significantly altering the dimensions or appearance of the engineered parts. The specific thickness can vary depending on the application, with decorative coatings often being thinner (around 0.30 microns) and functional coatings being thicker (up to 5 microns). The thinness of PVD coatings makes them ideal for applications where precision and surface enhancement are critical.
Key Points Explained:
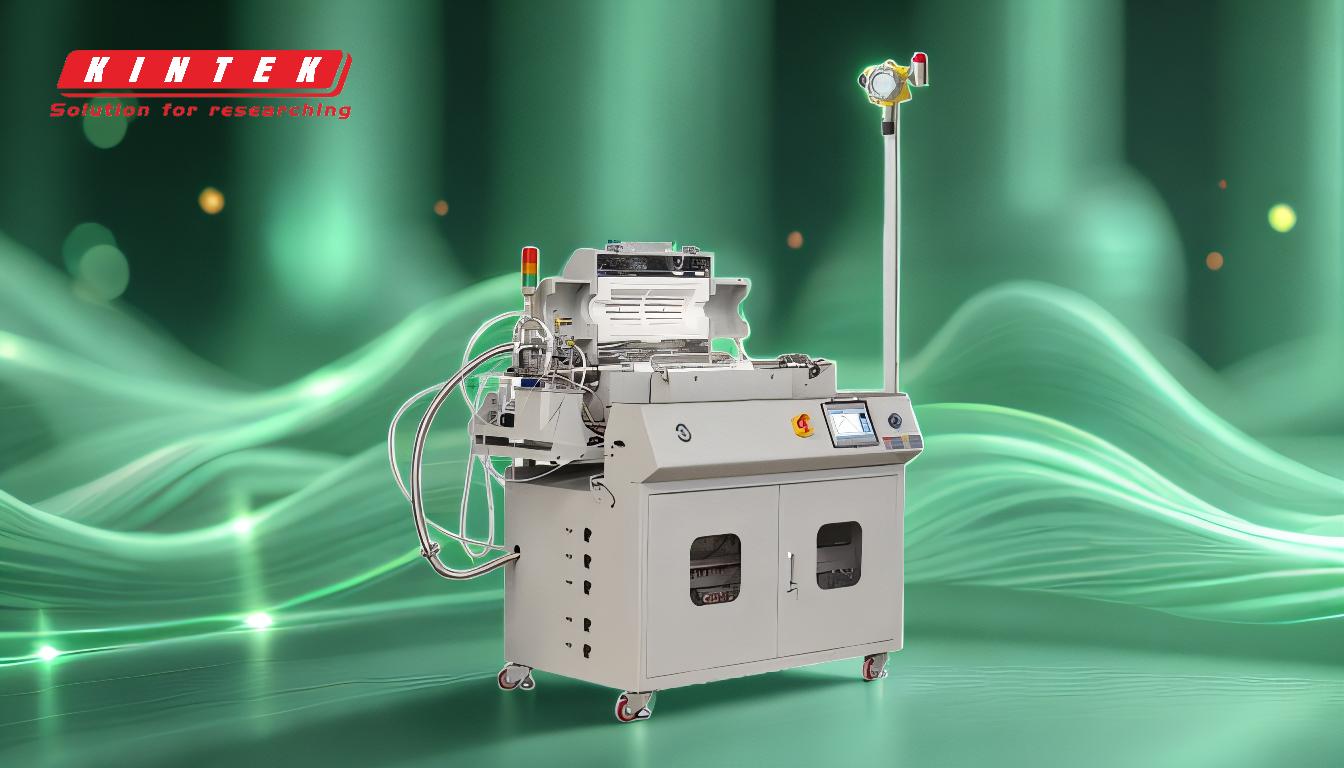
-
Typical Thickness Range of PVD Coatings:
- PVD coatings generally range from 0.25 microns to 5 microns in thickness.
- This range is consistent across multiple references, indicating that PVD coatings are designed to be extremely thin to maintain the integrity and specifications of the underlying material.
-
Application-Specific Thickness:
- Decorative Applications: For decorative purposes, such as on stainless steel sheets, PVD coatings can be as thin as 0.30 microns. This ensures a visually appealing finish without adding significant bulk.
- Functional Applications: For functional uses, such as enhancing hardness or corrosion resistance, the thickness typically ranges from 2 to 5 microns. This increased thickness provides the necessary durability and protection for demanding applications.
-
Benefits of Thin PVD Coatings:
- Precision: The thinness of PVD coatings ensures that the dimensions of engineered parts remain unchanged, which is critical for precision components.
- Surface Enhancement: Despite their thinness, PVD coatings significantly improve surface properties such as hardness, smoothness, and resistance to wear and corrosion.
- Aesthetic Preservation: In decorative applications, the thin coating enhances appearance without altering the material's original look or feel.
-
Comparison with Other Coating Technologies:
- PVD vs. CVD: PVD coatings are generally thinner than CVD (Chemical Vapor Deposition) coatings, which typically range from 5 to 10 microns. This makes PVD coatings more suitable for applications where minimal dimensional change is required.
-
Real-World Context for Thickness:
- Human Hair: For perspective, a human hair is approximately 80 microns in diameter, making PVD coatings significantly thinner.
- Red Blood Cells: Red blood cells are around 8 microns in diameter, further illustrating how thin PVD coatings are in comparison to biological structures.
-
Factors Influencing Coating Thickness:
- Lubrication: The presence of lubrication can affect the optimal thickness of the coating.
- Surface Finish: The initial surface finish of the material can influence the required coating thickness.
- Type of Motion: The nature of the application (e.g., sliding, rotating) can determine the necessary thickness for durability and performance.
In summary, PVD coatings are characterized by their thinness, typically ranging from 0.25 to 5 microns, depending on the application. This thin film provides significant benefits in terms of precision, surface enhancement, and aesthetic preservation, making PVD coatings a versatile solution for both decorative and functional applications.
Summary Table:
Aspect | Details |
---|---|
Typical Thickness Range | 0.25 to 5 microns |
Decorative Applications | ~0.30 microns for aesthetic finishes |
Functional Applications | 2 to 5 microns for hardness and corrosion resistance |
Key Benefits | Precision, surface enhancement, and aesthetic preservation |
Comparison (PVD vs. CVD) | PVD is thinner (0.25-5 microns) vs. CVD (5-10 microns) |
Real-World Perspective | Thinner than a human hair (80 microns) and red blood cells (8 microns) |
Explore how PVD coatings can enhance your projects—contact our experts today!