The power consumption of an induction furnace depends on the type of material being melted, the furnace design, and the desired production capacity. For steel, the standard power consumption is approximately 625 kWh per tonne. For example, if the desired production is 520 kg/hour, the required power supply capacity would be 325 kW. Coreless induction furnaces typically consume between 500 and 800 kWh per tonne, depending on the type and grade of casting. Efficient operation requires a three-phase electric current and specialized transformers to convert alternating current into direct current at the appropriate frequency. The input voltage for aluminum melting furnaces is typically three-phase 380V.
Key Points Explained:
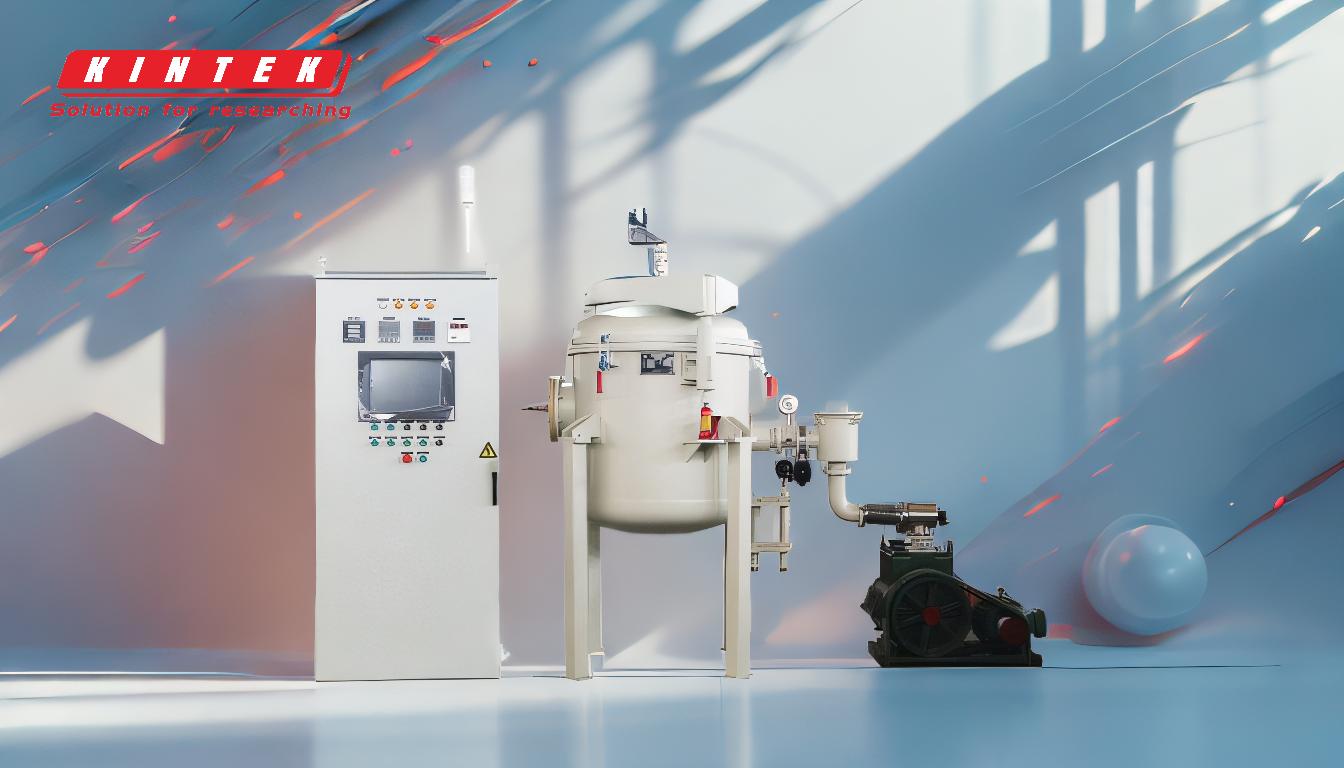
-
Power Consumption per Tonne:
- The standard power consumption for a steel induction furnace is 625 kWh/ton.
- For coreless induction furnaces, the specific energy consumption ranges from 500 to 800 kWh/ton, depending on the type and grade of casting.
-
Calculating Power Supply Capacity:
- The required power supply capacity depends on the desired production rate.
- Example calculation:
- Desired yearly production: 2000 tons.
- Daily production: 8.33 tons/day (assuming 240 working days).
- Hourly production: 520 kg/hour.
- Using the standard power consumption of 625 kWh/ton, the required power is: [ (520 , \text{kg/hour}) \times \left(\frac{625 , \text{kWh}}{1000 , \text{kg}}\right) = 325 , \text{kW}. ]
- Therefore, the required power supply capacity is 325 kW.
-
Input Voltage and Electrical Requirements:
- Induction furnaces typically operate on a three-phase electric current.
- For aluminum melting furnaces, the input voltage is usually three-phase 380V (three-phase five-wire power supply).
- Special transformers are required to convert alternating current (AC) into direct current (DC) and provide the appropriate frequency for efficient operation.
-
Safety Considerations:
- It is essential to avoid touching input and output connectors when the machine is powered on to prevent safety accidents.
-
Factors Affecting Power Consumption:
- Material Type: Different materials (e.g., steel, aluminum, iron) have varying energy requirements for melting.
- Furnace Design: Coreless induction furnaces may have different energy efficiencies compared to other designs.
- Production Capacity: Higher production rates require greater power supply capacities.
By understanding these key points, equipment and consumable purchasers can make informed decisions about the power requirements and operational efficiency of induction furnaces.
Summary Table:
Factor | Details |
---|---|
Power Consumption | Steel: 625 kWh/ton; Coreless: 500–800 kWh/ton (varies by casting type/grade) |
Power Supply Capacity | Example: 520 kg/hour requires 325 kW (based on 625 kWh/ton for steel) |
Input Voltage | Aluminum melting furnaces: Three-phase 380V |
Electrical Requirements | Three-phase current; transformers for AC to DC conversion |
Safety | Avoid touching connectors when powered on |
Need help calculating your induction furnace power requirements? Contact our experts today for personalized guidance!