The heat resistance of a crucible depends on the material it is made from, with common crucibles capable of withstanding temperatures up to 2000°C. However, high-purity graphite crucibles can endure even higher temperatures, up to 3000°C (5472°F), making them suitable for melting metals like aluminum, copper, and brass without risk of contamination or heat stress damage. Additionally, when used with air heaters, graphite crucibles can withstand temperatures up to 3200°F. Crucibles must also have high resistance to chemical attack, especially when used with corrosive metal treatments, ensuring durability and stability during high-temperature processes.
Key Points Explained:
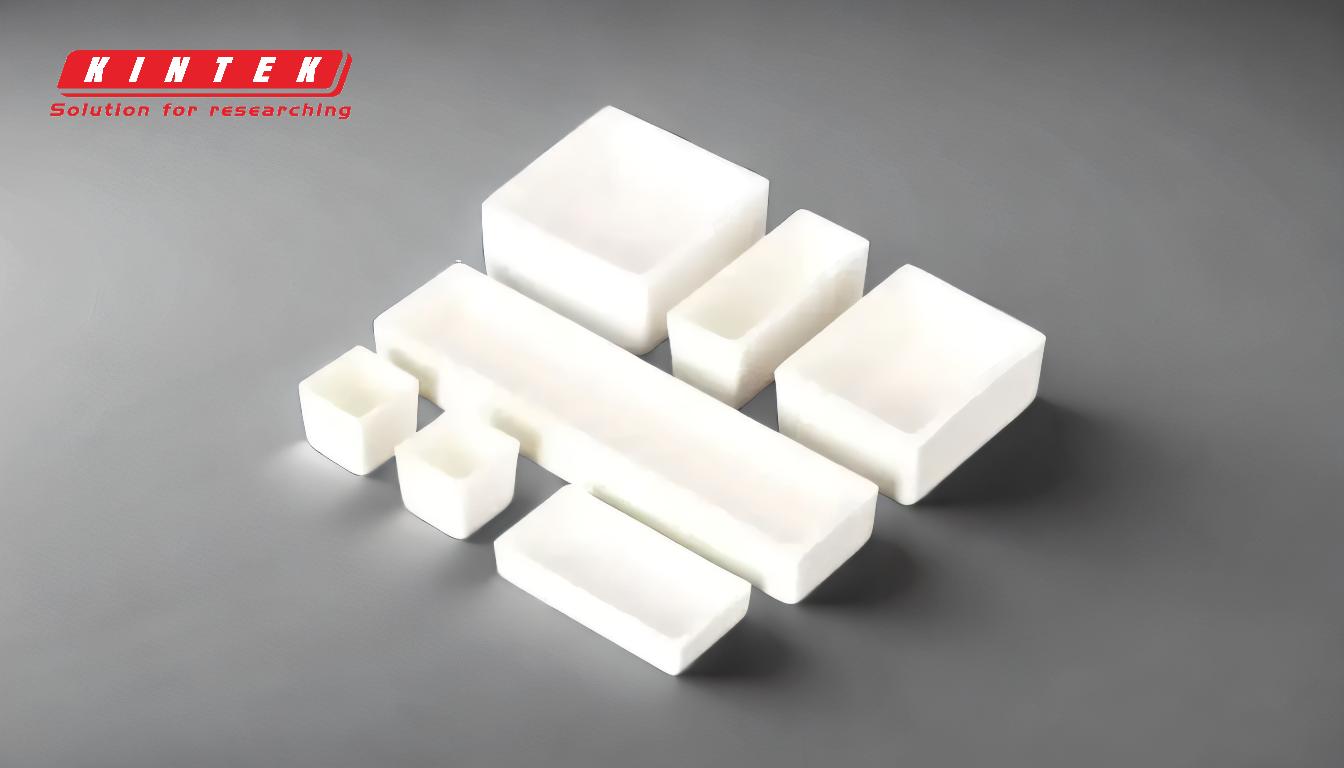
-
General Heat Resistance of Crucibles:
- Most crucibles can withstand temperatures up to 2000°C.
- They are made from materials designed to endure extreme heat and chemical reactions, ensuring stability during high-temperature processes.
-
High-Purity Graphite Crucibles:
- These crucibles can withstand temperatures up to 3000°C (5472°F).
- They are ideal for melting metals like aluminum, copper, and brass due to their ability to resist contamination and heat stress damage.
-
Graphite Crucibles with Air Heaters:
- When used with air heaters, graphite crucibles can withstand temperatures up to 3200°F.
- This makes them suitable for applications requiring even higher heat resistance.
-
Chemical Resistance and Durability:
- Crucibles used with corrosive metal treatments (e.g., fluxes and additives in aluminum melting) require high resistance to chemical attack.
- A dense material structure and durable protective glaze are essential to ensure the crucible can withstand corrosive environments.
-
Key Properties of Crucibles:
- A crucible must have:
- Extremely high-temperature resistance.
- Outstanding chemical and physical stability.
- A melting point higher than the materials it contains.
- Chemical compatibility with the melts to prevent reactions that could cause deterioration or contamination.
- A crucible must have:
By understanding these key points, purchasers can select the appropriate crucible material and type based on the specific temperature and chemical requirements of their application.
Summary Table:
Crucible Type | Max Temperature | Key Applications |
---|---|---|
Standard Crucibles | 2000°C | General high-temperature processes |
High-Purity Graphite | 3000°C (5472°F) | Melting aluminum, copper, brass |
Graphite with Air Heaters | 3200°F | Extreme heat applications |
Key Properties | ||
High-temperature resistance | Essential for stability in extreme heat | |
Chemical resistance | Prevents contamination and deterioration | |
Durable material structure | Ensures longevity in corrosive environments |
Need a crucible that meets your high-temperature and chemical resistance needs? Contact us today for expert guidance!