Electron beam evaporation is a physical vapor deposition (PVD) technique used to create thin films with precise control over thickness and composition. The process involves heating a target material using a focused electron beam in a high-vacuum environment, causing it to evaporate or sublimate. The vaporized material then deposits onto a substrate, forming a thin film. This method is widely used in industries requiring high-purity coatings, such as optics, electronics, and semiconductors. The process is characterized by its ability to handle high-melting-point materials and produce films with excellent reflectivity and uniformity.
Key Points Explained:
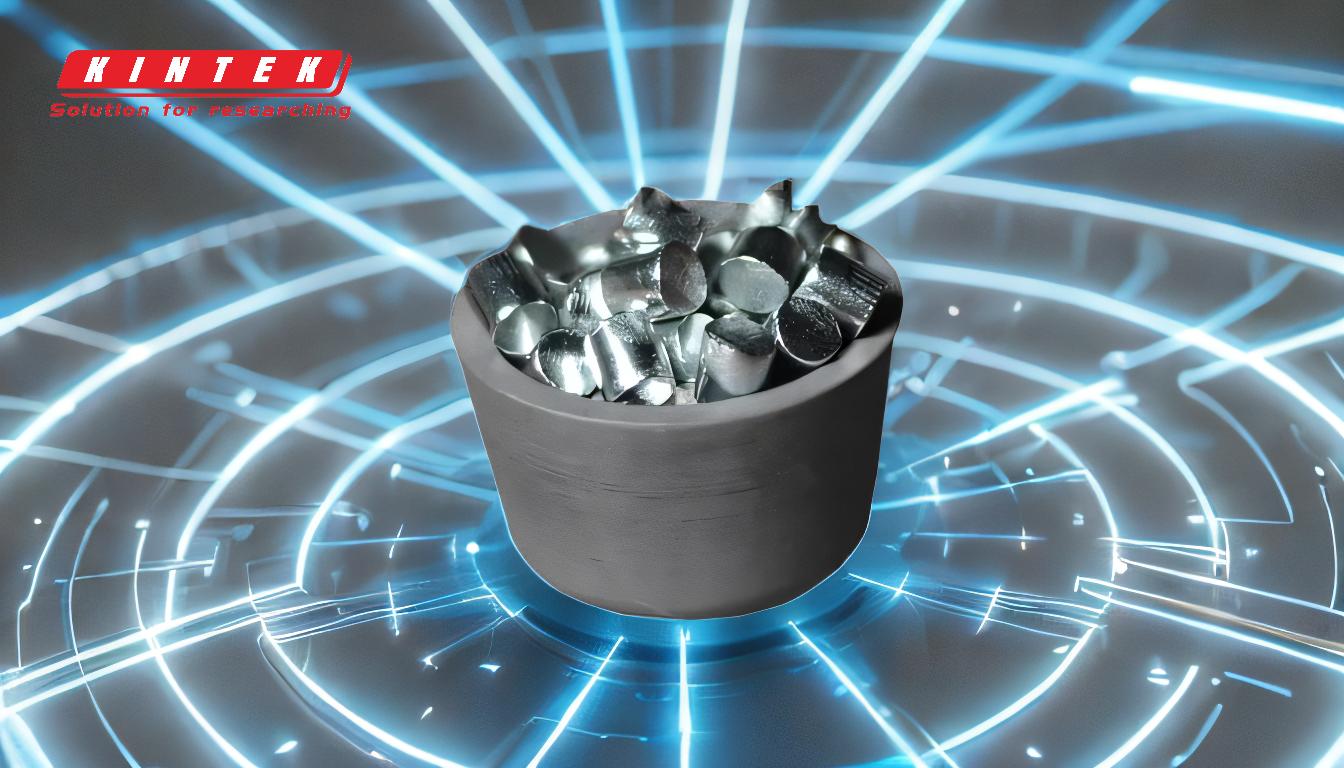
-
Electron Beam Generation and Focusing:
- A tungsten filament is heated by passing an electric current through it, causing thermionic emission of electrons.
- These electrons are accelerated by a high-voltage electric field (typically 5–10 kV) toward the target material.
- A magnetic field is used to focus the electrons into a narrow, high-energy beam, ensuring precise targeting of the material in the crucible.
-
Material Heating and Evaporation:
- The focused electron beam strikes the target material in a water-cooled crucible, transferring kinetic energy into thermal energy.
- This intense heating causes the material to reach its vaporization temperature, either evaporating (for metals) or sublimating (for certain compounds).
- The high vacuum environment minimizes contamination and ensures the vaporized material travels unimpeded to the substrate.
-
Deposition on Substrate:
- The vaporized material disperses in the vacuum chamber and condenses onto the cooler substrate surface.
- The substrate is typically positioned above the crucible to ensure uniform deposition.
- The resulting thin film adheres strongly to the substrate, forming a coating with excellent reflectivity, uniformity, and purity.
-
Role of Reactive Gases (Optional):
- In some cases, reactive gases like oxygen or nitrogen are introduced into the vacuum chamber.
- These gases react with the vaporized material to form non-metallic films, such as oxides or nitrides, expanding the range of materials that can be deposited.
-
Advantages of Electron Beam Evaporation:
- High Purity: The high vacuum environment and localized heating minimize contamination.
- Versatility: Capable of depositing a wide range of materials, including high-melting-point metals and ceramics.
- Precision: Allows for precise control over film thickness and composition.
- Uniformity: Produces films with excellent reflectivity and uniformity, making it ideal for optical and electronic applications.
-
Applications:
- Optics: Used to create reflective coatings for mirrors, lenses, and other optical components.
- Electronics: Deposits thin films for semiconductors, sensors, and conductive layers.
- Decorative Coatings: Provides durable and aesthetically pleasing finishes for consumer products.
- Research and Development: Enables the creation of advanced materials with tailored properties.
By following these steps, electron beam evaporation achieves high-quality thin films with exceptional control over material properties, making it a cornerstone of modern thin-film deposition technologies.
Summary Table:
Key Aspect | Description |
---|---|
Electron Beam Generation | Tungsten filament emits electrons, focused by a magnetic field for precision. |
Material Heating | Electron beam heats target material, causing evaporation or sublimation. |
Deposition | Vaporized material condenses on a substrate, forming a uniform thin film. |
Reactive Gases (Optional) | Introduced to form non-metallic films like oxides or nitrides. |
Advantages | High purity, versatility, precision, and uniformity in thin-film deposition. |
Applications | Optics, electronics, decorative coatings, and advanced material research. |
Need high-quality thin films for your applications? Contact us today to learn how electron beam evaporation can meet your needs!