Hydraulic presses are among the most powerful machines used in industrial and manufacturing settings, capable of exerting immense force to shape, mold, or compress materials. Their strength is determined by factors such as hydraulic pressure, piston size, and the design of the press. Hydraulic presses are widely used in applications like metal forming, forging, laminating, and powder compacting due to their ability to deliver consistent and high-pressure force. The strength of a hydraulic press can range from a few tons to thousands of tons, depending on its size and purpose. For instance, smaller presses are used in workshops, while massive industrial presses are employed in heavy-duty manufacturing. The versatility and power of hydraulic presses make them indispensable in industries requiring precision and force.
Key Points Explained:
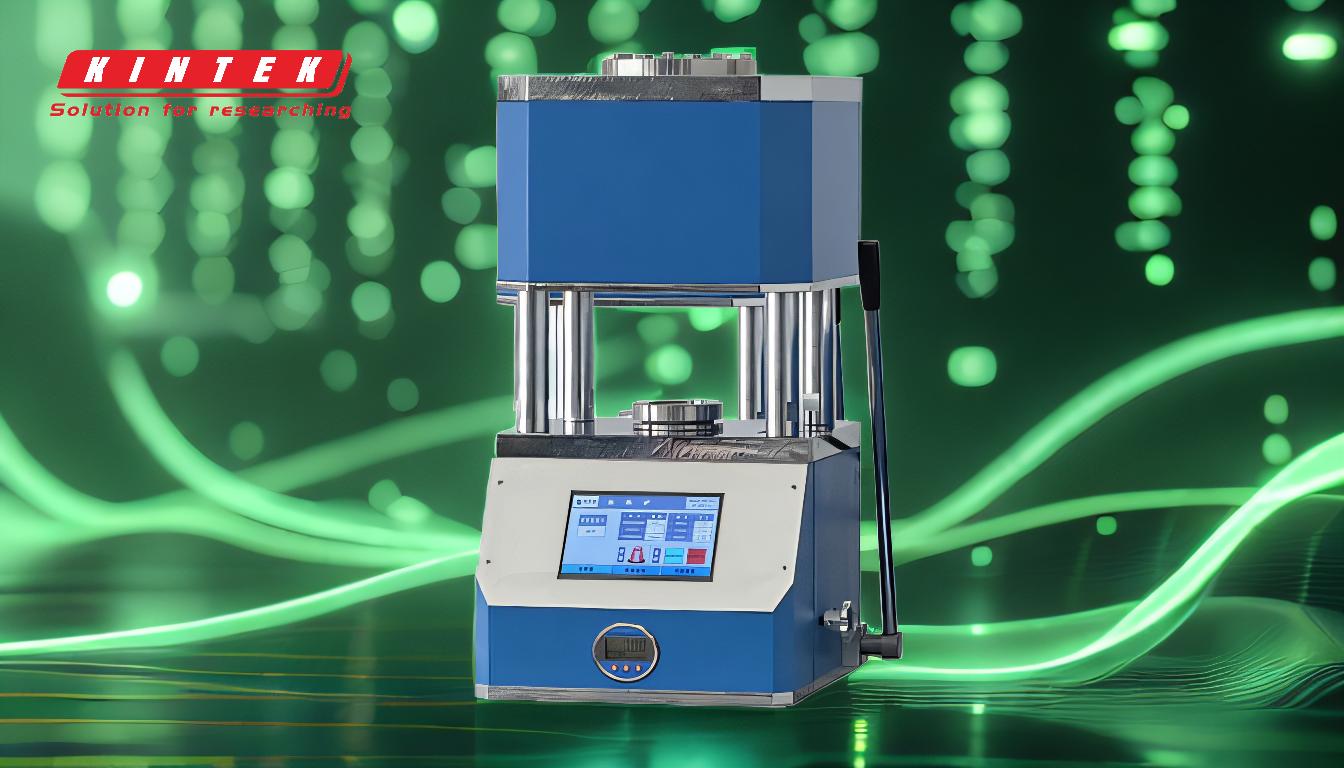
-
How Hydraulic Presses Generate Force
- Hydraulic presses operate on Pascal's principle, which states that pressure applied to a confined fluid is transmitted equally in all directions. This principle allows hydraulic presses to amplify force using a small input force applied to a small piston, which then generates a much larger force on a larger piston.
- The force output is calculated using the formula:
[ \text{Force} = \text{Pressure} \times \text{Area} ]
This means that by increasing the pressure or the area of the piston, the press can generate significantly higher forces.
-
Range of Force in Hydraulic Presses
- Hydraulic presses are available in a wide range of force capacities, from small bench-top models capable of exerting a few tons of force to massive industrial presses that can deliver thousands of tons of force.
- For example, a typical workshop hydraulic press might have a capacity of 10 to 100 tons, while industrial presses used in forging or automotive manufacturing can exceed 10,000 tons.
- The hydraulic hot press machine is a specialized type of hydraulic press that combines high pressure with heat, making it ideal for applications like laminating, molding, and composite material production.
-
Applications of Hydraulic Presses
- Metal Forming and Forging: Hydraulic presses are widely used in shaping metal parts through processes like stamping, deep drawing, and extrusion. Their ability to deliver consistent force ensures precision in forming complex shapes.
- Powder Compacting: In industries like pharmaceuticals and ceramics, hydraulic presses are used to compress powders into solid forms. The high pressure ensures uniform density and strength in the final product.
- Laminating and Molding: Hydraulic presses, especially the hydraulic hot press machine, are used in laminating materials like wood, plastics, and composites. The combination of heat and pressure ensures strong bonds between layers.
- Assembly and Disassembly: Hydraulic presses are also used for tasks like pressing bearings into housings or removing stubborn components, thanks to their controlled and powerful force.
-
Factors Affecting the Strength of Hydraulic Presses
- Hydraulic System Design: The design of the hydraulic system, including the size of the cylinders and the quality of the hydraulic fluid, plays a critical role in determining the press's strength.
- Pressure Rating: The maximum pressure the hydraulic system can sustain directly affects the force output. Higher pressure ratings allow for greater force generation.
- Piston Size: Larger pistons can generate more force due to their greater surface area.
- Frame Construction: The frame of the press must be robust enough to withstand the forces generated without deformation or failure.
-
Advantages of Hydraulic Presses
- High Force Output: Hydraulic presses can generate significantly higher forces compared to mechanical or pneumatic presses.
- Precision and Control: Modern hydraulic presses are equipped with advanced controls that allow for precise adjustment of force, speed, and stroke length.
- Versatility: Hydraulic presses can be adapted for a wide range of applications by changing dies, molds, or tooling.
- Safety: Hydraulic systems are inherently safer than mechanical systems, as they can be designed with overload protection and fail-safes.
-
Limitations of Hydraulic Presses
- Speed: Hydraulic presses are generally slower than mechanical presses due to the time required to build and release hydraulic pressure.
- Maintenance: Hydraulic systems require regular maintenance to prevent leaks and ensure optimal performance.
- Energy Consumption: Hydraulic presses can be less energy-efficient compared to other types of presses, especially in continuous operation.
In conclusion, hydraulic presses are incredibly strong and versatile machines, capable of generating forces ranging from a few tons to thousands of tons. Their strength, precision, and adaptability make them essential in industries like manufacturing, automotive, and construction. The hydraulic hot press machine is a specialized variant that combines heat and pressure for applications requiring enhanced material bonding or shaping. Understanding the factors that influence their strength and performance is crucial for selecting the right press for specific tasks.
Summary Table:
Aspect | Details |
---|---|
Force Range | Few tons to thousands of tons, depending on size and purpose. |
Key Applications | Metal forming, forging, powder compacting, laminating, and assembly tasks. |
Factors Affecting Force | Hydraulic system design, pressure rating, piston size, and frame strength. |
Advantages | High force output, precision, versatility, and safety features. |
Limitations | Slower speed, regular maintenance, and higher energy consumption. |
Need a hydraulic press for your industrial needs? Contact us today to find the perfect solution!