Hydraulic presses are incredibly strong machines that utilize hydraulic fluid pressure to generate immense force, making them essential in various industrial applications. Their strength is primarily determined by the system's hydraulic pressure, piston size, and mechanical design. Hydraulic presses can exert forces ranging from a few tons to several thousand tons, depending on their configuration and purpose. They are widely used in manufacturing, metalworking, and material testing due to their ability to apply consistent and controlled force. The strength of a hydraulic press is a result of Pascal's Law, which states that pressure applied to a confined fluid is transmitted equally in all directions, allowing for the amplification of force.
Key Points Explained:
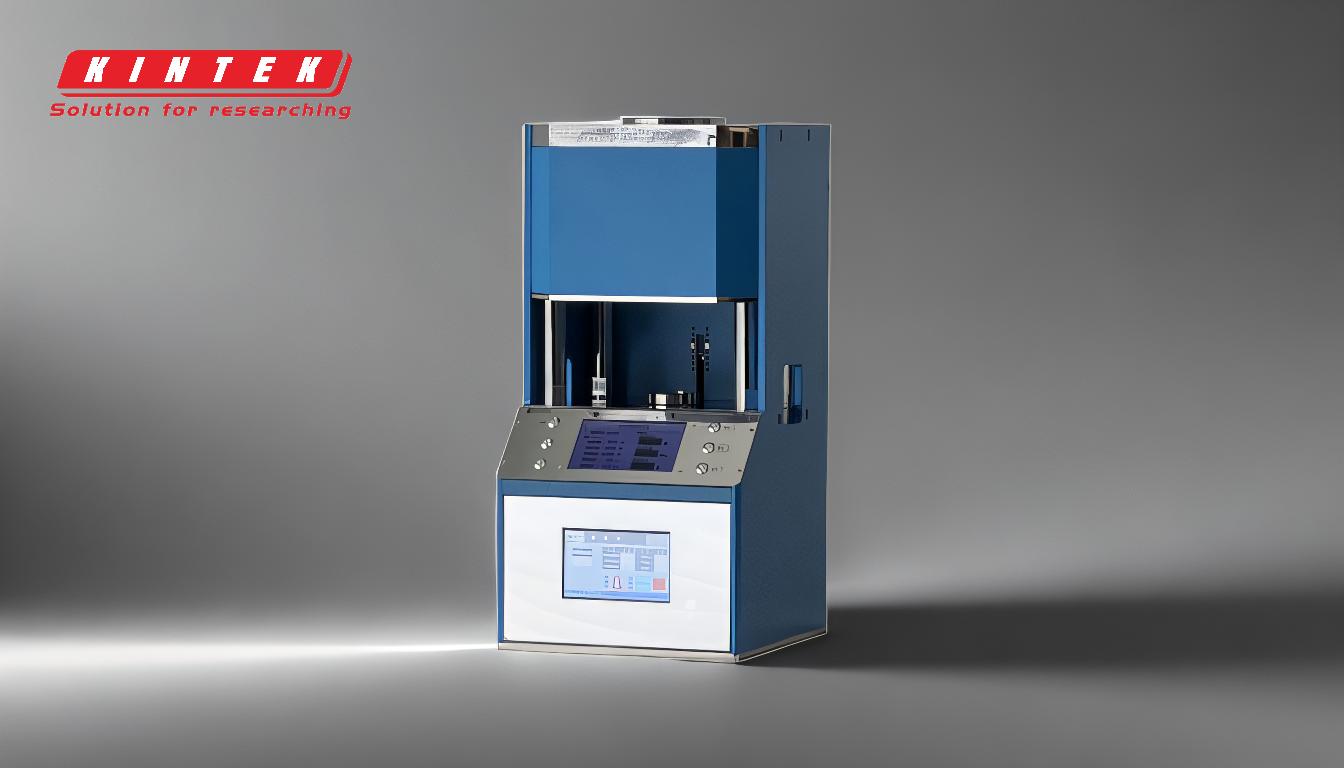
-
Principle of Operation: Pascal's Law
- Hydraulic presses operate based on Pascal's Law, which explains how pressure applied to a confined fluid is distributed equally in all directions. This principle allows a small force applied to a small piston to generate a much larger force on a larger piston, enabling the press to amplify force significantly.
- The formula ( F = P \times A ) (Force = Pressure × Area) is central to understanding how hydraulic presses achieve their strength. By increasing the area of the piston, the force output can be dramatically increased.
-
Force Capacity
- Hydraulic presses are capable of generating forces ranging from a few tons to over 10,000 tons. For example, smaller bench-top hydraulic presses might exert forces of 10-20 tons, while industrial-grade presses, such as those used in forging or automotive manufacturing, can exceed 10,000 tons.
- The force capacity depends on the hydraulic system's pressure rating and the size of the pistons. Higher pressure and larger piston areas result in greater force output.
-
Applications of High Force
- Hydraulic presses are used in industries requiring high-force applications, such as metal forming, stamping, forging, and compression molding. For instance, in the automotive industry, hydraulic presses are used to shape car body panels and components.
- They are also employed in material testing, where precise and controlled force application is necessary to evaluate material properties like tensile strength and durability.
-
Types of Hydraulic Presses
- Hydraulic Hot Press Machines: These are specialized hydraulic presses designed for high-temperature applications, such as laminating, molding, and curing composites. They combine hydraulic force with controlled heating to achieve precise results in processes like aerospace component manufacturing.
- C-Frame and H-Frame Presses: These are common designs for smaller to medium-sized hydraulic presses, offering versatility and ease of use for tasks like assembly, punching, and bending.
- Four-Column Presses: These are used for heavy-duty applications, providing stability and uniform force distribution for tasks like forging and deep drawing.
-
Advantages of Hydraulic Presses
- High Force Output: Hydraulic presses can generate significantly higher forces compared to mechanical presses, making them suitable for heavy-duty tasks.
- Precision and Control: The ability to precisely control the force and speed of the press ensures consistent results, which is critical in manufacturing and material testing.
- Versatility: Hydraulic presses can be adapted for a wide range of applications by adjusting pressure, piston size, and tooling.
-
Limitations and Considerations
- Maintenance: Hydraulic systems require regular maintenance to ensure proper functioning, including checking for fluid leaks, maintaining hydraulic fluid quality, and inspecting seals and hoses.
- Energy Efficiency: Hydraulic presses can consume more energy compared to mechanical presses, especially in continuous operation. Advances in hydraulic technology are addressing this issue with more efficient designs.
- Cost: High-capacity hydraulic presses, such as those used in industrial settings, can be expensive to purchase and operate.
-
Hydraulic Hot Press Machines
- These machines are a specialized subset of hydraulic presses, designed for applications requiring both high force and controlled heat. They are commonly used in industries like aerospace, automotive, and electronics for tasks such as laminating composite materials, curing adhesives, and molding high-performance plastics.
- The combination of hydraulic force and precise temperature control makes these machines ideal for producing high-quality, durable components.
In summary, hydraulic presses are among the strongest machines available, capable of generating immense force through the principles of hydraulics. Their strength, precision, and versatility make them indispensable in industries ranging from manufacturing to material testing. For applications requiring both force and heat, hydraulic hot press machines offer a specialized solution, combining hydraulic power with controlled heating to achieve exceptional results.
Summary Table:
Key Aspect | Details |
---|---|
Force Capacity | Ranges from a few tons to over 10,000 tons, depending on piston size and pressure. |
Principle of Operation | Based on Pascal's Law: Force = Pressure × Area. |
Applications | Metal forming, stamping, forging, compression molding, and material testing. |
Types of Presses | Hydraulic Hot Press, C-Frame, H-Frame, and Four-Column Presses. |
Advantages | High force output, precision, control, and versatility. |
Limitations | Requires maintenance, energy efficiency concerns, and higher costs. |
Ready to harness the power of hydraulic presses for your industrial needs? Contact us today to find the perfect solution!