Brazing is a versatile joining process that can be used to bond metal parts of varying thicknesses, typically ranging from thin sheets to thicker sections. The thickness of metal that can be brazed depends on several factors, including the type of metal, the brazing method, the filler material, and the joint design. Generally, brazing is suitable for metals up to several millimeters thick, but with proper techniques, even thicker sections can be joined. The key to successful brazing lies in ensuring proper heat distribution, capillary action, and joint preparation.
Key Points Explained:
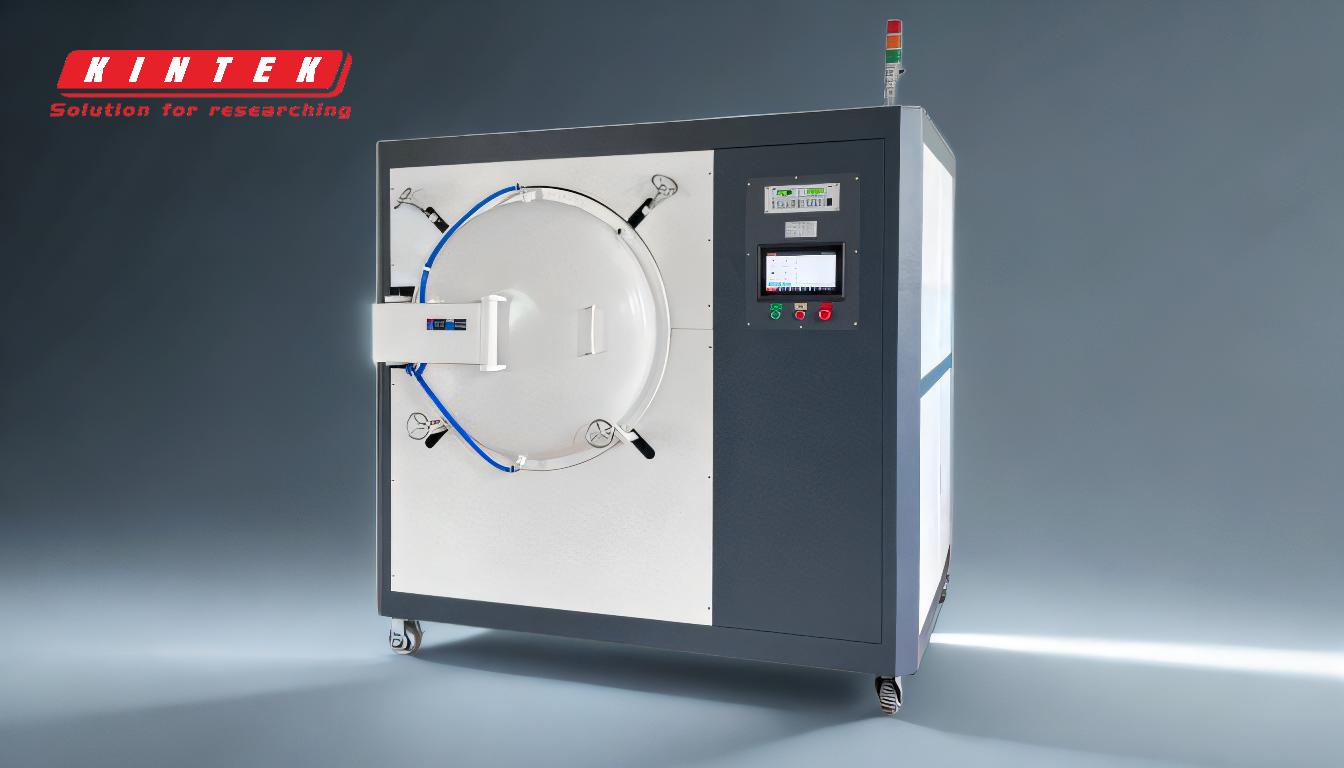
-
Factors Influencing Brazing Thickness:
- Metal Type: Different metals have varying thermal conductivity and melting points, which affect how heat is distributed during brazing. For example, copper and aluminum are easier to braze than stainless steel due to their higher thermal conductivity.
- Joint Design: The design of the joint plays a critical role in determining the maximum thickness that can be brazed. Lap joints and butt joints are commonly used, with lap joints being more effective for thicker materials.
- Filler Material: The choice of filler material must match the base metal and the intended application. Filler materials with lower melting points than the base metal are used to ensure proper bonding without melting the base metal.
- Brazing Method: Techniques such as torch brazing, furnace brazing, and induction brazing have different capabilities in terms of heat control and penetration, which influence the thickness of metal that can be joined.
-
Typical Thickness Range for Brazing:
- Brazing is commonly used for metal thicknesses ranging from 0.5 mm to 6 mm. For thicknesses beyond this range, specialized techniques or preheating may be required.
- Thin sheets (less than 1 mm) require careful heat control to avoid warping or burning.
- Thicker sections (up to 10 mm or more) can be brazed using techniques like furnace brazing or induction brazing, which provide uniform heat distribution.
-
Challenges with Thicker Metals:
- Heat Distribution: Thicker metals require more heat to reach the brazing temperature, which can lead to uneven heating and weak joints if not managed properly.
- Capillary Action: The filler material must flow evenly into the joint. In thicker sections, ensuring proper capillary action can be challenging, especially if the joint gap is too wide or uneven.
- Preheating: For very thick metals, preheating may be necessary to ensure the entire joint reaches the required temperature for brazing.
-
Techniques for Brazing Thicker Metals:
- Furnace Brazing: This method is ideal for thicker metals because it provides uniform heating and can handle large or complex assemblies.
- Induction Brazing: Suitable for localized heating, induction brazing is effective for thicker sections where precise heat control is needed.
- Torch Brazing: While commonly used for thinner metals, torch brazing can be adapted for thicker sections by using multiple torches or preheating.
-
Joint Preparation for Thicker Metals:
- Surface Cleaning: Proper cleaning of the joint surfaces is essential to ensure good wetting and bonding of the filler material.
- Gap Control: Maintaining a consistent joint gap (typically 0.05 mm to 0.2 mm) is critical for capillary action. For thicker metals, the gap may need to be slightly wider to accommodate the filler material.
- Flux Application: Flux is used to prevent oxidation and promote filler flow. For thicker metals, applying flux evenly is crucial to ensure a strong bond.
-
Applications of Brazing Thick Metals:
- Brazing is widely used in industries such as automotive, aerospace, and HVAC for joining thick metal components like heat exchangers, radiators, and structural assemblies.
- The ability to braze thick metals makes it a preferred method for applications requiring high strength and durability.
In conclusion, while brazing is typically used for metals up to 6 mm thick, with the right techniques and joint preparation, it is possible to braze much thicker sections. The key lies in understanding the factors that influence brazing and selecting the appropriate method and materials for the specific application.
Summary Table:
Key Factor | Description |
---|---|
Metal Type | Different metals have varying thermal conductivity and melting points. |
Joint Design | Lap joints are more effective for thicker materials compared to butt joints. |
Filler Material | Must match the base metal and have a lower melting point for proper bonding. |
Brazing Method | Torch, furnace, or induction brazing—each offers unique heat control capabilities. |
Typical Thickness | 0.5 mm to 6 mm, with specialized techniques for thicker sections (up to 10 mm+). |
Challenges | Heat distribution, capillary action, and preheating for thicker metals. |
Techniques | Furnace brazing, induction brazing, and torch brazing for thicker sections. |
Applications | Automotive, aerospace, and HVAC industries for durable, high-strength joints. |
Need help brazing thick metals? Contact our experts today for tailored solutions!