Pressing cast in ceramics involves a series of steps that transform granular or powdery ceramic materials into a solid, geometrically defined shape using pressure. This process can be achieved through methods like slip casting or semi-isostatic pressing, depending on the desired outcome and material properties. The process typically includes preparing the mold, filling it with ceramic slip or powder, applying pressure, and finishing the piece. Hydraulic presses are commonly used to compress ceramics at room temperature, offering a faster alternative to traditional kiln firing. The key to success lies in uniformity of pressure, proper material selection, and adherence to specific fabrication steps.
Key Points Explained:
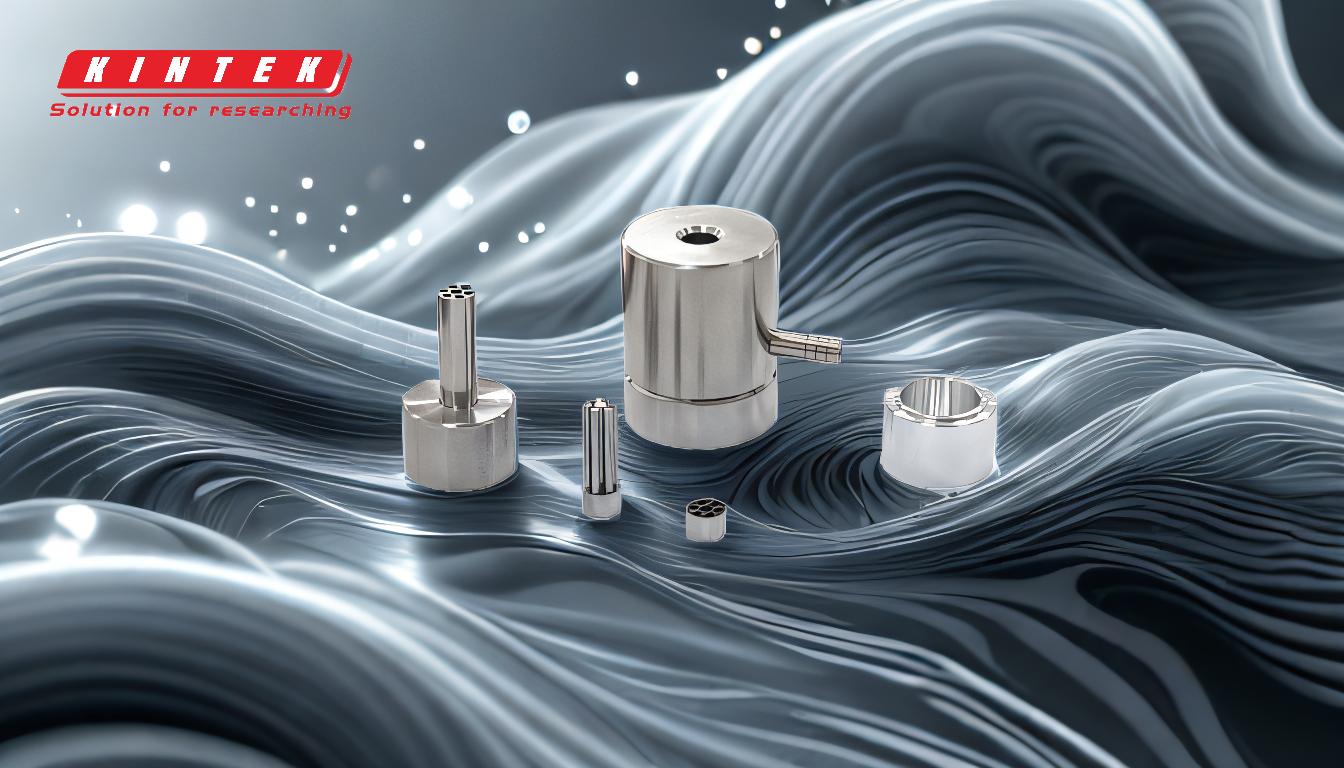
-
Preparation of Mold and Material:
- Mold Setup: Begin by preparing the mold, which can be made of plaster or other materials capable of absorbing moisture. Ensure the mold is clean and free of debris. For slip casting, secure the mold pieces tightly using rubber bands or clamps to prevent leakage.
- Material Selection: Choose the appropriate ceramic material based on the desired properties of the final product. Common materials include leucite-based or lithium disilicate-based ceramics, which are known for their strength and aesthetic qualities.
-
Filling the Mold:
- Slip Casting: For slip casting, slowly pour the ceramic slip (a liquid mixture of clay and water) into the mold until it reaches the top. The plaster mold absorbs the water from the slip, leaving a layer of solid ceramic material against the mold walls.
- Powder Pressing: For powder pressing, fill the mold with granular or powdery ceramic material. Ensure the material is evenly distributed to achieve uniform density in the final product.
-
Applying Pressure:
- Hydraulic Pressing: Use a hydraulic press to apply pressure to the ceramic material. The pressure can be applied isostatically (uniformly from all directions) or axially (from one or more directions). This step compresses the material into a solid body with the desired shape.
- Semi-Isostatic Pressing: This technique ensures uniform pressure distribution, which is crucial for achieving optimized mechanical performance and dimensional accuracy. It is particularly useful for complex shapes and high-performance ceramics.
-
Removing Excess Material:
- Slip Casting: After the slip has set, carefully remove any excess slip from the mold. This step ensures that the final piece has clean edges and a smooth surface.
- Powder Pressing: Excess powder may need to be removed or trimmed after pressing, depending on the mold design and the pressing method used.
-
Releasing the Casting:
- Demolding: Once the ceramic material has sufficiently hardened, carefully release the casting from the mold. For slip casting, this may involve gently tapping the mold to loosen the piece. For pressed ceramics, the mold may need to be disassembled or the piece ejected using a press mechanism.
- Handling: Handle the freshly pressed or cast piece with care to avoid any damage or deformation.
-
Finishing the Piece:
- Trimming and Smoothing: After demolding, trim any rough edges or imperfections using ceramic tools. Smooth the surface as needed to achieve the desired finish.
- Drying and Firing: Allow the piece to dry completely before firing it in a kiln. The firing process will further harden the ceramic and give it its final strength and durability.
- Glazing (Optional): If desired, apply a glaze to the piece before the final firing. Glazing can enhance the appearance and provide additional protection to the ceramic surface.
-
Quality Control:
- Inspection: Inspect the final product for any defects, such as cracks, warping, or uneven surfaces. Ensure that the piece meets the required dimensional tolerances and mechanical properties.
- Testing: Perform any necessary tests to verify the performance of the ceramic piece, such as strength testing or thermal shock resistance.
By following these steps, you can successfully press cast ceramics, whether using slip casting or powder pressing techniques. Each method has its own advantages and is suited to different types of ceramic products, from intricate artistic pieces to high-performance industrial components.
Summary Table:
Step | Details |
---|---|
1. Mold Preparation | Clean and secure the mold; choose the right ceramic material. |
2. Filling the Mold | Use slip casting or powder pressing for uniform distribution. |
3. Applying Pressure | Apply hydraulic or semi-isostatic pressing for optimal compression. |
4. Removing Excess | Trim excess slip or powder for clean edges and smooth surfaces. |
5. Demolding | Carefully release the casting to avoid damage. |
6. Finishing | Trim, dry, fire, and optionally glaze the piece for final strength and look. |
7. Quality Control | Inspect and test for defects, ensuring dimensional and mechanical accuracy. |
Ready to elevate your ceramic fabrication process? Contact us today for expert guidance and solutions!