Induction furnaces primarily operate using alternating current (AC). They utilize an AC solenoid coil to generate an electromagnetic field, which induces eddy currents in the metal to be melted, thereby heating it. The two main types of induction furnaces, coreless and channel-type, both rely on AC for their operation. Coreless furnaces use a water-cooled AC solenoid coil surrounding a crucible, while channel-type furnaces use a loop of molten metal as a single-turn secondary winding through an iron core, also driven by AC. This design ensures efficient and controlled heating for melting metals.
Key Points Explained:
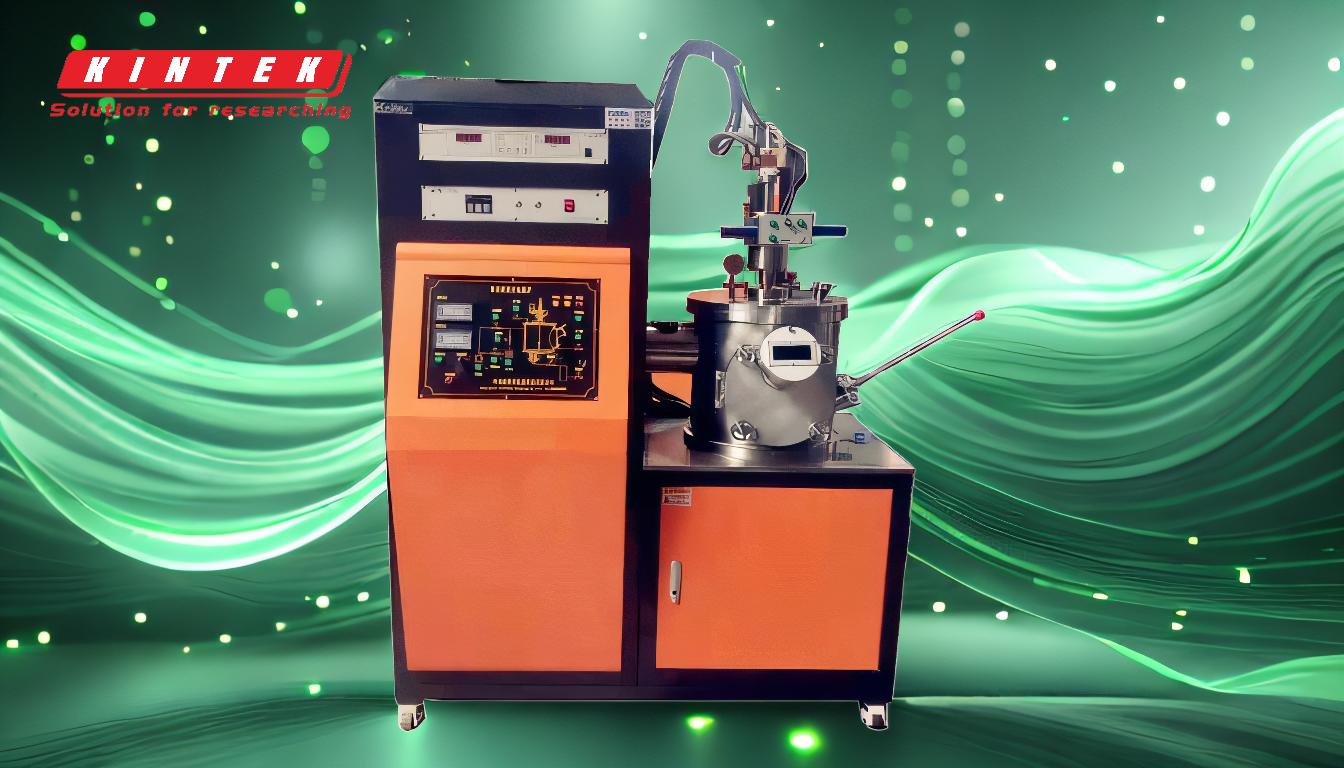
-
Induction Furnaces Use AC, Not DC
- Induction furnaces rely on alternating current (AC) to generate the electromagnetic field required for heating and melting metals. DC is not used because it does not produce the necessary fluctuating magnetic field to induce eddy currents in the metal.
-
Coreless Induction Furnaces
- Coreless induction furnaces use a water-cooled AC solenoid coil surrounding a crucible. The AC current in the coil creates a rapidly alternating magnetic field, which induces eddy currents in the metal placed inside the crucible. These eddy currents generate heat through resistance, melting the metal.
-
Channel-Type Induction Furnaces
- Channel-type induction furnaces operate similarly but use a loop of molten metal as a single-turn secondary winding. The primary AC coil induces current in this molten metal loop, which heats and maintains the metal in a molten state. This design is more efficient for continuous melting processes.
-
Why AC is Essential for Induction Heating
- AC is essential because it creates a changing magnetic field, which is necessary to induce eddy currents in the metal. These eddy currents are responsible for the resistive heating that melts the metal. DC, on the other hand, produces a static magnetic field, which cannot induce eddy currents.
-
Types of Induction Furnaces
- The two main types of induction furnaces are coreless and channel-type. Both types use AC for operation, but they differ in design and application. Coreless furnaces are more versatile for batch melting, while channel-type furnaces are better suited for continuous melting processes.
-
Frequency Considerations
- Induction furnaces can operate at different frequencies, such as main frequency (50-60 Hz) or medium frequency (higher than 60 Hz). The choice of frequency depends on the type of metal being melted and the desired melting efficiency. However, regardless of frequency, the power source remains AC.
-
Advantages of AC in Induction Furnaces
- AC provides precise control over the heating process, allowing for uniform melting and minimal melt losses. It also enables the use of different furnace designs (coreless and channel-type) to suit various industrial applications.
In summary, induction furnaces are AC-powered devices designed to efficiently melt metals using electromagnetic induction. The use of AC is fundamental to their operation, enabling the generation of eddy currents and the subsequent heating of the metal. Whether coreless or channel-type, all induction furnaces rely on AC to achieve their melting capabilities.
Summary Table:
Key Aspect | Details |
---|---|
Power Source | Induction furnaces use AC to generate electromagnetic fields for heating. |
Coreless Furnaces | Water-cooled AC solenoid coil surrounds a crucible for batch melting. |
Channel-Type Furnaces | Molten metal loop acts as a secondary winding, ideal for continuous melting. |
Why AC is Essential | AC creates a fluctuating magnetic field, inducing eddy currents for heating. |
Frequency Options | Operates at main (50-60 Hz) or medium frequencies, depending on application. |
Advantages of AC | Precise control, uniform heating, and minimal melt losses. |
Unlock the power of AC-driven induction furnaces for your metal melting needs—contact our experts today!