Brazing and welding are both effective joining methods, but their strength and suitability depend on the application. Welding typically provides superior strength because it creates a metallurgical bond by melting and mixing the base materials, resulting in a joint that is as strong as or stronger than the parent metals. Brazing, on the other hand, uses a filler material that melts at a lower temperature than the base materials, creating a strong but generally less robust joint compared to welding. While brazing is advantageous for specific applications like small cast iron repairs due to reduced cracking risk and less thermal distortion, it generally offers lower strength and heat resistance than welding.
Key Points Explained:
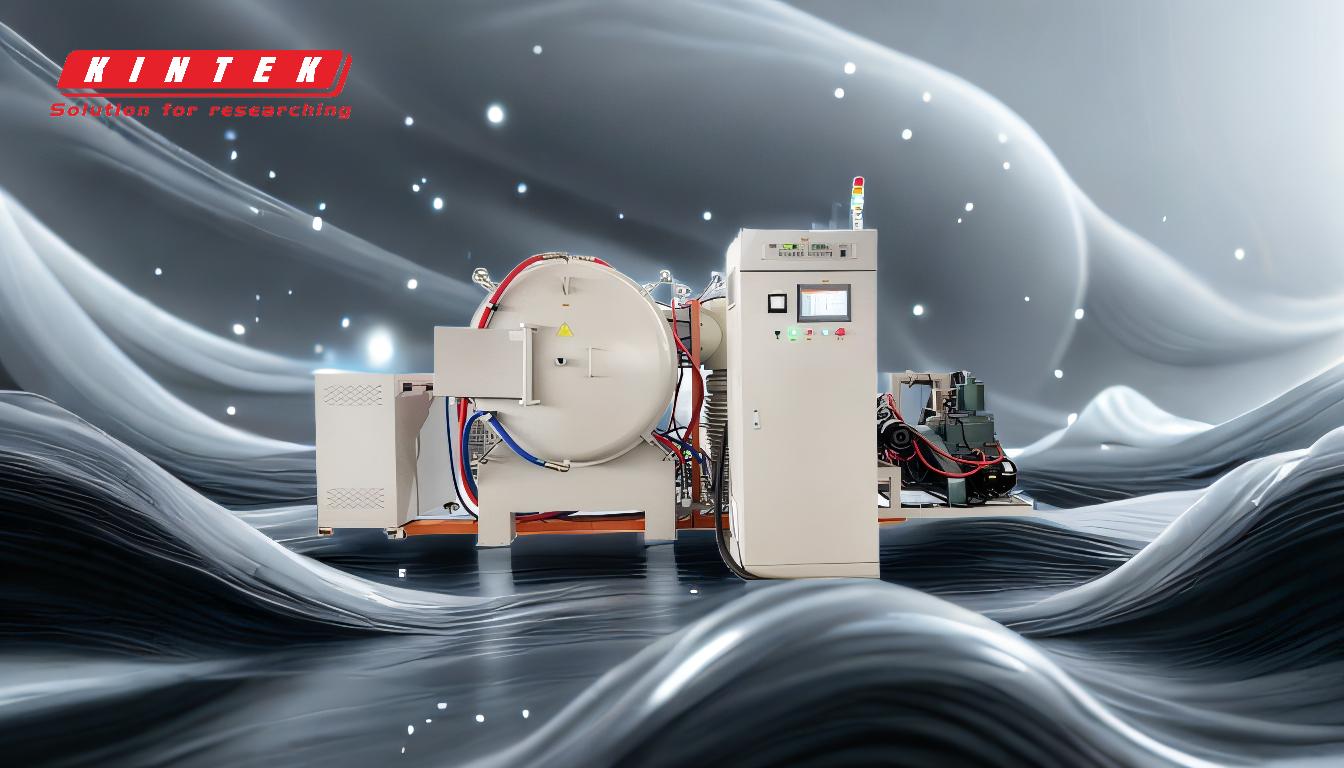
-
Mechanism of Joining:
- Welding: Involves melting the base materials (and sometimes a filler) to form a metallurgical bond. The resulting joint is a mixed alloy, making it as strong as or stronger than the parent materials.
- Brazing: Uses a filler material with a lower melting point than the base materials. The filler flows into the gaps via capillary action and solidifies, creating a durable but less robust joint compared to welding.
-
Strength Comparison:
- Welding generally provides superior strength because it fuses the base materials, creating a joint with strength comparable to or exceeding the parent metals.
- Brazed joints, while strong, are typically less robust than welded joints due to the lower melting point of the filler material and the absence of a metallurgical bond with the base materials.
-
Heat Resistance:
- Welded joints offer significant heat resistance, making them suitable for high-temperature applications.
- Brazed joints have reduced heat resistance compared to welded joints, limiting their use in high-temperature environments.
-
Applications and Advantages:
- Welding: Ideal for applications requiring high strength and heat resistance, such as structural components and high-temperature environments.
- Brazing: Preferred for delicate or small-scale repairs, such as cast iron, where the risk of cracking or metallurgical changes in the heat-affected zone (HAZ) is a concern. It also produces less thermal distortion, making it suitable for precision assemblies.
-
Thermal Distortion:
- Welding can cause localized high temperatures, leading to warping or distortion in the base metal.
- Brazing, especially furnace brazing, uniformly heats the entire assembly, minimizing thermal distortion and making it suitable for precision applications.
In summary, while brazing is a valuable joining method for specific applications, welding generally provides stronger and more heat-resistant joints. The choice between the two depends on the specific requirements of the project, such as strength, heat resistance, and the risk of thermal distortion.
Summary Table:
Aspect | Welding | Brazing |
---|---|---|
Mechanism | Melts base materials to form a metallurgical bond. | Uses a lower-melting filler material that flows into gaps via capillary action. |
Strength | Joint is as strong as or stronger than the parent metals. | Strong but less robust compared to welding. |
Heat Resistance | High heat resistance, suitable for high-temperature applications. | Reduced heat resistance, limiting use in high-temperature environments. |
Applications | Structural components, high-temperature environments. | Delicate repairs (e.g., cast iron), precision assemblies with minimal distortion. |
Thermal Distortion | Can cause warping or distortion due to localized high temperatures. | Minimizes distortion, ideal for precision applications. |
Need help choosing the right joining method for your project? Contact our experts today for personalized advice!