Calcination is a thermal treatment process that involves heating a substance to high temperatures, typically below its melting point, to bring about thermal decomposition, phase transition, or the removal of volatile components. While blast furnaces are widely used for smelting and refining metals, they are not typically used for calcination. Instead, calcination is more commonly performed in specialized high-temperature furnaces designed for precise temperature control and uniformity. These furnaces, such as muffle furnaces or rotary kilns, are better suited for calcination due to their ability to maintain consistent high temperatures and provide controlled environments.
Key Points Explained:
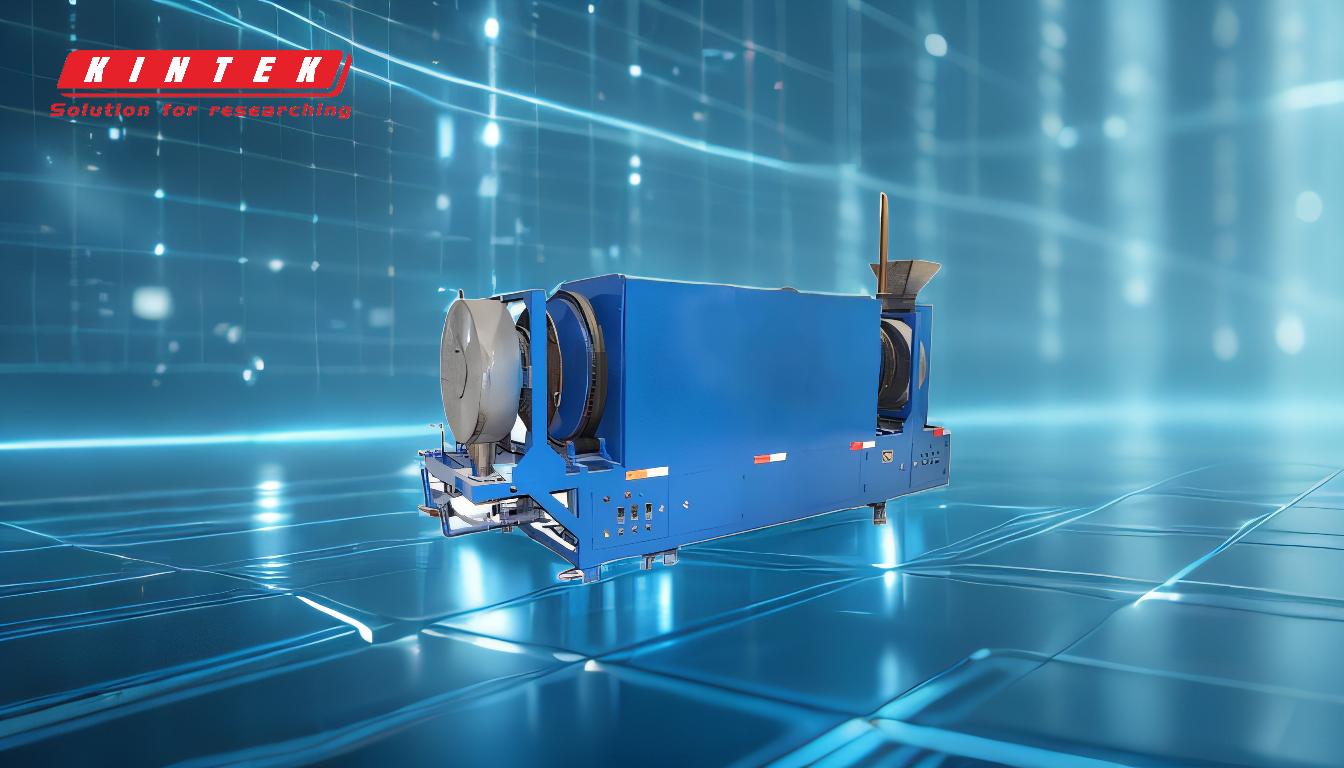
-
What is Calcination?
- Calcination is a thermal process used to decompose materials, remove volatile substances, or induce phase changes. It typically occurs at temperatures below the melting point of the material being processed. Common examples include the decomposition of limestone (CaCO₃) to produce lime (CaO) and the removal of water from gypsum.
-
Blast Furnace vs. High-Temperature Furnace
- Blast Furnace: Primarily used for smelting iron ore to produce pig iron. It operates at extremely high temperatures (up to 2300°C) and is designed for large-scale industrial metal production. The environment inside a blast furnace is not ideal for calcination due to the presence of reducing agents like coke and the lack of precise temperature control.
- High-Temperature Furnace: Specifically designed for processes requiring uniform and controlled high temperatures. These furnaces are equipped with advanced heating elements, such as silicon carbide (SiC), and are used for calcination, sintering, annealing, and other heat treatment processes. They can maintain temperatures up to 1550°C, making them suitable for calcination.
-
Why Calcination is Not Done in Blast Furnaces
- Calcination requires a controlled environment with precise temperature regulation, which blast furnaces cannot provide. Blast furnaces are optimized for reducing ores and producing molten metal, not for the delicate thermal decomposition processes involved in calcination.
- The presence of reducing agents like coke in blast furnaces can interfere with calcination reactions, leading to undesirable chemical changes in the material being processed.
-
Applications of High-Temperature Furnaces in Calcination
- High-temperature furnaces are widely used for calcination in industries such as ceramics, metallurgy, and chemical processing. For example:
- Ceramics: Used to remove organic binders and decompose raw materials like kaolin to produce alumina.
- Metallurgy: Employed for the calcination of ores and concentrates to remove volatile impurities.
- Chemical Industry: Utilized for the thermal decomposition of compounds like calcium carbonate or magnesium carbonate.
- High-temperature furnaces are widely used for calcination in industries such as ceramics, metallurgy, and chemical processing. For example:
-
Advantages of Using High-Temperature Furnaces for Calcination
- Temperature Uniformity: Ensures consistent heating throughout the material, which is critical for achieving the desired chemical or physical changes.
- Precision Control: Allows for accurate regulation of temperature and heating rates, reducing the risk of over- or under-processing.
- Versatility: Suitable for a wide range of materials and processes, including sintering, annealing, and organic curing.
-
Examples of High-Temperature Furnaces
- Muffle Furnace: Ideal for calcination due to its enclosed design, which prevents contamination and ensures uniform heating.
- Rotary Kiln: Commonly used for continuous calcination processes, such as in cement production or the decomposition of limestone.
In conclusion, while blast furnaces are essential for metal smelting, they are not suitable for calcination. High-temperature furnaces, with their precise temperature control and uniform heating capabilities, are the preferred choice for calcination processes across various industries.
Summary Table:
Aspect | Blast Furnace | High-Temperature Furnace |
---|---|---|
Primary Use | Smelting and refining metals | Calcination, sintering, annealing |
Temperature Control | Limited precision | Precise and uniform |
Environment | Reducing agents (e.g., coke) interfere | Controlled, contamination-free |
Applications | Metal production | Ceramics, metallurgy, chemical processing |
Examples | Iron ore smelting | Muffle furnace, rotary kiln |
Discover the best furnace for your calcination needs—contact our experts today!