Diamond coatings are known for their exceptional hardness, wear resistance, and durability, making them highly desirable for various industrial and scientific applications. However, whether a diamond coating is permanent depends on several factors, including the application environment, the quality of the coating, and the substrate material. While diamond coatings are extremely durable and resistant to wear, they are not indestructible and can degrade under certain conditions, such as extreme mechanical stress, high temperatures, or chemical exposure. The permanence of a diamond coating is thus relative and context-dependent.
Key Points Explained:
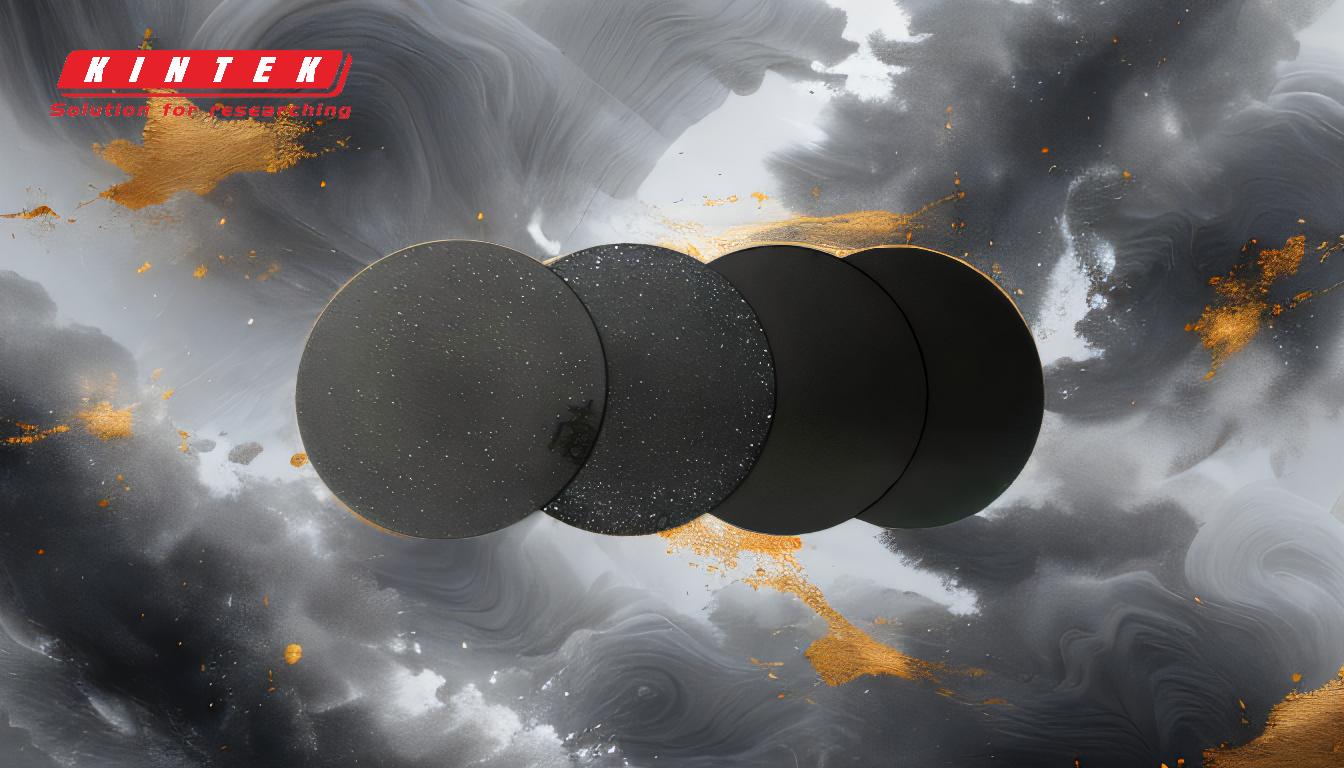
-
Properties of Diamond Coatings:
- Diamond coatings are renowned for their high hardness, which makes them resistant to scratches and wear.
- They exhibit excellent thermal conductivity, allowing them to dissipate heat efficiently.
- Diamond coatings are chemically inert, meaning they resist reactions with most chemicals, enhancing their durability in harsh environments.
- Their mechanical, electrical, optical, and thermal properties make them suitable for a wide range of applications, from cutting tools to electronic devices.
-
Factors Influencing Permanence:
- Deposition Quality: The permanence of a diamond coating depends on how well it is deposited onto the substrate. Factors like grain size, surface roughness, and crystallinity can be controlled during the deposition process to optimize durability.
- Substrate Material: The material onto which the diamond coating is applied plays a significant role. A strong bond between the coating and the substrate ensures better adhesion and longevity.
-
Application Environment: Diamond coatings are not immune to degradation under extreme conditions. For example:
- Mechanical Stress: Prolonged exposure to high friction or impact can wear down the coating.
- High Temperatures: While diamond has excellent thermal conductivity, excessive heat can affect the coating's integrity.
- Chemical Exposure: Although chemically inert, certain aggressive chemicals or environments can still cause degradation over time.
-
Limitations of Diamond Coatings:
- Not Indestructible: Despite their hardness, diamond coatings can chip, crack, or delaminate under extreme conditions.
- Cost and Complexity: High-quality diamond coatings require precise deposition techniques, which can be expensive and complex, limiting their use in some applications.
- Substrate Compatibility: Not all materials can effectively bond with diamond coatings, which may reduce their effectiveness or permanence in certain applications.
-
Applications and Longevity:
- In cutting tools, diamond coatings significantly extend tool life due to their wear resistance, but they are not permanent and will eventually wear out with heavy use.
- In electronic devices, diamond coatings can provide long-lasting thermal management, but their permanence depends on the operating conditions.
- In optical applications, diamond coatings can maintain their properties for extended periods, but they may degrade if exposed to harsh environments.
In conclusion, while diamond coatings are highly durable and resistant to wear, they are not permanent in the absolute sense. Their longevity depends on the quality of the coating, the substrate material, and the conditions under which they are used. For equipment and consumable purchasers, understanding these factors is crucial when selecting diamond-coated products to ensure they meet the specific requirements of the intended application.
Summary Table:
Aspect | Details |
---|---|
Properties | High hardness, wear resistance, thermal conductivity, chemical inertness |
Factors Affecting Permanence | Deposition quality, substrate material, application environment |
Limitations | Not indestructible, high cost, substrate compatibility issues |
Applications | Cutting tools, electronic devices, optical applications |
Learn more about diamond coatings and their applications—contact our experts today!