Yes, induction hardening is indeed a heat treatment process. It is a specialized form of heat treatment that focuses on hardening the surface of a metal part, typically made of steel or cast iron, through the application of induction heating followed by rapid quenching. This process selectively heats the surface of the workpiece using electromagnetic induction, which generates localized heat due to eddy currents. The heated surface is then rapidly cooled, typically using a quenching medium, to achieve the desired hardness and wear resistance. Induction hardening is particularly advantageous for applications requiring localized hardening, as it allows specific areas of a part to be hardened without affecting the entire component.
Key Points Explained:
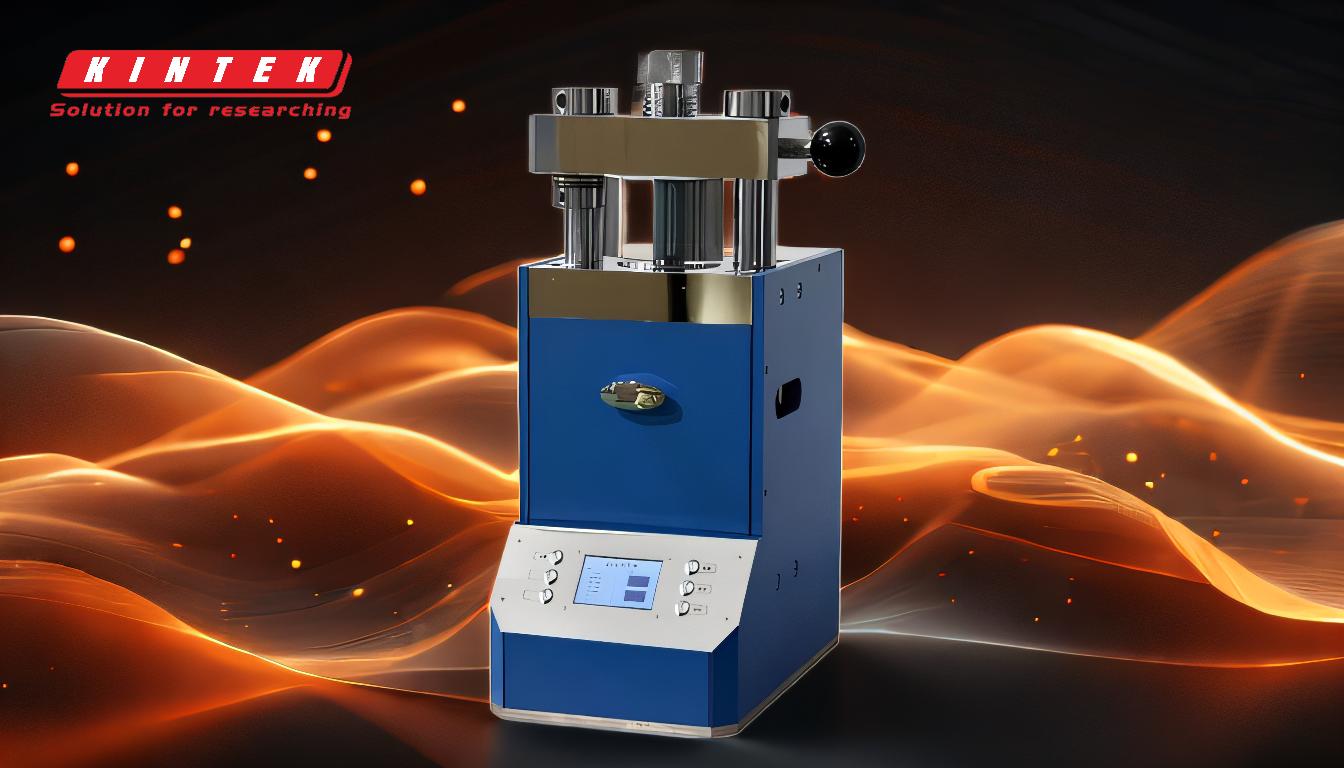
-
Definition of Induction Hardening:
- Induction hardening is a heat treatment process that uses electromagnetic induction to heat the surface of a metal part, followed by rapid quenching to increase its hardness and wear resistance.
- It is specifically designed for materials like steel and cast iron, where surface hardness is critical for performance.
-
How Induction Hardening Works:
- The process involves placing the workpiece inside an inductor (coil) and passing a high-frequency alternating current through the coil.
- The alternating current generates an alternating magnetic field, which induces eddy currents in the workpiece.
- Due to the skin effect, the eddy currents are concentrated on the surface of the workpiece, causing rapid heating of the surface layer.
- Once the surface temperature exceeds the critical point (typically the austenitizing temperature for steel), the workpiece is rapidly cooled (quenched) to achieve surface hardening.
-
Advantages of Induction Hardening:
- Localized Hardening: Induction hardening allows specific areas of a part to be hardened without affecting the entire component. This is particularly useful for parts that require wear resistance in specific regions.
- Efficiency: The process is faster and more energy-efficient compared to traditional case-hardening methods, as it directly heats the surface rather than the entire part.
- Suitability for Large Parts: Induction hardening can be applied to large parts, making it versatile for a wide range of industrial applications.
- Minimal Distortion: Since the heat is localized, there is minimal distortion or warping of the part, which is a common issue in other heat treatment processes.
-
Comparison to Other Heat Treatment Processes:
- Unlike traditional heat treatment methods that heat the entire part, induction hardening selectively heats the surface, making it more efficient and precise.
- It is often compared to case hardening, but induction hardening is faster and does not require the use of chemical treatments or prolonged heating cycles.
-
Applications of Induction Hardening:
- Induction hardening is widely used in industries where wear resistance and surface hardness are critical, such as automotive, aerospace, and machinery manufacturing.
- Common applications include gears, shafts, bearings, and other components that require high surface hardness to withstand friction and wear.
-
Limitations of Induction Hardening:
- The process is primarily effective for surface hardening and may not be suitable for applications requiring uniform hardness throughout the part.
- It requires specialized equipment, such as induction coils and high-frequency power supplies, which can be costly.
In summary, induction hardening is a specialized heat treatment process that provides localized surface hardening through the use of electromagnetic induction and rapid quenching. Its efficiency, precision, and ability to selectively harden specific areas make it a valuable technique in various industrial applications.
Summary Table:
Key Aspect | Details |
---|---|
Definition | A heat treatment process using electromagnetic induction for surface hardening. |
How It Works | High-frequency alternating current heats the surface, followed by quenching. |
Advantages | Localized hardening, energy efficiency, minimal distortion, and versatility. |
Applications | Gears, shafts, bearings, and components requiring high surface hardness. |
Limitations | Primarily for surface hardening; requires specialized, costly equipment. |
Want to learn more about induction hardening for your industrial needs? Contact our experts today!